Social Distancing w/ Kevin Roche
MEMIC Safety Experts - Podcast készítő Peter Koch - Hétfők
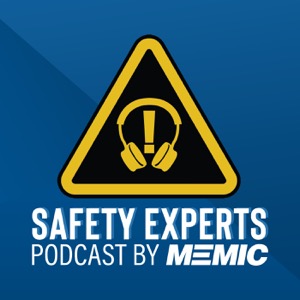
Kategóriák:
Many of us haven’t heard of the term until the current novel coronavirus pandemic. However, this isn’t a new tool at all. Studies back in the early 2000’s and late 1900’s discuss physical distancing as one of the main community mitigation measures recommended during influenza pandemics. On this Episode of the MEMIC Safety Experts Podcast, Pete talks with Kevin Roche, CEO of EcoMaine a non-profit waste management organization serving a third of Maine’s population. Together, they explore the decision EcoMaine made to begin physical distancing early on in the novel coronavirus pandemic, what impacts it has had on their team and business plan, and leadership that made a difference. Peter Koch: Hello listeners, and welcome to the MEMIC Safety Experts podcast. Some say absence makes the heart grow fonder. And while this may be true, in some cases, the current situation certainly calls for us to be separated. And I can say that physical distancing is making me more aware of what we lose when we can't be face to face. However, social or physical distancing is a reality now and a good tool to limit the spread of any disease in the workplace. And that's not a new phenomena. There have been studies showing that physical distancing is one of the community mitigation measures recommended by the CDC during any influenza pandemic. That said, many of us haven't even heard of the term until the current novel coronavirus pandemic. However, we have all participated in physical distancing in one form or another over the years. Some of us were kept at home from school and we got sick or stayed at home from work due to illness or decided not to go to an event because we were ill or the host canceled due to illness. All examples [00:01:00] of physical distancing, and if that was never your experience, I expect that you've decided to keep yourself distant from someone who is coughing or sneezing during cold and flu season. So regardless of how or why you did it, someone maybe even you made the decision to keep yourself distant from someone else in order to prevent the spread of germs. Well, I'm your host, Peter Kotch. And on the phone today with me is Kevin Roche, CEO of Ecomaine, a non-profit waste management organization serving a third of Maine's population and more than 70 member communities. Kevin and I are going to explore the decision that Ecomaine made to begin social distancing and what impacts that it has had on their team and the business plan. Kevin, welcome to the podcast today. Kevin Roche: Thank you, Peter. Peter Koch: Great. And it's really great to have you on the line and giving us some time today to talk about the decision that you made for physical distancing. And I think it's a very apropos topic for the time that we're in. But before we get into that, why don't you [00:02:00] tell me a little bit about yourself and an Ecomaine so that our listeners get a little bit more of an idea about what Ecomaine is and what they do. Kevin Roche: Sure, Peter. I think our mission statement really describes us best, and that is Ecomaine provides comprehensive long term, solid waste solutions in a safe, environmentally responsible and economically sound manner and is a leader in raising public awareness of sustainable waste management strategies. So we have several facilities to help us manage the waste and recyclable materials that are collected from our member communities. And there's over 70 of those member communities, as you pointed out. So we have a recycling single salt recycling facility that processes all the recyclable materials boughs that material up and sends it off to market. And then we have a waste energy facility that takes in all of the non-recyclable waste burns. That waste generates steam, then generates power, electricity, and then we sell that electricity to [00:03:00] the grid. We also have a landfill to dispose of the ash from the waste energy facility. And we also have a food waste recovery program where we send it to an anaerobic digester for energy recovery of the food waste and then to support all of that infrastructure. We have an aggressive public relations and outreach program whereby we provide tours, classroom presentations, online education to our member communities so that we get really, really good compliance and participation from the residents and businesses in our communities. Peter Koch: You got a lot going on there, it's more than just a place where you bring trash to, there's a bunch happening and I bet you the complexity of the systems to make sure that everything functions correctly and keeps going really requires quite a few people, quite a bit of technology to make it all happen, which [00:04:00] I think it can be pretty challenging to keep going, especially during times of crisis. Kevin Roche: That's correct. And, you know, I’ve been in the industry for about 30 years. And, you know, when we were first faced with this crisis, the one thing that I knew was that we needed to continue offering these services to our member communities because we didn't want this crisis to lead to another health crisis whereby the trash would be backed up at our hospitals and our restaurants, at our medical facilities and even at our households. We knew we had to find a way to keep the trash moving out of the homes, out of the businesses, out of the hospitals and be processed in an environmentally and safe manner. Peter Koch: Yeah. And I imagine that would have been a pretty challenging thing as you're watching the news and sort of seeing the world get smaller and smaller because the pandemic got larger and larger and [00:05:00] we were thinking about shutting businesses down. You were thinking, how do we keep this going? Because like you said, you never really think about trash as an essential business or trash collection as an essential business. But when it doesn't get picked up or it doesn't happen, whether it be on the day that it's supposed to happen or maybe for weeks, it can be a pretty significant not just inconvenience, but I think you hit the nail on the head. It can be a public health emergency as well. So that was great forward thinking on your part as you started to look at the potential impact that would be happening with the current crisis. So that was the prompting, I guess that Ecomaine needed to do something. But why did you choose the physical distancing as a policy to try to put into place? Kevin Roche: Sure. So with the understanding that we needed to find a way to continue our operations through this crisis and [00:06:00] you know, at that time we had no idea how big this crisis was and how long it was going to last. But it appeared that it was here and it appeared that we you know, we needed to make some changes in the way we