SMART Goals with Randy Klatt
MEMIC Safety Experts - Podcast készítő Peter Koch - Hétfők
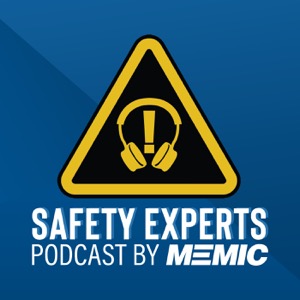
Kategóriák:
When a workplace injury happens, it is an indication that something within the organization didn’t function the way it was supposed to. If your organizational goals are set up well, then you can readily identify where the failure was and address it. Specific, Measurable, Agreed On, Realistic, Time Based - SMART goals are one way to help you and your organization develop a road map for safety success. On this Episode of the MEMIC Safety Experts Podcast, I talk with Randy Klatt, CSP, Director for Region 2 Loss Control at MEMIC, to better understand how SMART goals can help you stay on the path for safety success. Peter Koch: Hello, listeners, welcome to MEMIC Safety Experts podcast. Today, we're recording from the studios of Portland Pod. If a full service podcast, recording and production studio right here in South Portland, Maine. And if this podcast sounds good to you. Get a hold of Tanner. Down at PortlandPod.com. My name is Peter Kotch and I'm the host of the MEMIC Safety Experts podcast. I've worked for a number of different organizations and small businesses over the years. And if I've asked the person in charge of safety was important to them and their organization, the answer that they had was always yes. And I was considering that the other day, preparing for this podcast. And I took that question one step further. So what did I understand the safety goal for those companies I worked for, to be? The answer for many, was some form of. Well, nobody gets hurt or everyone goes home at the end of the day. Those really, truly aren't lofty goals, but under more scrutiny. None of those organizations consistently achieve them. Don't get me wrong. These were great companies to work for [00:01:00] and successful in many, many ways. And they consistently achieve the goals that they set. However, that safety goal remained elusive for most of them. Looking back, I realized that even in companies that had safety as a goal or priority, I, along with my co-workers, made choices or engaged in tasks that could have, should have and sometimes did put me in situations where I might have been and sometimes was injured. And in speaking to others, I found that there were similar experiences and responses. Yes, the company I worked for has a safety goal. They don't want me to get hurt. No, I don't always work safely, though. And if they took the question even further and explored what backed up the safety goal, I found that in many cases there was no organized plan or they use their insurance loss run to track progress or the goal was just way too general. Sometimes it was a fairly specific goal and everybody was responsible for it. So [00:02:00] effectively, if everyone's responsible, then no one's responsible. And in one organization, the goal was very specific. But it was never achieved. And the same goal was set year after year after year with we need to do a better job working safely. As the sendoff. So I don't think that my experiences is really unique. So I want to get all you listeners to take a challenge right now. Do you know what the safety goal is at the business or organization that you work for? Don't take too long. They should come to mind fairly quickly. Now, think about the following questions. With that safety goal that you have in mind, how are they measured and when does it get reviewed? Is there a timeframe for that goal? Is the goal, General, or does it target something specific? Who is responsible for that goal? Has your company ever even achieved that goal? You might be surprised, as I was, that the answers to those questions weren't as easy to find as you [00:03:00] thought. So why does it matter? Why can't the goal be that everybody goes home at the end of the day and then leave it at that? Well, it's fine if everyone does that all the time, without exception. But I don't know many organizations that don't have at least one workplace injury a year and often more than one when an injury happens. It's an indication that something within the organization didn't function the way it was supposed to. And if the goals are set up, well, then you can more easily identify what went wrong and address it. If not, then you're in the Spray and Pray School of Workplace Safety, and that's not a functional place to be Today, I'm speaking with Randy Klatt, CSP and director of Region two Lost Control at MEMIC. To better understand how smart goals can help you stay on the path for safety success. Randy's career spans emergency medicine and active duty Navy pilot, commercial airline pilot and aviation safety instructor at the university level. Randy [00:04:00] is the current director of Region two loss control at MEMIC, leading a team of consultants serving the central Maine and southern Maine areas. Randy, welcome to the podcast. Randy Klatt: Thank you, Peter. It's great to be here. Peter Koch: Awesome. Great to have you in the studio today, Randy. So let's jump right into it. You've had quite a bit of experience in large organizations where goal setting was an integral part of work life. So I guess the question to you to start things off is why set goals at all? Randy Klatt: So as a roadmap, as a method of reaching the end, whatever that end might be, we better have some goals along the way so that we know where we're going. We have people who understand what the responsibilities are going to be, how do we measure when we're there, all those sorts of things. So I just look at it as someone sent on a long trip with no compass. How do you figure out where you're going if you don't set it, especially with workplace safety? Because it is an elusive target. [00:05:00] It's a moving target and it takes a lot of work to get there. So if you're not organized and have a strategy and understand if you're failing or if you're winning, it's pretty hard to make any meaningful changes. Peter Koch: So let's talk specifically about safety goals, because in many organizations, the goal of safety is really no one gets hurt but to have a good goal and safety if we have a functional goal and safety. How can that really positively impact the organization overall? So what's the positive impact of a good, solid safety goal? Randy Klatt: Well, again, if you if you set a goal and you achieve it now, you know that you've made progress. And in the world of safety, of course, that