OSHA’s Top 10 and How they can Affect your Safety Program with Stephen Badger
MEMIC Safety Experts - Podcast készítő Peter Koch - Hétfők
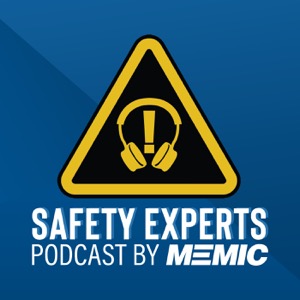
Kategóriák:
In 2020, Fall protection was once again, number one of OSHA’s Top Ten most frequently cited standards. On this episode of the MEMIC Safety Experts Podcast, Steve Badger, CSP, OHST, and Safety Management Consultant with MEMIC breaks down OSHA’s Top 10 and how it can be used as a tool for continuous improvement of your safety program. Peter Koch: [00:00:03] Hello, listeners, and welcome to the MEMIC Safety Experts podcast, I'm your host, Peter Koch. Well, we all make lists. I don't know about you, but I love to check stuff off my list. For me, it represents an accomplishment or at the very least, something I don't have to worry about anymore until, of course, it resurfaces on my lists again, lists tend to be an important part of any safety management process, and they can help keep us on track for the myriad of different topics, hazards and exposures that must be addressed by our teams every day in the workplace. It can be overwhelming about the number of things that we have to manage. So lists become an important part and sometimes we generate lists to help us focus our limited resources and energies. So consider hazard or injury mapping. These are two great ways to generate and prioritized injury prevention and hazard mitigation [00:01:00] efforts and strategies. Well, if you're not sure what those two things are, we can put some resources in the show notes. But this is not a podcast about hazard and injury mapping. We're talking about lists today and specifically OSHA's top 10 list. So OSHA has a myriad of different lists and their lists can also help employers and business owners find a starting place in workplace safety. So to help us with that today on the podcast, with me is Steve Badger, CSP, OHST and safety management consultant with MEMIC. Steve has more than 20 years of experience working with the paper, medical, sterilization and construction industries. He's also an authorized instructor for the OSHA Institute in Manchester, New Hampshire. Steve's experience in different industries and workplace safety, as well as his connection to the OSHA Institute, has allowed him insight into OSHA's top 10 lists and how they can be used to help us focus on the right areas [00:02:00] and overcome some of the barriers to enhancing safety in the workplace. So, Steve, welcome today to the podcast. Steve Badger: [00:02:08] Thank you, Peter. Thank you very much for having me on here today. And just a little bit about myself and my safety history. I started way back in 1986. I worked for Johnson and Johnson, and that was my really my first exposure to safety. And, you know, what we had to do. And the very first part of it was hazard communications and, you know, those things called material safety data sheets that just came out of nowhere supposedly. And, you know, that had to put together a program. And you have to think about the fact we didn't have a lot of computers back then. We didn't have a lot of resources back then to be able to go in and look these things up. We had to call people. And if we were lucky, we had a thermal fax that we could have somebody fax something to us. And it was a very difficult process when you worked in a laboratory like I did, where [00:03:00] there was a chemical part and there was also a microbiology part. And, you know, in trying to put these HAZCOM safety data sheets and programs together. So that that was that was where I get started with that. And then I moved back to Maine after that. And I worked for an environmental safety company doing lots of air testing and air monitoring and industrial hygiene related stuff. Steve Badger: [00:03:22] Then I moved back out of state again, went down to the southern part of the country, down to Kentucky and Tennessee, and did a lot of work at the Tennessee Valley Authority Plants doing industrial hygiene, monitoring and safety related to that. Shortly after that, I came back to Maine again and did some more work in the environmental field and started doing a lot of work in the paper industry, doing safety related job safety analysis and things like that for the different companies that I worked for. And then a while after that, I started as the safety director for Fisher Plow, which gave me some industry related [00:04:00] background, which was really interesting. You know, to see a snowplow being made is something that we take for granted every year here in the northeast part of the country. But there's a lot that goes into that, a lot of safety and environmental concerns there. So and then, of course, I've been with MEMIC now for about ten and a half years as a full time employee. So, you know, I feel my background has been varied and it really has helped me in the years. Peter Koch: [00:04:26] Yeah. It really kind of rounds everything out when you have that experience in all those different industries and makes you be able to I think at least that on my side, to be able to appreciate some of the challenges that a particular industry might have with either compliance or managing safety within their particular industry. But tell me a little bit more, because I know working with you over the last 10 years when I kind of think about OSHA and I want to have kind of an interpretation of maybe what a standard says, especially around the environmental [00:05:00] side of things or HAZCOM side of. Things I tend to think of you and I go back to you and I start thinking about, well, what would Steve what's Steve's got some insight into that maybe he can give me a little guidance in those areas. So talk to me a little bit about kind of your experience with OSHA and how you became, I guess, as interested as you are in the standards and then kind of going through their lists. Steve Badger: [00:05:24] Sure, absolutely. You know, my interests have always been and I'm a numbers kind of guy and I like looking at, you know, these lists and frequencies and, you know, and how these things tie together with the frequently cited standards. How do they apply to the real world? You know, how do they apply to the injuries and incidents of that happened out there? You know, is there any correlation to it? And we certainly can talk about that later on as we go through this. But, yeah, that was my interest was really looking at and trying to figure out, you know, why are these top [00:06:00] ten violations? Why are they there? And, you know, is OSHA focusing on these things or is it these things that they see every day is they're driving from point A to point B or they get a complaint or something. And so, you know, trying to figure that out, you know, is really important. And we certainly can