operated. So early on, you know, we started making calls. And, you know, when the city had their first crisis right there at city hall, you know, I spoke to the city manager, I spoke to the county. And I also spoke to the CDC. And my question to them is, look, you know, we're an essential service. We need to continue operations. What are the tools that we could employ to ensure that we can continue to operate during this crisis? And so they gave me, you know, all of those resources really gave me a whole laundry list of things that we could do. Some of them were things that I really couldn't employ here at Ecomaine because they [00:07:00] just you know, they really weren't either they didn't make sense for our operation or we were already doing those taking those measures. But the ones thing, it was almost at the end of a call kind of thing. One of those conversations was that, well, you know what you could do if you want to ensure that you can continue to operate and you didn't lose your entire staff because you had a positive test for the coronavirus. One of the things that you could do is you could practice physical distancing. And at that time, this was early on the physical distancing and the recommendation was three feet. Now, the CDC, you know, had had moved to six feet shortly thereafter and we adopted the six feet. But our first requirement was to keep all of our employees separated by three feet. And that went with, you know, our contractors and customers, too. And then what really was the game changer for us was [00:08:00] that we started documenting every one of those close encounters that were within three feet. And then, of course, as I mentioned, it went to six feet. So every single employee had to document write it down, report it. on this form that we had formatted every single six-foot close encounter that lasted for more than 10 seconds. And to me, that was the game changer for us because it did two things. It provided for self-awareness of the close encounter that every employee was experiencing throughout the workday. And then secondly, provided a way to Correct The issue so that these close encounter forms went to the supervisor and the supervisor and the manager discussed, OK, how can we eliminate those close encounters the next day? And so they came up with strategies to engineer ways to eliminate those close encounters. And then finally, [00:09:00] the final benefit is if we did have a positive test result, then we could go back and easily trace who's been exposed to who. So that we didn't lose the whole organization, that we could just quarantine those that had the exposure that, you know, require that quarantine to be employed. Peter Koch: That's an all-encompassing plan that you have there. I do want to talk about the encounter tracking for sure, but I want to back you up just a little bit. And let's talk about the policy for physical distancing itself. How did you roll that out? Like how did that once you determine this had to happen, what did you need to do to make sure that you had proper knowledge within the workplace and that you had some buy-in? Because I can imagine that if you just put a couple of signs up there and put it in a memo and said, you guys, like you all got to stay three feet or more than three feet apart, that there would have been a lot of smiles and nods and it might not have happened the way you needed it to. But really, the stakes were pretty high here. [00:10:00] If you couldn't do this. You might not have been able to maintain business throughout the crisis. So how did you implement the policy to start with? Kevin Roche: Right. And that's a key point. You know, this is 100 percent leadership, leadership, leadership. And I needed my managers and supervisors to buy into this going forward, because at that time, early on, you know, there were still you know, there's still a split out there as to how real and how serious this thing was. And so, you know, I what I asked for is, hey, look, we all have our opinions on where this is going, where this crisis is going, and really that the foundation behind this crisis. And I said, we're not here to argue about that. We're not the health experts. We manage waste and recyclable materials. That's our expertise. You know, what I told my team was that we need to listen to the health experts. They have told us that [00:11:00] physical distancing will be, should be a priority and will be the most effective way to reduce transmission of this disease. And so we had to accept that. We had to accept that advice from the health professionals, in particular from the CDC. And so that going forward, that kind of created or almost mandated buy-in the of the current circumstances and then how we were going to deal with those circumstances. So, you know, we laid out the requirements for physical distancing and it had to happen every day, every hour with every single employee, including myself. So I started filling out the forms, every single interaction. You know, I had to record. And that made again, that self awareness piece was so critical because it made me think about, OK, geez, you know, I came into this contact with this other employee. How can I reduce that next [00:12:00] time? And so, you know, habits are hard to break. And so the documentation forced the habit to change. And that's why the documentation behind this was so critical and making this effort successful. And so you can't let your guard down for one moment. So we started recording this information into a spreadsheet and then created the summary. And so I got to report each day that showed me how many close encounters we had and we started color coding them. You know, we had greens, yellows and reds. And the idea was to change the reds, those long duration close encounters and get them to yellow and get the yellows into the green category. And so the minute you let your guard down, you know that one person doesn't fill out their form and doesn't turn it in. Then you begin to lose participation and compliance, you [00:13:00] know, with this effort. So we haven't you know, we're a month into this. Now, we haven't let our guard down. We actually started this on the 18th of March, you know, so we're almost a month into this now. And each and every day we basically fill in the holes. And if there's any missing forms, we go out searching to make sure that every employee is filling out a form every single day. Peter Koch: Well, it's a lot to take to take in and to take care of. So you were talking about color coding and obviously the greens were good yellows were for a shorter period time, but longer than you would want. And then the Reds. Were a longer period of time. How did you when you looked at the red ones that you wanted to manage? What was the process by which you went through to try to put something in place so that that wouldn't happen again? So you