goal is to prevent workplace injury. I understand when people say my goal is to have no one hurt. Safety is number one. You know, all those things are said. And I think they are genuinely. They come from the heart. People do believe that that's what they want. They don't want people hurt. But the real benefit [00:06:00] comes when you have a structure around that desire. We all want a lot of things in your personal life as well as your business life. And you know, you will not achieve them unless you have a goal set to do so. And then a structure around that to make it happen. And there's a lot of study out there about the human brain and what goals do for us, what it actually does to motivate behavior. And so back to your question about what does that do for an organization? Well, it actually helps you achieve that goal of getting no one hurt. Now, it may not be possible based on the size of a company and how much exposure you have to go from 100 injuries in one year down to zero the next. That's probably not going to happen. But a progressive improving program that is measurable and that is agreed upon by everybody in the strategy has been put [00:07:00] in place to achieve it. Certainly we pick away at those incidents as they occur and we learn from them and we set new goals. And eventually you find yourself in a place where a son of a gun. We actually did reduce injuries considerably and we've met our goal for the year. Now, we probably need another goal for next year and we'll continue that process, continual improvement is what it's all about. That's the way safety is. It never really ends. You know, as we know, safety never takes a holiday. So you have to continually work on it to make it better and better and better. And of course, the benefits, we could talk about that for a whole podcast. But the cost involved in human suffering and the way people feel when they're injured in the way it inhibits their lifestyle, it's just there are numerous benefits to having a safe and healthful workplace. Peter Koch: Sure. So let's take that concept a little further and talk about how there's obvious benefits if I can achieve the goal [00:08:00] of fewer injuries there. There is a cost benefit. There is a culture benefit. There's an employee health benefit that is overall healthy for the company. But there is also a consistency in habit establishment there. If you are able to set a goal and you're able to go back to it all the time and consider what makes the goal achievable, what you have to do to do that, if you're doing that consistently, it builds those habits. So if you go from a culture that has, take your example, 100 injuries a year and you want to bring it down to half of that in the first year or a quarter of that in the first year, you want to go to 50 injuries or 25 injuries. You got to change something. And in order to make those changes, you've got to identify what the change and then you have to consistently do those things. So if you do it over a year and you keep going back to that, you could pretty much establish some fairly good safety based habits, which, [00:09:00] again, you know, what gets expected is inspected. So if we do those things, we will achieve the goals, hopefully. Randy Klatt: Right. And I think all of that you just said can be summed up in the word culture. You use that a few times. It is the culture of my organization that we shall not have injuries. And I'm going to do everything as the company owner or the CEO or the general manager to make sure that happens. But simply saying that to people. Doesn't really make it work. So hanging up the banner in the facility that says safety is number one. Doesn't make safety happen. What makes it happen is the culture of the organization that supports that message or that goal at all levels. Not only supporting it, but actively doing something about it. As you said. If we don't change anything, nothing's going to change. There [00:10:00] are a lot of companies out there that have great safety records for a period of time. But when we really drill into it, they just got lucky because eventually that comes back to bite them. And they have a really poor year or several poor years or a catastrophic incident. There are other companies that aren't performing very well from a safety perspective, but have huge programs in place. But it's mostly compliance and it's fill in the blank. And it's lip service. And when we really get down to what's happening, the floor level, it isn't really significant for safety improvement. So that's why these goals have to be not only lofty and on the executive level. This year, we're going to reduce injuries by whatever. But they have to work their way all the way down to the newest new hire in orientation to talk about safety. And this is our goal for our company and this is the goal for [00:11:00] your department. You're going to and this is what your supervisor will expect you to do for your safety each day. And this is what we're going to do at every level through the organization. And it's all going to be measurable and it's going to be assigned to people and they're going to be held responsible for it. And when all that happens at all levels, son of a gun. Now we do make change and injuries, like all other aspects of a business, turn out to be manageable for the vast majority of them. Peter Koch: That's a great point. Being able to establish behaviors and habits by looking at the corporate goal and then breaking it down so that corporate goal makes sense to each part of the organization, no matter how high up in the seats we are, how low on the totem pole that new hire might be so that they all understand what their responsibility is as [00:12:00] part of the success of that goal. Randy Klatt: Oh, that's clear. And we see it as safety consultants. We see it almost every day. We go into businesses and you sit down with the owner and he thinks safety is great or you meet with the safety committee and they're all eating their doughnuts and very happy and safety is doing well. But when I walked into that safety committee meeting, I walked by three hazards that were obvious in the hallway or, you know, the fire extinguishers are never inspected. The emergency exit was blocked. There's electrical cord that's damaged. There's material that people are trying to lift by hand when there's a hand truck or a forklift or a pallet jack to use. Everyone's in a hurry. They're rushing