delve a little deeper into that is as we go through this. But, you know, it really gives us an insight as to what hazards are out there. Peter Koch: [00:06:28] Yeah, perfect. And OSHA has tons of lists as we start to go through. And they really become a good repository for us for numbers as and they take numbers from the Bureau of Labor Standards and they pull them together and they analyze them and try to figure out sort of where some of the focus's are. And one of those lists we're going to talk about today is the top 10 most frequently cited standards. So why don't you tell us a little bit about what are the top 10 most frequently cited standards and where do they come from, [00:07:00] where they derived from? Steve Badger: [00:07:02] Sure. Certainly the number one and it has been number one most years, certainly within the last 15 years, is fall protection or the lack thereof. And most of that comes from the residential construction. And in a lot of that is because, you know, is you know, is complaints are made war as OSHA happens to be driving by. They're going from point A to point B, they see somebody in an imminent danger situation, meaning that, you know, the worst hasn't happened yet. They have not been injured, but they are in a situation where they could be injured or it could be a fatality if the person should fall. So that's the number one citation that's out there. Number two, which is near and dear to me, is the hazard communications and hazard communications for the general industry side of things. It's always been number one for the last 15 years in [00:08:00] the overall list. When you combine the two together, it usually comes in second or third. And typically that has to do with one not having a written program. It's usually, number one, not having the safety data sheets, as we now call them, in place, and people just not being trained. You know what are the hazards of these chemicals? Number three, this past year was respiratory protection. And there's a whole host of reasons. Again, take a look at what was going on in our past year, you know, with covid-19 and, you know, and other issues and the difficulty of getting respirators. A lot of people took some shortcuts with respiratory protection. Steve Badger: [00:08:41] Maybe, you know, some of those were things like not having a medical clearance to be able to wear a respirator. That was a big one. And again, not having a written program in which would have indicated to them that they needed to do these things, scaffolding came in number four. You know, scaffolding is one [00:09:00] of those things in construction and general industry that people use to get to upper heights, to be able to access something that they might not be able to get to from the ground. And there's a lot of rules and regulations around scaffolding, and it's very easy to make a mistake when it comes to scaffolding. Ladders was number five and typically with the ladder use, it was people not using them appropriately. And as most of us know, there's right ways and wrong ways of dealing with or handling ladders and how we access them and how we secure them from falling. And, you know, that message just doesn't seem to get out there sometimes. Number six was lock-out tag-out or controlling hazardous energy. And this one has more than just electrical implications. This has to do with pneumatics and hydraulics and lots of other types of hazardous energy that can seriously hurt or killed somebody. Number seven this past year was powered industrial trucks or forklifts. And typically [00:10:00] the citations that went along with that had to do with the, you know, the operators not being properly trained or the authorization from the employer, even though they might have been trained, they weren't authorized to use it, you know, in doing their daily inspections to make sure that that powered industrial truck is actually safe to operate. Steve Badger: [00:10:20] We get to number eight, which was, again, a fall protection related issue. And in this case, here, it was training requirements and these training requirements, this had to do with not having a written program, not doing what we call training that is documented by a competent person that is not a certified training. And so there was a lot of citations. So between number one being fall protection and number eight, there was nearly 7000 citations alone just in those two areas. Number nine, was eye and face protection, personal protective equipment and again, these are very important [00:11:00] ones because we only have two eyes and if we're not protecting our eyes, you know, we lose something there. And so there was a lot of those types of citations. And then number 10 this past year was machine guarding. You know, we talk about, you know, guarding on pulleys and saws and all kinds of different types of machinery that has nip points and places where people could get their hands caught or their arms caught or some other part of their body or something they're wearing gets pulled into that piece of equipment. So, you know, it certainly is something that we you know, we could spend a whole day talking about just machine guarding because there's so many different issues around that. So that really rounds out that top 10. Peter Koch: [00:11:44] Yeah. And it sounds like as we start to look at each of these top fall protection, hazard communication, respiratory protection, scaffolding ladders, lock out, tag out forklifts, fall protection again eye and face safety or PPE and then machine [00:12:00] guarding. You know, as we start to look at that long list, there's a lot that goes into each of those standards. And it seems that OSHA is you know, those citations are coming from particular parts of those standards that employers tend to miss. And I think that's one of the important things that we can think of this list as it is a reminder that, hey, these issues are out there. And, yes, they're coming from citations and OSHA is doing their enforcement process and finding these citations that way. But really, it's a good reminder that this happens all over. You know, if you have someone that uses ladders within your facility, know that Ladders was number five this year of the most frequently cited standards for OSHA. And if you have ladders, there's probably something that you can do to improve in that section. So ladders or utilizing [00:13:00] this list as sometimes a guide or a check to say, hey, how am I actually doing? How would I stand up as an employer for workplace safety based on this year's standards? So let's think about this. So this was this was from 2020, correct? The list that you just read off was from 2020. Steve Badger: [00:13:23] Yes, that's correct. This is for fiscal year 2020. So I caution people, if you go out there and