had an encounter that was closer than six feet and it lasted for quite a long time or a longer time that you wanted [00:14:00] it to be. What process did you go through to troubleshoot that and to put a plan in place for it. Kevin Roche: So, you know, firstly, we asked the supervisors, OK, those areas that are coded in red, you know, find a solution to eliminate the reds and move them to yellows or even better yet, greens. And so that was kind of the first line of defense to find that corrective measure that would make that happen if they continued it then moved from the supervisory level to the managerial level. So then the managers would look at it and say, OK, we're not moving this red area to yellow. So they would look for ways to correct the situation. And then if that wasn't correcting itself, then it went to senior management and myself to determine, OK, what needs to be done, how can we fix this problem? And there were some situations where we found it very difficult to move [00:15:00] out of the red category. So we had to find another solution. And so in those areas, we were somewhat fortunate in that we already had met. Many of us, including myself, are already fitted annually for half face respirator. So we had a lot of the equipment that perhaps not everybody has so that if we had to operate within a certain area within that six feet for an extended period of time, we put the tools in place, the PPE, personal protective equipment to ensure the safety of our employees. And that included masks, that included Tyvek suits, that included goggles, everything, you know, that would be required as far as PPE goes to ensure the safety of our employees. But first and foremost, even before we got to that level, we wanted to find ways to keep our employees separated. And it was amazing that that really was the solution that usually could be found with thinking outside [00:16:00] of the box and finding a way to separate those employees. Peter Koch: So that's a great tool Is engaging the supervisors to come up with the solution. Like you've identified that there's a problem you want that problem. You realize the gravity of the problem and the supervisors are bought in. And the tracking form, like you said, really helps with that awareness. And to identify that there is a challenge here, like we understand that there is a health problem going on. One of the solutions is physical distancing. Here's those places where we can't make physical distancing happen. So how long are they lasting? How often are they lasting? Great awareness tool and then engaging the supervisor to come up with an elimination or an engineering problem. And it's great that you didn't dive right into PPE as the solution that you actually looked at other ways to manage that first before you went to the PPE answer because PPE is not always the best. Like you said, you had to be fitted for the respirator. It's [00:17:00] got to work. It's got to be maintained. There's a lot of other challenges there and it sounds like your supervisors and managers were fairly successful in coming up with out of the box solutions to still get the job done, still maintain good productivity and workflow while keeping the encounters to a minimum. Kevin Roche: That's right. That's right. And they did an excellent job because they were focused on. It was a priority it is our number one priority. So, you know, they really had that keen focus. And this element, what they were able to do is they were able to look at the lines. You know, we have these sorting lines where we sort a lot of the material that's coming in and separate those employees by at least, again, six feet. some of the problem areas actually were the lunch room and the locker room. And so simply by staging lunches and moving people around [00:18:00] a little bit and changing the punching in and punching out so that people weren't lined up at the time clock, those kind of things were simple solutions to keep people apart. One of the other things that we have done is we've provided for a company sponsored lunch so that employees weren't having to leave for lunch and go to the store to get their lunch or go to the convenience store to get their lunch or, you know, early on when restaurants were still open. You know, go to one of the restaurants or takeout. They could stay right on site, but still they would take a box lunch, staying six feet apart and then take that lunch to their own space. Whether it was their own car was whether it was a picnic table that was outside on the warmer days anyway, or that that space in the cafeteria that we kept people six feet apart or maybe their own office. So that was an easy solution in that coming together at the beginning and [00:19:00] the ending of the day and the lunch period, the lunch breaks. Those were some of the problem spots that we had to change the way we normally did business. Peter Koch: And those were identified, those problem spots were identified through the tracking form is that how they were really identified that this would be a problem spot for you. Kevin Roche: Yes. They really were you know, people don't think about the locker room, you know, and you practice physical distancing all day long and then you're coming together and you're changing your boots, you know, in order to go home. And you're sitting three feet away from, you know, your co-worker. So, you know, yeah, those areas kind of came up on the tracking form and enabled us to formulate ways to mitigate that. Peter Koch: It's just another way that that tracking form really helped it didn't just identify where were the areas on the work line were, but some of those places where you wouldn't actually think of or you might not think of until it's too late. Because if you hadn't [00:20:00] identified those right off, those would have been the places where you probably would have had some sort of transmission and you might have lost the whole plant if you hadn't identify those areas. Kevin Roche: That's correct. Yep. And I've shared this with a lot of colleagues and friends. And it only works if somebody is looking at the data every single day and responding to that data and filling in the holes. You know, those forms that aren't turned in, if you let this self manage, it doesn't work because the minute somebody thinks that nobody's really, you know, taking this serious or really responding to the issues that are raised, you know, I think you lose. You know, you lose your base. So the only way that this works is if you're committed to it. You review it every single day and you respond on a daily basis. Peter Koch: And I know you touched on this earlier, but can you talk a little bit more about the specifics of how [00:21:00] you reviewed the data, like who reviews it? What's the process for response? How do you manage those areas that you deem to be challenged? Kevin Roche: Well, because