around. And if they're not being hurt, they're just lucky at that point. It's inevitable it's going to happen. So everything has to translate down to the daily activity. And again, a culture will support that. But if you want to look for a structure to put around that, something that will help everybody [00:13:00] understand how to set those goals, then we need some kind of template. And I think that. The smart goal template, which we are about to talk about here, is the way to go because or at least a way to go. I won't pretend to be the expert on all goals or all a psychology or even all safety. But I found these to be very helpful and make it easier for people to set goals that are actually going to be attained. Again, the owner will say there's not going to be any injuries. That's my goal. And I applaud that. And I say, yep, that's the way it should be. But that's not the way it's been for the last 20 years. Somebody got hurt every year. So you're, as you said earlier, you not reaching that. So what are we going to do to actually reach that goal? And that's when we can talk about S.M.A.R.T. That acronym. To help people understand it. There is some criticism out there like there is on [00:14:00] most things that I guess our goals are outdated or it's not what it's cracked up to be. It's not the magic bullet. Well, you're right. Absolutely it isn't, because it's not the acronym that's going to make things change. It's the people who understand what it means and how to use it and actually formulate proper goals and processes to make those happen. That's what's going to make the difference. So it's a tool like any other tool in the safety toolbox that I think will help people but it in of itself. Doesn't do anything. Peter Koch: No, you've got to take action in order for something to happen. It's not it's not the Alexa thing. Hey, Alexa, make me a goal. Randy Klatt: Yeah, it's not a smart speaker. Peter Koch: Thank gosh. It's done great. We can move on with our lives now. Someone else would take care of it. No, if you have the goal when you're speaking there, I was thinking that goals give you a reason for change. Like, if you don't have that goal, then there's no reason to change the behavior or the habit or the culture that might be causing [00:15:00] the circumstances for the injury to happen. So like you’re talking about, you go to talk to the safety committee and they're excited about what's happening there. They're the safety committee. We've just done this. But you've walked through and I've had that same experience walking through with the safety committee and in the stairway that's narrow enough to begin with. They have boxes stored on it, a propane tank stored on it and other equipment stored on it so that there's no way to actually get out of the office that's upstairs without going through all this stuff. There's got to be a reason to make that change. And if the goal is set appropriately, the goal then gives you a reason to change the behavior, to not walk past that, to understand that I can now take action and not that I can just take action, but I must take action because that's our goal. So it is a call to action if they're set correctly. Randy Klatt: Yup well said. And I [00:16:00] think this format can be used at any point in an organization's development. It can be used by any individual. And we can talk about long term goals, short term goals, business goals, personal goals. You want to lose weight this year. You want to lose ten pounds. Okay, there's a goal. What are you going to do to achieve it? Well, I'm going to hope I lose 10 pounds. Peter Koch: That's my goal. Yeah. Yeah. I hope. Randy Klatt: It doesn't work. Well, it may. It probably won't. And it won't last unless you actually have an action plan to put in place. You have something that is specific. Let's just say it's specific, measurable, attainable, realistic and timely. Peter Koch: There you go. Oh, here we go. Randy Klatt: Yeah. And there's your smart acronym. Peter Koch: So before we jump into that, can you talk a little bit about the pitfalls that companies will stumble into when they're setting goals that make those goals unachievable or [00:17:00] they make those goals so complex that they can't? So what are some of the pitfalls that you see companies falling into when they're setting goals? Randy Klatt: Two or three things come to mind right away. One is that the goal is too lofty a goal or too general a goal. Again, the top guy, nobody gets hurt. Now, you all carry that plan out for the year. It's not realistic for most cases. So the goal has to be realistic enough that it can actually be achieved. So we try to, we set people up to fail. If we do not set a goal, that is actually something that has a good chance of succeeding. The second problem is, even if it's a realistic goal, I often see that it doesn't translate to the lower levels of the organization or through all levels of the organization. It is a goal and it's been set by the safety committee or it's been set by management [00:18:00] or the general manager or the owner. But it doesn't get to the floor level. It doesn't get to the new hires. They don't understand it. I'm continually amazed when I do training with companies and I have a group in a room and I say, what's your safety goal for the year? Usually I get the deer in the headlights look. And then somebody says, well, nobody gets hurt. And we have that whole discussion about specific goals. But if I go ask someone on the floor or in a production area or on the job site or in the back office, what the safety goal is for the company. They don't even know if there is one. They've never even considered it. So your administrative support person in, say, a manufacturing company. It's just as important for that person to understand the goals, be in on that planning. Be part of the solution. And help the company to reach their goal [00:19:00] as it is for anyone on the floor. Because how many times have you seen the largest claim, the worst injury in a business is administrative support person with carpal tunnel syndrome or the back injury that occurred when they slipped in the parking lot on the way in, when they deal with hazardous materials and heavy machinery and all that all day long and no one is hurt there but someone else is with some mundane task of walking through the hallway that happened to be wet and they slipped and fell. So these goals have to be. Disseminated through the