you're looking for these and these lists from other sources, maybe a magazine or maybe some other online service, you just have to be careful because sometimes these numbers don't seem to match up because they're doing fiscal year versus calendar year. And so the numbers can be a little bit differently because the fiscal year for 2020 ended in on September 30th. So we had several months after that to where some of these numbers may not match up. And [00:14:00] you're looking and you're going, wait a minute, you know, how can it be that much different? And it is because of the calendar year versus fiscal year. Peter Koch: [00:14:06] It's a really good point, especially if you're trying to prioritize something and say, well, where do I want to focus? I want to focus on the place that maybe has the most frequency and it doesn't line up. So that's a really good point. Let's talk a little bit about because this is not the first year that has done this. They've done this for quite a while and have put together these lists of the top 10 most frequently cited standards. How does this year's lineup match up to say what happened in the past? So are they the same standards that keep getting cited all the time? Or are there significant differences from year to year? Steve Badger: [00:14:45] Yeah, it's a great question because, you know, when you look back, I mean, just for an example, in 2011, the top three citations frequently cited violations were fall protection scaffolding and HAZCOM. [00:15:00] 2012 fall protection HAZCOM scaffolding, you jump forward a couple of years to 2016, fall protection HAZCOM scaffolding. So as you could see, these things do not change greatly from year to year. That top 10 tend to stay top 10. Now, there is some movement within that in this particular year, you know, for fiscal year 2020, the biggest mover within that was the respiratory protection. And as I mentioned, I think a lot of that was probably had to do with, you know, covid issues that people, you know, what are you giving people respirators because of the fear of somebody catching it or passing it along to someone else. So there was a lot of those type of issues, and most of those came because of initially just giving somebody a respirator and not making sure that they're medically cleared to wear it, which is, as we all know, could be a pretty dangerous situation for anyone that has any breathing difficulties, Peter Koch: [00:15:56] As could many of these standards. If you think about [00:16:00] it, especially as you have mentioned, as you're describing some of the citations, many of those around training or authorization and OSHA as well as myself. And I think you personally as well think that there's a responsibility on the employers part to not only choose the people that should be doing the particular tasks correctly, but then authorize them to do that task, give them permission to do that task. And then the employer has a responsibility to provide the appropriate level of training so that they can be competent in the task that they're doing. And part of that is understanding the hazards that they're exposed to and the controls that need to be in place. And respiratory protection is a really good one. Because you put a respirator on and you see it all the time, you know, people will wear a paper mask, respirator, sweep and dust up in the shop someplace or they'll have a full face respirator on with. [00:17:00] And what you can see is their beards sticking out underneath the bottom of it. So they've understood that there's a hazard. They're utilizing a particular piece of equipment to help protect them from it. But they're not really understanding the limitations of that piece of PPE. So they're using it incorrectly and probably or possibly putting themselves at greater risk for the hazard that they're exposed to. Steve Badger: [00:17:28] Yeah, absolutely. With the respiratory protection, it can give you a false sense of security that, you know, it's doing something for you. Whereas like you mentioned, you know, somebody's beard is sticking out from their respirator. That human hair is many, many times larger than a lot of the particles in the things that were inhaling. They get down deep into our lungs and cause the infections and those type of issues. So wherever that hair is sticking out, there's that much less protection that we have. And so it does give us a [00:18:00] false sense of security. Sometimes if we're not properly fit tested, we're not properly trained. To even put it on can be a big issue because that was something I always used to do with respiratory protection training. Was just hand some of your respirator and tell, OK, put it on. And, you know, probably half of the people would have it on sideways or backwards or, you know, upside down because they just didn't understand how that was to go on. So you can imagine with the covid-19 issues and, you know, respirators just being handed out, there was probably a lot of people wearing those incorrectly. Peter Koch: [00:18:33] Yeah, I can totally imagine that. And then the same thing happens with fall protection. You see that often people using ladders incorrectly, people using harnesses incorrectly. And some of it stems from inappropriate training or lack thereof. Some of it stems from not having the right equipment and some of it stems from possibly ignorance around what the hazards are and the limitations of that particular equipment that they're handed given or that they've [00:19:00] brought themselves to the job site sometimes. So it's interesting if and if you go back to 2011 and fall protection in 2012, fall protection 2016 fall protection, and here we are again in 2020 fall protection is number one HAZCOM number two. To 2016 HAZCOM number two, 2012 HAZCOM's number two. Why are we seeing the same, I know you're not going to have an official, you know, Nostradamus like a predictive answer here. But I guess in your opinion, why are we seeing the same citations over and over and over again? Steve Badger: [00:19:45] Yeah, I think there's a few really important reasons that I think sometimes it comes to, you know, lack of knowledge, you know, people, you know, they received these citations and they and they're, you know, doing work. [00:20:00] And so we'll pick one here has the communications and they buy a chemical, they don't realize that, you know, even though you go to, you know, your local hardware store and you buy this chemical, that you have to train people how to use it properly. And so there's some of that is lack of knowledge when it comes to things like fall protection. Sometimes, you know, people are in that mindset that, you know, this is the way we've always done it and we haven't had any serious injuries before. We've never had that, you know, that big issue