we have so many eyes looking at these close contact form, six-foot close encounter forms, starting with the supervisor and then going to the manager and then going to senior leadership, including myself. We have a lot of areas that, you know, corrections are being made and, you know, we're asking the questions. OK. You know, if there's some reds there, what was done? And, you know, it wasn't acceptable. The status quo was not acceptable. And like you point out, throwing PPE at it is, you know, may or may not be the best solution. And so it's really important to have all supervisory staff on board. And your middle managers as well as your senior managers [00:22:00] on board with this so that everybody is working as a team to correct the situation. And then everybody in the organization knows that this is a priority for everyone and that's when everybody begins to buy in and takes it seriously. And then, you know, again, you can't let a great day go by where you miss, you know this Information you don't pay attention to these data points that you're collecting because, you know, again, if you're not responding to your problem areas, then you're really not giving this a fair shot. Peter Koch: Right. And responding appropriately, I keep going back to that. The PPE example, and I just had this vision in your head when you're talking about PPE again. If PPE was the solution that you threw at the lunchroom or the brake area, that would be just a weird experience to go into the break room where everyone had to wear their PPE to eat, to be with each other. And that would that'd be the solution? Right. So if that was the that was the solution that you came up with to manage the close encounters [00:23:00] in the break room or the locker room, it just wouldn't function. So thinking out of the box sometimes and looking at it from a how do I eliminate it? How do I engineer it. What are the administrative controls that can be in place to help me here before we put PPE in place? I think that's an important lesson for people to learn with this, because many times when you think about what's been in the news, we've been talking about masks. I think for the last four weeks here. And are they functional for the public? Are they functional for workers? We know they're functional for healthcare workers. But why are they functional? How are they functional? So there's a lot of questions about how effective PPE can really be. And I think the thing to consider is that PPE, it still puts you in the line of exposure, the hazards still there, the exposure is still there. And what you're trying to do is trying to eliminate that exposure or at least engineer or administrate the potential [00:24:00] for exposure there. So good lesson to learn and really nice to see that you're thinking so far outside the box, providing box lunches to keeping people away, changing the sorting line, changing different how brakes are taken and probably how some shifts are managed within the facility too. Kevin Roche: That's right. Yep. Peter Koch: Nice. What other things did you have to put in place to make this successful? Because it certainly here's the encounter piece. Like we're trying to keep people away. But then people leave. They go home. They go to they need to do the things that they've been doing at home. At home. How did you manage sick employees? Did you mind talking about that a little bit? Kevin Roche: Sure. Another measure that we put in place early on was that we provided an additional 40 hours of sick time to all employees to ensure that sick employees stayed home or, [00:25:00] you know, employees that were having issues, you know, would stay away from the workplace because we knew we had to keep our workplace healthy and we needed that healthy base to keep our operations going. And so more than ever, we couldn't have people who were obviously exposed to the coronavirus at the workplace or people who were, you know, had a bad cold or even a mild cold here at the workplace, because we really want to ensure that we stayed healthy so that 40 hours allowed us to encourage people to stay home. They were sick and also allowed us to send people home that appeared to be sick. And so, you know, every workplace has those people who come to work, no matter what. You know, they are just so dedicated. It doesn't matter if they're sick or if they got a cold or if they had a flu. They show up every hour of every day. [00:26:00] So this allowed us to send some of those people who were obviously ill home and then keep them home until they had recovered. What this also allowed us to do is people early on who were traveling, you know, we didn't know, you know, this whole thing. I believe it started from travel. And so people who had been traveling were on vacation or dealing with loved ones or whatever they were doing when they returned. This allowed us to keep those people at home and quarantine them until we knew that it was safe for them to come back to work. So everybody in this also kind of served as an equity issue because everybody received it. So that allowed the healthy employees to keep coming back to work. And it also allowed the people who were not healthy or were sick to take care of themselves or take care of their dependents and not return until they were ready. So that was one other [00:27:00] measure that we took that I think was quite effective. And then, of course, you know, we did what just about every other workplace did as we looked at who could work from home and provided accommodations for that to happen. Unfortunately, when we looked at that in the industry that we are in, we couldn't send the garbage home and we couldn't send the recycling home. So a lot of our work had to be done here at our facilities. But there were some people who definitely could do their work from home and those we did we sent those folks home to do their work. Kevin Roche: So that's great another strategic way to look at the business and to determine. So if this business is truly essential and we're all behind this and we're providing a service, if this business goes down, we're going to affect more than just the people who are working for us. It's going to be a broader impact. So we need to put some things in place and looking at it strategically. So who can work from [00:28:00] home? When did they do that? And who can't work from home? And then how do we protect them here and the additional 40 hours of sick time? It is a great way to help people feel comfortable to stay home when they feel ill so that they can contribute to the success of the company in that way. So again, great way of thinking outside the box to try to ensure the health and safety of the workers who are here. Let me ask you this. Kevin, do you see any of these practices, whether it's physical distancing or whether it is the box lunch policy or any of that? You see it occurring