whole organization, and everybody has to be part of it. So clearly set a realistic goal. Advertise it. Publicize it. Make sure everybody understands it. And then put a structure in place where everyone is involved and everyone understands it. Every person in the building should be able to answer the question. What's your safety goal? You know either for the year or the day or the week or whatever you're asking them about. [00:20:00] If they just look at you like, well, I don't know. Or you can say what's who's on your safety committee? Who's your representative? And if they say, I didn't know we have a safety committee, well, there's your problem. So those lofty goals that have been set by the committee that they're all excited about have not made their way into where it really needs to go, where people will actually change or modify or train or replace equipment or inspect or hold people accountable for any and all of those things to actually make things change and to be safer. So set good goals and communicate it and have a structure in place to make it happen. Peter Koch: Perfect. So a good guide, one guide, because as we establish before, it's not, this is not the only road map to setting goals, but it is a pretty decent road map to setting goals and gives you almost a step by step way to outline [00:21:00] a goal that should function well for your company. And that's the S.M.A.R.T Acronym. So we talked about it before. Specific, measurable, assignable, realistic, time based. And we can get in the E.R part later on, but evaluated and reviewed. So let's break that right down and talk about each of those bits and pieces separately. So let's start with specific. What does it mean to set a specific goal? Randy Klatt: Just as it says, we have to be specific enough so that we can then understand what actions have to be taken to reach it. If it's too broad a goal to overarching. People aren't going to really know where to start with it. And we might not be sure that we've met it because it's too nebulous. So let's get a very specific goal. And when we talk about this S.M.A.R.T Acronym, you ask me about specific, we'll talk about the rest here as we go. But some of those letters can change. It depends on which version [00:22:00] you read. It can be updated. Typically, I don't think I've ever seen anything other than specific for the S and measurable for the M. Those are pretty universal and the T is always time associated in some way. It's either timely. Time related. Time framed. Something like that. The A and the R. Those can be a little bit different, depending on which version you read or which one would work best for you. I've seen Assignable, which I really like. That's the original from back in 1981 when this was first published. So assignable is good because that means it's someone is going to be held accountable for that goal, but it can also mean agreed upon. I've seen attainable, used very much like realistic could be relevant. I've seen a few other words for that letter as well. So sorry I got off track a little bit on you there. But in the end, it doesn't matter as much. Which one you use [00:23:00] as long as you use one. And it makes sense to you. And you don't leave one of those off if you leave off time framed or timely. Now, we don't really know when that ends. It's a continual process, and I know it is. But we have to know if we've made it at some point, probably end it and start over. But you can't leave it off if you leave off assignable or it's not realistic. Well, obviously, things aren't going to happen. Peter Koch: Yeah, it makes it harder. So if we if we roll back to specific and we talk about a phrase that we've used a number of times, like no one gets hurt or everyone goes home at the end of the day in one piece. That's kind of specific. Like no one gets hurt. So nobody here gets hurt. So, OK, but like you said, that's a fairly lofty goal, depending on what industry you're going to be in. Is it actually realistic to do that? And is it truly specific enough like that might be the objective for the organization to have zero injuries, but [00:24:00] a goal that supports that objective might have to be more specific. You might need to look at where your injury trends are. So I go back historically and look at my lagging indicators. And while these are the areas where most of the injuries are coming from, so maybe I need to set some goals in those areas to be more specific about what might be causing those injuries or what the challenges are. So once we find that specific topic, that area that we want to improve on, let's then talk about measurable. So measurable is another one of those pitfalls that we might think we know how to measure, but we might not have a mechanism in place. Who can you speak a little bit about what different ways there are to measure goals? Randy Klatt: Sure. Well, we're talking about workplace injuries here, of course. So I would stick to that area. So are we going to talk about OSHA recordable injuries, lost work time injuries, anything that requires a worker's comp claims, or are you going to talk claims in general? Or [00:25:00] we can talk incidents which are, of course, really important to identify. Go back to Heinrich's pyramid and find a three hundred incidents out there for every few injuries and one serious injury. So it depends on where you're forming these goals and what your area is. But at some point it has to be safety related and measurable. Now, that's when we're talking specifically about injuries. So let's take an example of a company that forms a goal of reducing OSHA recordable injuries by 10 percent for the next calendar year. So we've fulfilled the smart goal, assuming that we have assigned this to people to carry out. We've fit in the blocks. But as we mentioned earlier, simply forming that goal doesn't make it happen. So now what are we going to do? Well, now we have to set another goal and probably a whole bunch [00:26:00] of goals to follow this on in shorter timeframes and smaller overall view points. So let's go to each department and form goals that will support this. Let's form quarterly goals that will support this. Let's go to each supervisor and talk about site inspections. And you have to do one of those every week. OK. We can form a smart goal around that activity. Make sure that happens and then that will support the overall goal. So when we started with a smart goal that talked about reducing