that has come up. So they don't tend to change until there's something to motivate them to change. And so it could be an injury. It could be a citation. Sometimes people worry about the cost. You know, these you know, they're always fearful of, you know, they have their own business. Steve Badger: [00:20:50] And if we put, you know, all this money into fall protection, you know, is that going to leave anything left for the business, you know, profit wise? And I always talk to people about that [00:21:00] and let them know, look, you know, can you afford the cost of somebody getting injured? You know, that's going to be a much greater cost to you than buying and training people how to wear a harness, you know, appropriately, you know, that personal fall protection stuff. So, you know, culture. Culture is always a big one that we always talk about, because sometimes people just, you know, don't have that culture within their company that helps them understand from the top down that, you know, your safety is our number one goal. You know, it is. And, you know, sometimes people will say it's number two or number three goal for a company. But, you know, the companies that have the best cultures, they understand that their workers, their employees are their number one asset. And if they don't protect those people, they are going to be in trouble. Peter Koch: [00:21:54] Sure. I think that's those are all good, good insight into why we keep seeing [00:22:00] it and when you really think about it again. So if you take those factors, it could be culture, it could be cost, could be motivation, could be something else that's driving someone to not take a step in the right direction. We're also seeing, I think when we can talk about this next here we are seeing the same citations or the same categories of citations show up because they're the most frequently people are exposed, the most frequently to these things in the workplace. And that shows up. I think, unfortunately, as we start to look at our lagging indicators, they show up in our injury statistics. So can you talk a little bit about maybe how these citations correlate to or these standards, standard citations correlate into injuries and maybe what BLS or the Bureau of Labor Statistics might show for us? Steve Badger: [00:23:00] Sure, [00:23:00] absolutely. You know, as I mentioned earlier, I'm kind of a numbers guy, I like to look at the numbers. And in this case here, if you take the data that came out of the Bureau of Labor Statistics for 2019, when we look at construction, you know, residential injuries, fatalities, that happened because people did not have proper fall protection. There were more than two thousand seven hundred and ten injuries just in that year of 2000, 19 from people falling to a lower level. There was also seven hundred and eleven fatalities, which was the number one thing that caused fatalities in construction and it is every single year. So 711 people that went to work last year, that did not come home. So it absolutely correlates to these citations. Another example of this is exposure to harmful substances in the environment and which is covered by hazard [00:24:00] communications. There were over 640 fatalities related to that. People using chemicals and think bad things happen, whether it was overcome with the chemical, the vapors or the gases that were related to that. Or maybe there was a physical hazard, something exploded or burned and caused that type. And then looking at respiratory protection number three in 2019, which was where we started this covid thing, they were five hundred and thirty three violations just on no medical evaluations. And so when you think about that and how many people may have been injured from that, you know, is hard to tell because sometimes those numbers don't always translate to the Bureau of Labor Statistics. But you can see from these numbers that they really do tie back to this top 10 citations in a very disturbing way. Peter Koch: [00:24:59] Sure. And [00:25:00] it's really interesting. I just I just pulled up while you were speaking there. I went on to, you know, your favorite site, Google. Right. And I searched OSHA top 10 most frequently cited standards for 2019. And so you related that in 2019. And residential construction falls to the lower level, generated twenty seven hundred or so injuries and over 700 fatalities. Well, guess what? The top citation was in 2019 fall protection. And there are, you know, upwards of 6000 different citations for fall protection, just the general requirements. So not providing or not protecting the worker from the unprotected edge at some point in time. And then number two, so the second point, you had so exposure to harmful substances and environments of 642 fatalities. Hazard communication was number two in 2019 with 3600 citations. [00:26:00] So it's substantial. There's a strong correlation between what we're seeing as the top 10 most frequently cited standards and that lagging indicator of injuries and fatalities. And you talked about earlier, like, why do we keep seeing the same ones over and over? One of those was lack of motivation until there's an injury or a citation and then we come into compliance or we step up our game a little bit. But predictively, I think and as a safety guy and I like numbers, too, maybe not quite as much as you like numbers, but I like numbers, too. As we start to look predictively, you know, you put these two things up here, you put the BLS information up in front of you for the injuries and fatalities around cause. And then you start to look at the most frequently cited standards. And I think you've got a pretty good roadmap of where to look in your business, at least a checklist [00:27:00] of what to look into and see how do I measure up. So how am I doing on fall protection where does my HAZCOM program look like if I got scaffolding, how does that work? And I went, who's authorized to use it? Who's authorized to set it up, how do I inspect it? Do I even know what OSHA requires for compliance around scaffolding or did I just buy it off a buddy and we're working on it because I need it. Which is not a bad thing by it. However you need it. If you need that tool to do your job, awesome. But then understand what the limitations are and where you should be focusing in order to keep your people safe. And again, so you want to get the biggest bang for your buck. The top ten might be a place to start for sure. For sure. Any other thoughts on that, Steve? Any other thoughts are on correlation between citations and injuries and how the numbers kind of fit together and places that employers can or things that employers can use to. Focus on. [00:28:00] Steve Badger: [00:28:01] Yeah, I you know, I think the you hit it, kind of hit it on the head there