again at some point in time. We are going to get on the backside of this at some point in time and the virus will be contained and controlled and we'll have a more normal workplace. But do you see any of your policies and procedures being able to be implemented again in the future, or is this just a one time one and done? We're not going to have to deal with this again. Kevin Roche: Yeah. No. This [00:29:00] you know, this experience has been enlightening for me. And the way I manage and, you know, really gives you a better pathway forward and can allow us to react even more quickly next time. You know, we you know, we didn't have this blueprint in front of us. And you know, that first two weeks I mean, this became my full time focus and to some extent it still is. But, you know, it was you know, I was calling, you know, everybody I possibly could to see what we needed to do. And, you know, one of the, I think, real benefits or opportunities that I had was, you know, I could not do this myself. I needed everybody to come on board with this. And I needed that buy-in. I had an opportunity. Dr. Shah was on main calling and, you know, the CDC early on. Well, you know, I think probably was overwhelmed with the number of calls and inquiries [00:30:00] that they were getting and the concerns that they were getting. And so I had the opportunity to call in, talk to Dr. Shah about the provisions and the measures that we were taking. And I actually asked him the question. I said, you know, the one thing that's missing for me is we're doing You know, we're documenting every single close encounter at the recommendation of the county and the CDC. But what's the duration of these six foot close encounters? I mean, are we talking seconds if you pass somebody by in the hallway? Is that what I should be concerned with? And what about surfaces? You know, there's a lot of issues out there with touching surfaces. And, you know, his response to that was really reassuring. And we recorded that segment so that I could convince my employees that this is the top health expert in the state. And he had one of his comments was that that our measures were exemplary. Those [00:31:00] are his words in containing, you know, this issue that we were faced with. And in the workplace. And so that really, I think was convincing to a lot of our workers here that, you know, we had, you know, the top health expert in the state really signing off on some of the measures that were taking place. Was it perfect? No. Did it take some time to roll out? Yes. Did it take some time to change habits? Yes. But, you know, over the last month, we're still operating. We have a healthy workforce and we've lost very few people due to sickness. Peter Koch: That's great. And it's really good to be able to have well, to have your plan reviewed like that and have had the top health expert give you those marks. That's fantastic and great, great opportunity for buy-in for your staff. But I think also what it does it highlights something you said early on is you didn't do this on [00:32:00] your own. You reached out right away. As soon as you felt that you needed to take action and weren't sure who, who did you reach out to? You said you reached out to the city, to the county, to the Maine CDC to determine what steps do I need to take, what's out there? Because, again, you're not the expert in epidemiology. You are an expert, Your companies an expert in solid waste removal and recycling. So who's out there to help? And I think that's a good lesson that don't wait. Reach out. Reach out to your state and local governments to see what resources are out there. Don't try to make decisions in a vacuum. Try to get information so that you can put a good plan in place. And it shows in the results that you've had, you've seen some success with your physical distancing program that you've had in place, which is fantastic. Kevin Roche: Yes. Yes, and I really appreciated the resources that took the time. [00:33:00] One that I didn't mention was the Cumberland County Emergency Management Agency. You know, the time that they took with us to put these procedures and policies in place, you know, without their advice, you know, we wouldn't be where we're at today. Peter Koch: Yeah. And you said early on, too, that you were provided with a whole slew of resources. but some of them you had to evaluate each of them. And were you able to implement this particular solution or this particular process in order to make this work? And you had to evaluate it based on your business. But when you found ones that you could implement, you did implement those. And that again, that's a good lesson too when you start to look at it, look at the resources that you have. Evaluate it based on your business and determine which ones will be most effective and which ones will be appropriate for the business that you're in. [00:34:00]Because some would be very effective, but some aren't going to allow you to maintain a certain level of production that you need to, to meet the demand. Kevin Roche: That's correct. And you know, one of the simple things that everybody, you know, I think has been doing is, you know, wiping down surfaces. And we made that a requirement for each and every employee. So, you know, when you touched a doorknob, you know, you needed to wipe it off. You know, before and after for the next person, early on when we were still having some meetings, you know, when you sat down at the conference table, you wipe down the area before and after. Now, we've since then moved off of those meetings, you know, that was when we could still have meetings early on. We've turned to obviously Zoom for just about every meeting that we have now. But you know that buy-in alone, you know, seeing each and every employee, no matter if it was a manager or the general manager, all the way down to every single worker in the organization, having [00:35:00] to pay attention to those surfaces again was, I think, a teaching environment for taking this as seriously as we did. Peter Koch: Yeah, it's great. And it really again, a way to reinforce and help people understand the importance of it so that if someone noticed that a surface or a doorknob or a high touch area wasn't wiped down, that I can imagine in that environment, someone would have said something and someone would have told the person that hey, remember, that's got to get done. And just another way to help reinforce the importance of the process that you have in place. Kevin Roche: That's exactly right. Peter Koch: So let's talk a little bit about how a lot of businesses don't just have an ecosystem where it's just their employees. You have a business that you're going to have contractors come in, you're going to have delivery people come in and your ecosystem that you can typically control with your staff. Now, has people from the outside coming