injuries, what we end up with is multiple goals that don't say anything about injury but are preventing injury. Their goals related. They're actually activities that are proactive. There are things that we are going to do to prevent the injury. So our overall smart goal is about measuring how many people were hurt. But to support that, we better come up with a whole lot of goals. That [00:27:00] are all about activities designed to prevent those injuries. Peter Koch: And that's a pretty interesting point because the initial goal uses a lagging indicator as a measuring tool. So you're going to go back to that the OSHA log to determine whether or not you had 10 percent less injuries last year over this year, which assumes that you're actually recording. Of course, the injuries on the OSHA log, which is goes back to that measurable discussion. So what mechanisms do we have to actually measure the injuries that come in which might actually look into a different corner of your business? Do we have a mechanism to report injuries? Then do we have a mechanism to track those injuries, not just have them on the show log, but how are we actually looking at those? So the discussion about the S.M.A.R.T goal can take apart or unravel parts of your business to look a little [00:28:00] bit deeper, to see if you actually have mechanisms to manage the goal that you have. And then the beautiful part about what you said is, if done right and the overall goal of reducing injuries for your company gets pushed down to the different levels and departments within the company. Then we start measuring the leading indicators. Are you doing training in those areas where you might find those injuries? Is there injury reporting training going on even at that, the basic level? And is there technical training being done to help support engaging in the risk, the risky behaviors or the risky tasks that the individuals might have to deal with? Or even the non risky ones like you talked about before, parking lot, someone slipping and fall in the parking lot or the administrator who spends all day at their desk getting carpal tunnel. They're not engaging in the hazardous activities that their co-workers are on the factory [00:29:00] floor. But if they're needing to meet the goal, they have to make some change there as well. So there needs to be some leading indicators that can get measured for them. That's a that's a really great they really great thing about the S.M.A.R.T goals is it allows you to look more deeply within your organization to see what you're doing, measure what you're doing, and then look to see if you've actually achieved that. Randy Klatt: Correct. And if you're using the A as assignable, then you have held someone accountable for that goal. So often we see a failure in safety because basically no one is held accountable for it. The owner says there'll be no injuries everybody says Yep. Good idea. We all agree. Let's go do our work. Someone gets hurt and they go, oh, gosh, that's too bad. I'm sorry that happened. No one is held accountable for that injury. And again, I'm not looking for blame. That's not what it's about. It's causal factors. And these things happen for a reason. We [00:30:00] investigate. We find out the reasons. And that has to be. Ninety nine percent of time. It's a human failure of some kind. It's a failure of supervision. It's a failure of training it's a failure of equipment. It's something that should have been fixed, should have been assignable to someone. And then you hold people accountable for that so it won't happen again. So if my evaluation has things on it like productivity and sales and widgets going out the door and customer service and, you know, I'm a great guy to work with and yep, that's teamwork is wonderful. Those are all things that typically people are rated on. But you also have a safety piece of that in there that you were assigned these goals. And we use this format and you know about it. And you didn't do it or you did. Congratulations. Thank you. We did have a great safety year. So it helps to keep everybody. Focused on the goal? Peter Koch: Yeah, I think you're right. And then the [00:31:00] the individual or departments or a group of people who are assigned responsibility for that particular goal. Then when they know they're responsible, they can take responsibility for it. It's like the cord that's laying across the walkway. It's not my cord. It's not your cord. And I don't know whose cord it is, but everybody's walking across it. And I'm not responsible for picking it up until somebody falls across it and falls down and breaks something. Now, everybody's responsible for it because we didn't achieve the goal. But if someone was responsible to make sure the walkways were clear, now we can look to see were we successful. And can we celebrate or do we need to do some remedial training if we weren't successful? So that accountability or assign ability is a key part. Along with realistic, too. If I'm assigned a goal or a team is assigned a goal or a responsibility for it and it's not realistic, that has a really degrading quality to the [00:32:00] morale. As you look forward, if I'm assigned a goal that's not achievable, not realistic, then it doesn't help the safety situation or the safety culture whatsoever. Randy Klatt: It does not. And in fact, when I see that a common way that I see that is when there is actually a safety director or a safety coordinator, you know, someone's been assigned in the company, which, you know, generally speaking is a good step to take. Someone should lead that program. But the problem then becomes everybody's is, oh, well, that job is the safety director's job. And when things go badly, he or she is the one that gets the blame for it. When, in fact, in reference to everything else we've talked about today, it's an organizational effort. There are S.M.A.R.T goals that should be formed for every one that safety director cannot be will not be in all places at all times watching. All people cannot realistically be held accountable for everything that happens. Now, [00:33:00] it is very specifically in their job description, I'm sure, and in their evaluation, because they're a safety person and that should be that way. But in order to attain company wide or organization wide goals, they need help and they need everyone's help to do that. So the owner will come down hard on the safety director because they've got way too many