about not knowing, you know, kind of not knowing what they don't know. And that's where I think, you know, we you know, we can certainly help with that. You know, when companies come to us and say, you know, we use scaffolding and but we're not sure what we're supposed to be doing or with hazard communications, what are we you know, I can read the standard and I get very confused by it, which we hear a lot. You know, what do I have to do? So that's where, you know, we do some training. You know, we sit down with our insureds and talk about these things and, you know, try to put it into terms that people can understand, because that's all about, you know, when we talk about hazard communication, they you know, that's a that rule, that law that is in effect is the right to know law. And so you have that right to know, but you also have the right to understand. And so, you know, for the employee that's working with this stuff, they need to understand that if they do something inappropriate, [00:29:00] that bad things can happen from that. Peter Koch: [00:29:03] Sure. Perfect. I think that's great. So a couple of places to look. Look at the Bureau of Labor Statistics, their information. Look at the top 10. And, you know, certainly use your insurance carrier, MEMIC. If you have a different carrier, use them or your trusted agent partners to look out. Or maybe you're some of the industry experts that are out there to kind of get some more information on some of these areas that you might not have full knowledge of. And they can be complicated. I was looking at you know, workplace safety. There's really two components. There's the moral component to it of like I really want to make sure that all my employees go home in the condition that they came in. I don't want them to get hurt. They could be sore. They can be tired just from physical activity and labor. But I wanted to get hurt. I want them to be safe so there's their moral component. And then sometimes that moral component, you get [00:30:00] to a point where I don't really know how to do it. And the compliance side of it, the standards that OSHA put out together put there is that tends to help with that because it gives you a baseline. Here's the minimum that you can do to try to mitigate the exposure to the hazard that your employees have while they're in the workplace. So those two pieces together and certainly the OSHA top ten gives you an idea of where to focus and what's going to give you the biggest bang for your buck generally. And obviously, if you're operating a company that doesn't have hazards that are encompassed by the top ten, it's not going to give you a whole lot of help. But certainly if you do if you use any of those things, the top 10 is going to going to give you an idea of where to look and then what standards to focus on. So not a bad deal. Well, let's talk a little bit about how Osha comes up with these. You mentioned earlier that [00:31:00] there were there are different ways that, you know, OSHA might drive by or OSHA might come to your business to inspect or to look for how you're doing on the compliance piece. And it's that partnership of helping keep the American workers safe by working with the employers out there to get them to understand where some of the gaps are within their safety process. So how does OSHA come by the citations and how do they come by citing businesses for not following the standards? Steve Badger: [00:31:38] Yeah, that's great, and I'm glad you mentioned the partnership part of this, Peter, because that's how we absolutely need to look at this. This is a partnership. OSHA's job is to protect that worker, your employee, just like it is yours. And that's why it's a partnership. It's not and it should never be an adversarial type of relationship. They're [00:32:00] not there to cite you. They're not there to fine you. They don't get their you know, their funding from the number of citations that they give out. They're there to help you keep your people safe. So, you know, it should be treated as a partnership, not as a bad thing. You know, I always use the example. You know, it's like police. Their goal isn't to write tickets. Their goal is to keep people safe. And with OSHA is to ensure a safe and healthful workplace that's written into their preamble, into their you know, this is their purpose is to help create that environment. So moving on to, you know, what do how they go about these inspections is, you know, they really it breaks down into two different types of inspections. There's programmed inspections. We'll talk a little bit about that in a minute. And then there's unprogrammed ones. Now, these unprogrammed ones can be anything from an imminent danger situation, meaning that they happen to be driving from point A to point [00:33:00] B, they see somebody on a roof or maybe they're working in a trench where they're not being protected. If that trench should collapse, they could they could be crushed or killed in there. Those they call those imminent danger situations where they have to stop at those because the worst has not happened yet. But potentially it could. And so that their number one, you know, unprogrammed is these imminent danger type of situations or somebody may call them and say, hey, you know, if you know these you know, this is this roofing project going on somewhere. And, you know, there's a bunch of people working without fall protection. They absolutely are going to respond to that because we know what those outcomes of those falls can be, that they can be fatalities. Peter Koch: [00:33:51] No, I just I was thinking, as you're talking about imminent danger, there's an interesting video on YouTube, and I'm sure you've seen it. An [00:34:00] OSHA compliance officer had driven past road construction that's going on. And there's an open trench happening there. And all you can see in the video is he's already come on site and he's introduced himself and he's asking just questions like, hey, what do you doing how long you've been working there? He's asking the guy to get out of the trench, pretty unstable. The guy is pretty much standing on a pipe in the middle in the middle of the trench and within. I don't think the video goes for longer than maybe 40, 45 seconds. Within that 45 second time frame, the size of the trench start to sluff and the guy jumps from where he's standing to another pipe to get out of the way of the collapsing trench. And had the OSHA guy not been there, the person might have might have been in a lower segment of the trench and not able to jump out of the way had been buried. So that imminent danger piece is [00:35:00] helpful. And I think it highlights sometimes As an employee or as an employer, we might not recognize the danger that we're in, which is why we have standards