in. How [00:36:00] does your physical distancing policy and all the policies you've put in place for the current situation, how does it affect the contractors that come in and work with Ecomaine? Kevin Roche: Yeah, that's a great point, because what we found was that some contractors were ahead of this and some contractors were way behind. And so, you know, anybody who was working for us, we actually had to go into an outage, our annual outage we evaluated that occurred during the last month and we evaluated whether we could suspend the outage. We could defer some parts of the outage. But by and large, we needed to maintain our equipment if we were going to continue to operate. And that required us to make the necessary repairs and upgrades to our equipment in order to keep our employees safe and continue to operate. So we made the decision. [00:37:00] There were a few things that we could suspend, you know, to the fall or late summer or early fall. But there were some items that we couldn't spend or delay those repairs. And so we had, you know, almost 200 contractors having to come into our facilities and assist us with making these repairs. So, again, we had an orchestrated effort to make sure that our contractors knew what our procedures were in dealing with COVID 19 and making it safe for their workers and our workers and minimizing any opportunity for exposure. And so that worked out fairly well. But follow up was really what was key. And we would have contractors come in and, you know, they'd be kind of coming into the front door here and huddled together and, you know, without any form of PPE or masks and things like that. And, you know, we kind of caught them at the front door and say, Hey, [00:38:00] hey, wait a minute. Didn't you get the memo? And so, you know, before we would even allow them into the facilities, we made sure that they understood the procedures and policies that we had to put into place to deal with these very important measures. And that took some education, no doubt about it. But, you know, I think that because we required it, it wasn't an option and because we had follow through. You know, I had a lot of people focus on safety during this outage. They would make their rounds and really enforce the six foot distancing procedures that were in place and enforce the wipe down of all surfaces that were touched and then enforce the requirement of PPE. But much it was a higher challenge than our own employees because our own employees were you know, it [00:39:00] already had become habit for them. And so we had been doing it for two weeks. So when the contractor started coming in, certainly it was we kind of had to renew our efforts. Peter Koch: Did you have to reinvent or make changes to some of the normal processes during that outage? Like if you had a plan for a lockout tag out or for maintenance of a particular machine where in months past people would work shoulder to shoulder with each other to get this done? Did you have to go through and maybe change some job hazard analysis or procedures to get the maintenance done, to be able to meet the physical distancing policies that you had? Kevin Roche: Yes. And we actually we did that right through. You know, the JSA's in and looking at each job and how to keep each job safe. You know, we orchestrated that effort. And one of the things we did find was, [00:40:00] you know, one of the biggest challenges was communication. So you're trying to fix a piece of equipment. It's a loud environment and you're getting closer and closer in order to communicate and share ideas and share solutions. And normally, you know, you would look at that as, you know, a good thing. You know, a good solution are people are communicating so well. But in this circumstance, it wasn't, you know, really working with the new policies and procedures we put into place. So, you know, for that example, we, you know, encourage our employees, you know, if you need to talk and communicate, leave the area that you're going to have to be so close to communicate and go to an area that you're going to be able to hear each other from a minimum of six feet apart. You know that that's an example of one of the common you know what we talked about those red high exposure [00:41:00] areas that were showing up on the 6 foot close encounter forms that we had to correct. And that worked, you know, that really got people away from the work area that they had to be so close to communicate in and allowed them to have that conversation from six feet apart. Peter Koch: Yeah, it's a great example of giving permission to do something different and still maintain the importance of both the current situation practices and the maintenance that has to be done. Typically, people like you said that it's good. I'm close to the person that I'm working with and we're going to communicate about this and get this done in the most efficient and safe means possible where, you know, the new policy gives them more and implementation of the policy gives them permission to move to a different area. And it's not that they're leaving the job. It's not that they're doing something wrong. They're thinking outside the box. They need to communicate. They can't do it in front of the [00:42:00] machine. They've got to do it in a place where they can hear each other from six feet away. Great thought about that. Again, thinking outside the box. Kevin Roche: And you know that 10 seconds, the advice that we got from Dr. Shah, you know that 10 seconds allowed for people to pass each other in the hallway, stairwell, you know, things like that, you know, going through a doorway. And, you know, his focus was, you know, it's those interactions that have some level of duration. And, you know, he felt like the ten second rule was, you know, going above and beyond where you needed to go, but certainly would provide for a certain level of awareness to reduce those close encounters, if at all possible. Peter Koch: Sure. And still allowing for people to work in the same space with each other. it's a great way to the. Some relevance to it and meaning to it. So a couple of questions as we flesh this out here. I'm going to throw this one out yet. [00:43:00] I'm not sure I talked to you about this before, but what do you wish that you had known before the decision to implement physical distancing that you know, now,. Kevin Roche: You know, that physical distancing was a tool that worked? We did physical distancing early on. But even, you know, even myself, even when I created the policy and the requirement, you know, I wasn't certain that physical distancing would make a huge difference. I was just listening to the health experts. And because I didn't know, I had to, I had to take her advice. And, you know, I wish I had known or better understood that from day one, because then, you know, I could have started this even sooner