injuries when in fact, I can look back to the owner and say, wait a minute, where were you last week? When was the last time you walked through the facility and noted the issues? Have you ever stood on the top rung of the ladder as a foreman when you knew you shouldn't you have responsibility in this program? So those are the things that would really help to have this format in place, keep everybody on the same page, support that safety director. And when things go well, everybody can take credit for it because it is a team sport. Peter Koch: Let's [00:34:00] pause for a moment and take a quick break. The MEMIC Safety Experts podcast is dedicated to discussing, describing and even debating workplace safety across all industries and applications with industry leaders, top executives and safety experts at MEMIC. Today, we've been speaking with Randy Klatt, director of Region two loss control at MEMIC, about S.M.A.R.T goals and how they can be used to help create a path to better safety performance. However, this S.M.A.R.T goal concept is only part of the roadmap to a successful safety culture. Do you lead people in your company, in your department, or maybe even in your work group? Then you'll want to check out our first episode with Randy Safety Leadership Walking the walk to find out more about how leaders can be successful and create a balance between safety, quality and productivity. You can find Randy's episode and more at MEMIC.com/podcast or check [00:35:00] us out on your favorite podcast platform and then subscribe since we drop new episodes every two weeks. You won't be inundated with notifications, but you'll never miss a new episode. Now let's get back to today's episode. Peter Koch: So to support that team, like with anything else, it needs to be or the goal needs to be refreshed in people's minds time after time after time. You think about any other goal that gets set in a company, whether it's a financial goal, a productivity goal, quality goal. You talk about those things sometimes daily, many times weekly, definitely quarterly and always annually. But from a safety standpoint, if you only look at that goal once a year, that might not be. That might not be appropriate for you. You might need to put it in front of you more frequently. So that time based [00:36:00] part of the Smart Goal acronym is a pretty key part. And not just to say, yep, we're going to look at it annually or it's going to be within this year. That's fine. But then when are you going to go back to it? How are you going to measure it so that we know where we are and can forecast where we're going before we actually get there? Because then you can make relevant change in stride instead of having to wait to the end of the year using the measurements of our lagging indicator and go, oh, we didn't make it. We got to be safer next year. So everybody be more careful. Thank you very much. Randy Klatt: Yeah, that that and that's exactly what we see most of the time. Even if a company has a goal for the year, which I think you have to set, I think that's important. Before you know it, 11 and a half months have gone by. And we look back at the goal and we say, oh, we didn't make it ah well it's because you didn't do anything differently. You didn't do anything to support that [00:37:00] overall overarching goal. That was a year long, even using the S.M.A.R.T format. You're never going to reach that goal simply by setting that goal. It has to be supported by multiple other goals with shorter terms. So, yes, let's review that overall goal every quarter or every month and then let's support that further by having the safety committee meet every month or having a team meet. Let's support their efforts by doing weekly facility inspections. Let's support it by doing tailgate talks or tool box talks every week on Monday mornings. Let's support it by doing quarterly all hands meetings, let's et cetera, et cetera, et cetera. So. The timeframe is important. All those things I just measured mentioned are measurable. If I do it at once a week, we should have 52 of [00:38:00] them. All right. Let's do a couple of vacation this take a few holidays. All right. Let's we're going to do forty five of them this year. There's your assignment. So now there's there are people that have very specific, measurable, attainable, assignable, realistic, timely goal. Just one. That fits the format, that will help support the overall goal of injury reduction. That goal in and of itself still isn't enough. That's one person doing some training once a week. We have to do some other things, too. So every company is different. But I do know the universal truth is that if you have injuries and you don't change something, you'll continue to have injuries. So let's get this S.M.A.R.T goal format and in big into the company and make it a part of our DNA. And you can use this on a daily basis. I always ask people how much of your to do list. Did you get done today? Peter Koch: Oh, [00:39:00] I got it all done. Randy Klatt: Yeah, sure. Peter Koch: Because I only set one thing. Randy Klatt: Yeah, well, at least it was realistic. Peter Koch: It was it was very realistic. Randy Klatt: But that's the point, of course, that, you know, S.M.A.R.T goals are not just that overall annual goal for safety. And these other things that we've talked about, but it can be used on a daily basis. I have a to do list. Am I going to get that to do list done today? Probably not. And that leads to frustration. It's we are in a society where we're trying to do more with less quite often. So you're never going to get it all done. So let's take the bites out of it that we can actually chew and let's break it down. Use the S.M.A.R.T goal format. So today I'm going to be very specific. I can do these three things and the measurable part is today if it's done or not. I'm assigning it to myself. I'll make it realistic. I could do only those things. And of course, time is today. So boom there is a S.M.A.R.T goal. I've taken my long to do list [00:40:00] and made it something that I can actually manage and then I'm going to feel better at the end of the day when I can check off that block that I've actually accomplished something. It feels pretty good. In fact, I'll even sometimes write down things on my to do list that I did. I forgot to write it down. I did. I write it down, then check it off. Peter Koch: Just so you could feel good? Randy Klatt: It feels so good. Peter Koch: Because sometimes it's the only thing that you've got done on your to do list. Randy Klatt: Well that that can be the case. And I understand environment can interrupt all this in a heartbeat. But if you don't start with a plan, if you don't have some kind of structure around it, you'll just be treading water forever. So I think this will really help everyone. Peter Koch: So let's talk a little bit about the ER part of S.M.A.R.T-ER goals, because those are two words tacked onto the end of the original acronym that hadn't always been there. But I think are fairly relevant to talk about, especially today and how fast paced business goes. So it's evaluated and reviewed. So [00:41:00] did you want to talk a little bit about the meeting of those two in the context of the smart goal? Randy Klatt: Sure. And it makes perfect sense once you've reached the end of that timeframe. So you've done S.M.A.R.T. Maybe we should do something else to evaluate how well it went if we made it or not. If the goal was successful or not, it's probably a good idea to evaluate the process. Did we learn anything along the way? If we did. Let's incorporate it into future training so that we can be even more successful down the road. So we should have an appraisal of our goal and how well it went and what we had to do to get there or perhaps why. We didn't make it. So that's the E in the evaluation process. And then the review is in a similar vein. Let's reflect upon it and we can adjust next year's goal. We've done some evaluation. We learned these things. Now as [00:42:00] we review and plan for next year or next month or next quarter, maybe we do need to change some things to make it a more realistic goal. Or we can push a little bit harder. Maybe we can be a little bit more aggressive because we learned this was actually achievable. So it's a good thing to add. Make it a smartah goal. That's how we say it in Maine there is no R. So that makes it a little bit tough, but it makes for a more closed loop process that we've now come full circle around and we're ready to go again for next year. Peter Koch: And I think that's a good framework for when I was listening to you about talk about evaluated. I thought about it could uncover those unintended consequences of your goal setting, like you might set a goal that excellent for the company. But as it trickles down into some of the different departments. There was an unintended consequence that was not healthy for the company. [00:43:00] It might have triggered a cultural change someplace where because of the way the goal was established or it was for lack of a better term, sold in that department to the people. It didn't go over very well. So that caused people to maybe not report injuries because they felt that they were going to be the ones that were going to make the company not achieve the goals. So they pulled it back. They didn't want to do that. So they let things go instead of being more open in their discussion, in their reporting. So evaluation can help, especially if you don't achieve the goal, can help look at or uncover those unintended consequences. And even if you do achieve the goal to look back and say, all right, so these are the reasons that we achieved it, that's really good. And then reviewing it to see if we can use those same tools again for next year and maybe, like you said, push a little harder or pull back a little bit and say, yeah, it wasn't really [00:44:00] realistic to say that we're going to go from one hundred injuries a year to 10. So we need to do something else for next year. So we're going to look at it in a little different way. And we only made it down to 80 injuries. So let's say we can take it now down to 50 instead of all the way back down to five. So it's a good, like you said, closed loop. It's a really good way to make sure that you are cycling your S.M.A.R.T goals or cycling your goals, that they are part of the company's overall health. And part of the company's overall success. They should always be part of that. If you're not, they're not there to help your company be successful, then it's not the right goal to have. Randy Klatt: Right. And if you as you evaluate and review, you may find some things that weren't great and other things that didn't you might have met your goal. But we can still eliminate some of the things that didn't work very well and replace them with something that did when you were talking there. The thing that came to my mind was back belts. Let's give everybody [00:45:00] a back belt because then we're going to reduce back injuries. Great. That's our S.M.A.R.T goal. Everybody's going to get one. It's measurable because they have it or not. It's assignable, each individual. It's realistic because we just bought it and we gave it to you its timeframed I guess in that sense that you're going to wear it all everyday, all the time. We find out later that didn't work. So maybe we should have evaluated and reviewed a little bit more often to really decide if that was a good idea. So pieces of equipment, particularly, we think they're going to be great and well, turns out maybe they weren't. So that evaluation process might be really important. Peter Koch: Yeah, very true. So just to recap here, before we get into our last section is a S.M.A.R.T goal, has a segment that's specific. It's measurable. It's assignable or achievable depending on what a you use. It's realistic and it's time related or it's in a box of time. It starts and it ends there. It's not one that just keeps going forever and ever and ever. And [00:46:00] then when you get to the end of that timeframe or you're within that cycle, there's an evaluation period and then there's a review period for it. So you can keep that goal going so that you can achieve the health of your company. So specific, measurable, assignable, realistic time related, evaluated and reviewed is the S.M.A.R.T.E.R acronym and just the review. Did I miss anything in there? Randy Klatt: No, I think you sum that up quite well with the last thing. The last statement we should try and make there is that it is not merely setting those goals to guarantee your success. It actually takes work. It's not a panacea here. So set the goals. And if. If you don't make it, if you set a goal with the S.M.A.R.T format and you don't make it, it's not really a failure of the model. It's a failure of what you implemented. So let's rework that in that. Make it S.M.A.R.T.E.R for next year