there. So I might be really comfortable with that risk up until the time that I get crushed or I do fall or I am exposed to very hazardous chemical and all of a sudden I'm not in a place where I can work anymore. Peter Koch: [00:35:28] Let's take a quick break so I can tell you about MEMIC online instructor led training for OSHA's 10 hour construction and general industry standards outreach workshops. Taking an OSHA 10 hour construction or General Industry Standards outreach course is a great way to set the baseline for workplace safety knowledge with a focus on hazards and controls. MEMICs authorized OSHA outreach trainers take the course's attendees through the required topics for the 1910 or 1926 OSHA standards. [00:36:00]Free to our policyholders. These online outreach courses are a great way to balance the need for engaging training around the OSHA Standards and scheduling time for staff to travel to attend an in-person class. Check out the full schedule of MEMIC workshops at www.MEMIC.com/WorkplaceSafety. Now let's get back to today's episode. Peter Koch: [00:36:28] So it's an interesting it's an interesting video, I think it really does highlight how a compliance officer can, especially in an imminent danger situation, be able to help. But unfortunately, there's not that many compliance officers and they're not going to be able to drive by every workplace in order to help you be safe. So there's other ways that OSHA has from a priority standpoint in these unprogrammed inspections. And you talked a little bit about someone [00:37:00] maybe calling in a complaint or a referral that be another one of those ways to for them to be called to an inspection, correct? Steve Badger: [00:37:09] That is correct. complaints, they may be called in complaints. They maybe somebody has filled out a form and submitted it, you know, through the through their website. Those complaints they do take seriously and they certainly take more seriously those ones where someone has taken the time to fill out a form and put it in. It can be done anonymously. They get a lot of calls, quite frankly, people maybe disgruntled former employees or maybe somebody didn't get a job bid that they were hoping to get. You know, they get a lot of these complaints. So they, you know, being not many people to be out there and do these inspections, they have to pick their battles, they have to pick, you know, what ones, you know, mean the most. And if somebody fills out that form, they're going to take that seriously. Referrals can come [00:38:00] from a number of different sources. They can come from here in the state of Maine. We have safety works they may have gone into and done a walk through of a certain facility or a business and found some hazards and made sure that the employer knew about those hazards. And if they have chosen not to fix those or not to correct those hazards, they may refer that, you know, further on other referrals come from places like EMS, fire, police, where they maybe they've had to go and take somebody, you know, to a hospital to get care because they fell off a roof. So sometimes those referrals can come from those directions as well. The second most common of the unprogrammed inspections are the fatalities and catastrophes. That's where the worst has happened. Something bad has happened. Somebodies fallen off a roof. They've been killed or somebody has been put into the hospital because of a situation. And that's also one of those things where, you know, you as [00:39:00] an employer have to make sure that OSHA is aware of these things. OSHA requires that any fatalities that happen on your job site, you have to notify them within eight hours of that fatality catastrophes such as somebody being put into the hospital, you have up to 16 I mean, sorry, 24 hours excuse me, to be able to put that in. But you have to let them know that is part of the rules as part of the law, that you have to let them know about those. And so they will absolutely follow up on those things. You know, anything whether there's an amputation or somebody loses an eye, they're going to investigate that. They're going to require you to, you know, talk to them a little bit about that and what you're doing to prevent that from happening again. Peter Koch: [00:39:45] And I think for those specifically, I meant obviously imminent danger is something that's pretty obvious from a fatality and catastrophe. You know, something has happened. Like you had said, the worst has happened. And OSHA now [00:40:00] is trying to work with you not so much to point fingers and say, hey, you're doing something wrong. But, hey, let's look at your process. And what did you do? How did you, how did this come to be? Why did it happen? Because, you know, honestly, not that the OSHA standard covers all of the situations that could be out there from a workplace hazard standpoint, but in particular for the most frequent causes of injuries and fatalities. The standard if you apply the standard well, it will cover the majority of the potential problems that would cause injuries or fatalities that are out there. Catastrophe's serious enough injuries to put somebody in the hospital for a period of time. And they're really there to help you figure out how to prevent this from happening again. And obviously, they're doing it from a compliance standpoint, but they have to that's part of their mission [00:41:00] standpoint. And you can you know, if you took the OSHA top 10 standard or top 10 most frequently cited standards to begin with and started to go through your business. And how are you doing on the compliance piece? You may never get to the imminent danger inspection, the complaint or referral inspection or the fatality or catastrophe inspection. So, you know, one of the other, they can help you get to a place where the injury or fatality, either will never happen again or won't happen in the first place. Awesome. So there's one more type of inspection out there we talked about the unprogrammed, the inspections. And why don't you talk a little bit about the programed, inspections, because I think that's a pretty interesting piece because it does have more numbers involved in it and how they determine where they go. Steve Badger: [00:41:49] Absolutely. With the programed inspections, there are different. A couple of different kinds that we want to talk about first is sometimes they have a local emphasis [00:42:00] program where the local will say state of Maine, OSHA taking statistics from the Bureau of Labor Statistics or, you know, taking them from other sources that there are a lot of particular injuries in a particular occupation. And so they will take those and say, OK, we're going to focus on that this particular year here in the state of Maine. You know, at different times we've had