than we did. And I could have been, I guess, had more conviction and understanding of how well social distancing or physical distancing [00:44:00] actually will work. Peter Koch: Yeah, that's a great point. Kevin Roche: And now we're a month into this and we're all you know, everybody's saying the same thing. Is that physical distancing, you know, has worked and has limited, you know, exposure to the limits that we're seeing today? Peter Koch: Sure, sure. And you talked about this a little earlier as well. And this is in reference back to the encounter checklist that you've had there and the encounter documentation when that was going on, that was the main way that you were documenting and holding people accountable for the encounters that they were having. How were you able to determine that your program was being successful in the middle of it using that checklist? Kevin Roche: Well, you know, that's a good question, because we didn't have a track record and we were just beginning this. And, you know, I did get some pushback early on. You know, I'd get, you know, one of the things people would [00:45:00] say is, well, you know, this six foot thing, you know, this is being transmitted because people touching surfaces. This is being transmitted, You know, if I just go into somebody else's space five or 10 minutes later. But what the health experts were telling us was that the primary way of transmission. Yes. It can be transmitted a whole host of different ways. But the primary way was the person to person, you know, durations of close contact within six feet. And that was what we needed to focus on first and foremost, you know, getting people home. I guess this is the first thing. You know, keeping them at home, those that could be at home. But then, you know, for those people who had to be at work, you know, really limiting that and wiping down the surfaces, too. But no, there's no way that we can ensure that we're wiping down every single surface between every single touch. But that was not ever communicated [00:46:00] as the primary way that the coronavirus was being transmitted. And so the really, you know, we were focused on the best, the best return or the best value for, you know, the efforts that we were making. And that was that 6-foot social distancing or physical distancing that we employed as being the number one way that we could move forward. And so, you know, I found that, you know, we had to hear what the health experts were telling us. And we had to give it a try. And that did take some convincing early on. But, you know, I feel like now that we're a month into it, I no longer have to be the one who convinces people. I think it's you know, the track record has convinced each and everyone who works here. Peter Koch: Yeah. And retrospectively looking at where you are now, the lagging indicator of a healthy workforce shows that the social distancing or the physical [00:47:00] distancing and the tracking has worked. And I think in the middle of it, as I think about another way that tracking tool can help the company overall is when you reach out to the experts, they tell you that this is the cause. And here is a way for you to prevent this from happening. You put that in place when you start looking at how the encounters start overall, start to get reduced. So I imagine right at the beginning, like you had said, you had quite a few of those encounters. And then as you start to look at the numbers, the number of red encounters, a number of yellow encounters started to decrease over time. And so you probably have the majority of them are green and some of them might still be yellow. And you're looking into those two to make changes. But. That's a great tool, data is an awesome tool to be able to look at as long as you've identified the problem and you're [00:48:00] implementing a solution to see in the moment whether or not you're making some progress because it can be pretty scary, especially when you don't really know what is going to happen looking back. We know what has happened, but looking forward, we're not really sure. So in the moment, using that data to show that you can be successful helps not only you as the CEO, but your executive team, the managers of the different departments and the supervisors and then the staff themselves to show that, hey, we are making a difference here. Right. We are truly making a difference. So the importance of that tracking tool I don't think you can speak to that enough in this whole process. Kevin Roche: That's exactly right. And when we had had some illness issues, we had been able to go right back to the data, the actual data point, instead of relying on somebody's memory and who they have been exposed to over the last [00:49:00] two weeks. We can go back to the data and we can show, OK, these people, these two people were exposed to one another. They were exposed for 10 seconds or 30 seconds or no they were exposed for an hour. And then you can react to that with a good understanding of what the exposure actually was. Instead of trying to guess what happened two weeks ago. Peter Koch: Sure. And I think that will probably provide some comfort to the individuals, not only at work, but even you at home when I go home. Hey, you know what? We know we had an illness here. But I can track I can go back and show that I was not I didn't have any contact with this particular individual. I can even go back two weeks and prove that I didn't have any contact with this individual or if I did, it was only for a few seconds and we should be good. So that's a it's a great [00:50:00] tool. The data can certainly help you guide the solution, come up with different processes and take some comfort that the solutions actually working. So awesome. Great with that. Kevin Roche: Yeah. And I did get a call when we did have a positive test from the CDC when they were doing their investigation. You know, I kind of told them what measures we had in place. And, you know, their response was, well, awesome. You know, it appears that, you know, you've got this well managed and under control and you can determine who needs to quarantine and who doesn't. Peter Koch: That's great. That's really another affirmation that the process is working. Now, going back, I know we talked about this already, so thinking about the contractor piece because again, that's an important part. Did you did you approach the contractors ahead of time and kind of give them a written copy of the policy as well as approach them when they came [00:51:00] to the facility to start work? You did both of those things, correct? To help them understand what process they would have to have in place. Kevin Roche: We did. And, you know, we did verbally and in writing and sometimes more than, you know, once or twice to ensure that they were coming into an environment that, you know, was treating this crisis very