or next quarter, next [00:47:00] week. And I think you'll find continual success if you continue that process. Peter Koch: It is interesting. I'm just reflecting back on a couple of conversations we had before the podcast. And we're talking about working with safety committees and setting S.M.A.R.T goals. And you get done with a smart goal and there's a sigh of relief. It's done. We set the goal. Yeah. But now the work starts. This is the time. What you've done is you set the roadmap for success. It's like getting, you know, putting your destination into Google Maps and then sitting in your driveway going. I hope I get there. No, you've got to actually follow the path. Follow. Take action. Follow the path and make sure you're always looking back at the goal so that the action is targeted. And that's a really important part to remember. Randy Klatt: Perfectly said. And that prompted my thought of safety committees, because I see a lot of them and most of them are failures. And it's because they come to a meeting. [00:48:00] They talk a little bit about safety and then they don't do anything until the next meeting and they do that twelve times a year and nothing really changes or happens. So if I were the leader of a safety committee, I would say, let's meet today. And in this meeting, we are going to assign a S.M.A.R.T goal project to every one of you. So in the next month, there's a time part of it. I want you to do this, this and this. So it's specific, measurable, assign it to you it's realistic, timely for the next meeting. And those are all activities that you are going to conduct in the workplace. And there are millions of them that we could think of but report back next month as to how those things went. And that might be actually a successful safety committee. Peter Koch: Yeah. Randy Klatt: It's not about the doughnuts that you get at eight o'clock in the morning on that one Monday a month. It's about what you do between the meetings and using the S.M.A.R.T format will really help people understand what to do. Peter Koch: Yeah, really good point. [00:49:00] Which brings us to our challenge. So I think that our listeners out there take this challenge. So go home or go back to your place of business and make a S.M.A.R.T goal. Find something that you want to change. Might be something at work. Could be productivity or quality based. Something at home. Might be something on your to do list and make a smart goal for that. Make it specific. Figure out a way to be able to measure it throughout the time that you're going to measure it. It's going to be assigned to you. Or maybe if you're a supervisor, you might assign it to someone within your team. And then as you talk to your team or think about it yourself, if it's your goal, is it truly realistic for you to do that? So make that smart goal and then follow through with it. Take action to see if you can achieve it, see if using this can actually make your goal setting process a little bit easier. Or at the very least, a little more structured so that you [00:50:00] can come up and actually be successful. One of the comments I make when I talk with business owners is it's great for you to have this goal of having fewer injuries. Fantastic. And if we get to next year and we're sitting here successful, that you've had fewer injuries. But you look back and you can't figure out why you got here or how you got here, then it's an exercise in futility because you can't replicate it. So a smart goal will help you to be able to replicate success if the smart goal is created correctly. So take that challenge. And if you've done that and you want to share your story, your success with us, go back to the MEMIC.com/podcast and leave us a comment there about what the S.M.A.R.T goal was and how successful you are with that. And we'd love to see how many responses we get from that. So please take that challenge and see how it functions for you. So, Randy, the last part for [00:51:00] you. Where can our listeners find some more resources about smart goals or developing goals overall? Randy Klatt: Well, certainly I would be remiss if I didn't recommend MEMIC's Web site and our safety director, which has hundreds of documents in there related to projects, checklists, inspection information, all sorts of tools that can be used to help you formulate your own goals. If you really want to just know more about S.M.A.R.T, well, do what everybody does. Go to your computer and type in S.M.A.R.T goals in your Web browser and you'll earn your search engine. You'll find plenty of information about it. Some of the different formats, S.M.A.R.T versus S.M.A.R.T.E.R, and those other letters that sometimes represent other words like attainable or achievable or is it assignable and make it fit for you. There's plenty of information out there about it. Bottom [00:52:00] line is, I want you all to figure out a way to make it work for your business, for your activities, personal or business. And make this place a little bit safer. One goal at a time. Peter Koch: Excellent. Randy, thanks. So that about wraps up our Safety Experts podcast. And thank you, Randy, for being here today and sharing your expertise with us. Randy Klatt: My pleasure. Peter Koch: Today, we've been speaking with Randy Klatt, CSP director for Region two loss control at MEMIC about S.M.A.R.T goals and its effect on workplace safety on the MEMIC Safety Experts podcast. If you have any questions for Randy or we'd like to hear more about our particular topic on our podcast. E-mail us at [email protected]. Also, check out our show notes that MEMIC.com/podcast where you can find links to resources for a deeper dive into this topic. Check out our Web site, MEMIC.com/podcast where you can find our podcast archive. While you're there, sign [00:53:00] up for our Safety Net blog so you never miss any of our articles or safety news updates. And if you haven't done so already, I'd appreciate it if you take a few minutes to review us on Stitcher, iTunes or whichever podcast service that you find us on. If you've already done that. Thank you. Because it helps us spread the word. Please consider sharing this show with a business associate friend or family member who you think will get something out of it. And as always, thank you for the continued support. And until next time, this is Peter Koch reminding you that listening to the MEMIC Safety Experts podcast is good, but using what you learned is even better.