sawmill's we've had things in the health care industry for local emphasis in what they will do is they will focus on those because they're higher than, you know, the average types of the numbers of injuries and the frequencies. The other type that goes kind of goes along with that are national emphasis programs where OSHA as a whole is a federal agency is focusing on a particular subject, in this case, one really common one is silica. The exposure to crystalline silica is a huge one for [00:43:00] them at this point, because silica is one of those things that, you know, it's naturally found mineral in the ground. People, you know, people get exposed to crystalline silica through, you know, cutting of concrete and things like that and dust and so, you know, as more time goes on, they're finding out that the levels of exposure are higher than what they should be. So as they are going along in time, they ended up, you know, doing more of these inspections and keeping the exposures down so that people aren't getting sick from this. Again, that partnership, you know, helping those employers, you know, realize that, wait a minute, this is something that is serious can make people sick prematurely and have breathing difficulties, which, you know, with silica, a good example that once you have it, you know, you once you have silicosis, it doesn't go away. It's something you have for life. So we certainly want to try to avoid that as much as possible. Peter Koch: [00:43:58] Yeah, for sure. Now, with [00:44:00] the program inspections, if I wanted to find out what emphasis programs were, were in my area, in my state or maybe what national emphasis programs were and what I would be affected by, where would I go? Where do I look that up? Because it's not something that you see a lot in the newspaper or find unless you're following safety publications, you're not going to see it all the time. So as a business owner, how do I find out what those national or local emphasis programs are? Steve Badger: [00:44:30] Yeah, absolutely, the best place to take a look for these are is at the OSHA.gov website, www.OSHA.gov for government is absolutely the best place to go. And if you do a search when you go in there, they have a very, very good search engine for their website. And you go in there and you plug in local emphasis or national emphasis programs, you will see you there will pop up and tell you different [00:45:00] ones and even some past ones that they've looked at, you know, previously. And then maybe now they put an end to it. You know, maybe they're focusing on something different to, you know, a different type of industry or something. But that is by far the best place to look. Some of the trade magazines will have some of that information, but it doesn't really go into why they're focusing on those particular things as much as OSHA does. Peter Koch: [00:45:25] Good. I think that's a good place. So. OSHA.gov, good place to go. I know I go there fairly often as part of my job and I guess as a safety, as a safety consultant, you're going to go there as a safety person at a particular facility. It might be a good place for you to check out to. I know quite a while ago here in Maine, I know that one of the, I Can't remember if it was a local emphasis program or a national emphasis program, it was an emphasis program around amputations for metal [00:46:00] fabrication facilities or metal fab businesses. And the employer that I was working for at the time had fabrication shops. So we had employees that were actually working under that classification. And I remember getting a letter saying that, you know, chances are because of the national emphasis program or because of the emphasis program for metal fabrication facilities, an inspection may occur. So you get notice right in the program inspections. If you have employees that fall under that classification for the work that's happening and you may get a letter in the mail saying that you might get inspected, it doesn't mean you're going to get inspected, but you very well might get inspected. Steve Badger: [00:46:50] Absolutely. And, you know, if you do get that letter, that doesn't necessarily mean that you've done something wrong. I always like to point that out as well. Just because [00:47:00] you're in that particular class code or that particular industry, they're going to try to see as many of those industries as many of those businesses as possible within that period of time that that emphasis program is open. So, yeah, I always like to stress that, that it's not just because you've done something wrong, it's just because you're in that particular industry. Peter Koch: [00:47:22] Yeah, right on. I think it's worthwhile just spending a minute or two here about if an inspection does happen, if she shows up on your job site for whatever the inspection priority is, could be imminent danger could be because you called them for a fatality, could be because it was a referral or you might be part of the program inspection, sort of what happened. So I guess if they show up, they're going to provide proof of who they are. They are they're required to produce their identification, their badge and state the purpose of what's going to happen and then really have an opening conference with you to tell [00:48:00] you what's going on, why they're there. And one of the things that will probably happen, I mean, it doesn't happen all the time, at least in my perspective. But you might actually have a request from the OSHA compliance officer for you to hand over, give them five years of your OSHA logs. Now, I think it's there's some pretty good data in those OSHA logs. But do you have any insight of why OSHA wants to look at those OSHA logs and maybe how those OSHA logs can be used as the employer as a as a good place to continue their safety efforts? Steve Badger: [00:48:41] Yeah, absolutely, you know, and I'm glad you again mentioned about the partnership thing, because that is where, you know, that partnership, you know, begins when they come on the site after they've been identified themselves. And, you know, in that, you know, that relationship is very important to build on from the beginning, that, again, they're not they are their [00:49:00] purpose is not there to fine you or to berate you or, you know, make you feel bad about what happened. It's to find out what did happen. And so that's kind of where this the OSHA logs come into play as well as because they want to know, you know, they want to look at these five years, you know, sometimes they don't. But they want to see what types of injuries you've been having as a business and are there like repeated numbers of injuries of certain types, like, for instance, you know, if you have a large number of hand cuts, we'll say each year. You