seriously. But even with that, again, you know, as I mentioned before, you know, the seriousness of the of the actions that we were taking, I think, you know, sometimes, you know, maybe it didn't get down to the front line, maybe it did get to the frontline. But they weren't really in habit mode yet. And so, you know, we actually, I got some positive feedback from some of our contractors, you know, who kind of came to our facility and we're like, whoa, you know, you guys are really taking this seriously, aren't you? And so they had to kind of rethink the [00:52:00] way that they were operating. And so it really took, you know, a lot of emphasis when it came to contractors because they were coming at us at different levels of understanding and different levels of how serious they were taking these measures. But once, you know, once they were here, they really had, you know, no excuse. As far as not understanding the procedures and policies that we had set in place. And, you know, if they weren't willing to follow them, then they were asked to leave. Peter Koch: That's a that's a really great point, because I can imagine that could really undermine all the efforts that you've put in place if you're allowing contractors to come in and not follow the same rules as your employees do. And the stakes are pretty high with this one all that work that you. Put in for the weeks prior to build those habits, to get buy-in, to get people to understand that they're all in this together, [00:53:00] to try to make this company successful and to stay healthy. That a contractor coming in and undo it and not following those procedures can have a significantly negative effect on the attitudes and the effect of your program. So that's a great point that you made there, Kevin. Kevin Roche: And we did have an experience where a contractor who came in to do their work, you know, a week later, then notified us that he was tested positive. And then we had to go back through those close contact forms to find out who was exposed. So those close contact forms are not just utilized for employees, fellow employees, co-workers. They were also utilized for contractors. So if you did come in to close contact with and or have a close encounter with a contractor, you were required to document that as well. Peter Koch: And [00:54:00] those were reviewed again at the supervisor level, at the manager level, if it could have been fixed. And then again, at your level, the executive team level, to make sure that solutions were put in place if it kept happening. Kevin Roche: That's correct. Peter Koch: Right on. Great. Well, we're coming right to the end of the podcast here today, and before we go, is there anything that I should have asked you about this? But I didn't. Is there anything else that you want to add to our conversation today? Kevin Roche: You know, I think you covered just about all of it. The only thing that I would emphasize is the importance of the buy-in, the importance of leadership in this. And that's not just leadership from the Top Gun, whether it's the CEO or the general manager or the executive director. It has to be leadership from everybody on the team. Everybody in your employment, because everybody can take a leadership role when it comes to [00:55:00] keeping every single employee safe, including the front line. So the front line can be leaders in this in protecting their co-workers and protecting the contractors, really protecting everyone and how to stay safe and when they're faced with these circumstances, such as we've been faced with over the last month. Peter Koch: That's a really interesting thought there. And as you were talking, what I thought of is you could really put any situation into that. It doesn't have to be response to a pandemic or coronavirus, but it could be lockout tag out. It could be machine guarding, it could be slips and falls. It could be another potential hazard that's there and leadership at all levels. Right. You said from the top all the way down to the line staff person, there has to be buy-in, there has to be leadership in order for those to be effective. And it's something that lacks in a lot of things. And [00:56:00] the items that you talked about today in order to make the solution for physical distancing really work. It's not just the paper that you have in place, but it is actually the leadership and the accountability. And you said it more than once. You can't let your guard down. So if you want to have a good response to a pandemic like this or you want to have a good response to a change in your lock out tag out program or another program that you have for employee safety, those are concepts that can be brought to any of those things. And they're really critical concepts that have to be implemented to be a successful company. And I appreciate you bringing that up because it really ties this all together. So. Thanks. Thanks very much for. For throwing that out there, because it's not only a great lesson, but it's a great example. So thank you for that. Kevin Roche: Certainly. Peter Koch: All right. Well, I think that about wraps up this safety experts podcast. I really [00:57:00] want to thank you for sharing your expertise with us, Kevin. Thanks very much. Kevin Roche: Thanks, Peter. And look forward to joining you next time when you we're on the other side of the circumstances that we're faced with today. Peter Koch: Yeah, me too. Hopefully we can have you back on and we can talk about something else a little lighter than the response to the pandemic. So, yeah, I'm looking forward to that as well. Kevin Roche: OK. Peter Koch: Excellent. Kevin Roche: Thank you. Peter Koch: Today we've been speaking about implementing a physical distancing in the workplace with Kevin Roche, CEO of Ecomaine , on the MEMIC Safety Experts Podcast. If you have any questions for Kevin or like to hear more about a particular topic on our podcast. Email me at [email protected]. Also, check out our show notes at MEMIC.com/podcast where you can find our entire podcast archive as well as a link to our pandemic planning a resource page with workplace safety tools for keeping workers safe and healthy. While you're there, sign up for our safety net blog so you never miss any [00:58:00] of our articles in safety news updates. And if you haven't done so already, I'd appreciate it if you took a minute or two to review us on Stitcher, I-Tunes, or whichever podcast service you found us on. And if you've already done that. Thank you. Because it really helps us spread the word. Please consider sharing the show with a business associate friend or family member who you think will get something out of it. And as always, thank you for the continued support. And until next time, this is Peter Kotch reminding you that listening to the MEMIC Safety Experts Podcast is good, but using what you learned here is even better.