know, you you've had, you know, in this department or that department year after year, you're seeing that that's going to kind of indicate to them that you are not controlling that hazard as well as you should be. Steve Badger: [00:49:47] And so they're going to look for those type of things and point those out and say, OK, let's focus on this a little bit. I see I see them also look at like hearing related issues where, you know, there's been hearing loss. And [00:50:00] if there's multiple people that have had a hearing loss within your industry or within your company, what are you doing about that? You know, that kind of opens the door. They'll ask some, you know, some questions about that. But again, it's all in that spirit of partnership that they want to help you try to identify what those issues are and how to help control them. They're not going to offer you and say, OK, you need to do X, Y, Z. That's not their purpose. Their purpose is to, you know, say, hey, you know what? This is an issue. You know, they don't authorize pieces of equipment. They don't you know, that's not their job. It's to try to help identify what those things are. Peter Koch: [00:50:40] Nice. And it seems that they're really using that OSHA log in the same way we should be, not we being safety consultants, but we as the employers should be using that OSHA log to really look at it for trends. They're looking OSHA looking for insight into how's that business doing? They might not have experience [00:51:00] in that particular business or that well in that particular industry, but they're going there and they're looking for clues as to What is the what are the challenges, what are the problem. Not so much problems. What are the challenges that the company is having around workplace safety? And then and then pointing out maybe here are some places where you can step it up a little bit and do a better job for workplace safety. And again, there's a list. It's an OSHA list. It's a list you keep for OSHA, but it's certainly a list that OSHA requiring of the injuries and illnesses that you're going to have in the log. Another pretty good list for us to use to help get ahead of the curve from a workplace safety standpoint. There's a lot more on inspections, we can do a whole podcast around OSHA inspections and what the process is and what the rights are of employees and employers, I don't think this is the place to talk about those now. I thought [00:52:00] it was important to kind of get an idea of some of the paperwork that might go around those OSHA logs. Peter Koch: [00:52:05] But let's talk a little bit about now that we Know about the OSHA top 10 list and where it comes from, that we see repeated citations year after year. We have many of the same standards are in the top 10 list year after year. And sometimes, like fall protection is going to be number one in years running. What can we do with that? Like, how do we get to a place where we can take the OSHA top 10 or even some of the other information that OSHA provides us in the lists and develop solutions around injury prevention and hazard mitigation? Steve Badger: [00:52:44] Sure. That's great to be able to follow up with this, because, you know, really, you know, first and foremost for me is the employer's mindset that, you know, I mentioned when we started out that, you know, that philosophy, you know, [00:53:00]it's too costly or, you know, it can't be done that changing that mindset to it can be done. And how are we going to do it that that is key to changing that company culture, which goes hand in hand with that. And as IO mentioned, that's going to be a top down. That's going to start with the ownership, the management. And just saying, you know what, we've had enough of this. We are going to change our belief in how we approach safety. And taking a look at this list and other lists are going to be the way to do that, to change that culture, to stop thinking about it from a lagging perspective. As you mentioned earlier, those lagging indicators changing it from reactive to proactive. How can we do these things initially? How can we prevent these things from happening? Peter Koch: [00:53:51] Have you had experience? I don't mean to interrupt. I'm just thinking about this from changing that mindset from a can't be done to a can be done. I expect you've had stories [00:54:00] with the employers that you work with where they've had a significant injury or maybe even an unfortunate fatality within their workplace. And they've had to deal with family and co-workers of the injured or the severely injured employee or the employee that's passed and their mindset changes. It goes from it can't be done to a can be done because they have a mission that's really not we see that happen often. But what we would rather have is them use these proactively, like you said, like don't wait for the problem to happen. Like, if all protections your gig, if that's what you do day in, day out within your industry, it could be construction, it could be roofing, it could even be maintenance. It could be as an arborist, it could be whatever it is. If you have a fall protection component to your business, know [00:55:00] that it's going to happen to you. So be proactive with. So have you seen that happen within the employers that you work with where you have a significant event that changes the mindset? Steve Badger: [00:55:12] Yeah, yeah, I've seen it in more than one time, you know, with more than one of these in this top 10 where either a fatality or a serious injury has happened. And that really has changed the culture, which, you know, you hate to see it happen because of that. But you're glad to see that it's being taken seriously at that point where all of a sudden, you know, somebody says, you know what, we've got to stop thinking about this the way we did 30 years ago or 40 years ago. We have to come into the 21st century and say, OK, this can be done. How can we do it? You know, I've worked with companies that work again fall protection is one of the big ones where it used to be that to put up trusses, they'd be walking the plate, you know, meaning that they're on the top and they're doing this balancing act [00:56:00] and they're trying to hold these trusses up and nail them together. And, you know, having the mindset, is there a better way? Is there a better way to do this? Well, maybe it's putting together on the ground and lifting all up in one big piece. So you've eliminated that fall hazard. And that's how we always want to approach these things, is can we eliminate them first or can we reduce that hazard to the point where it's going to be negligible or something we can better wrap our hands around? Peter Koch: [00:56:29] Yeah, that's great and again, proactively looking at it and using this list to go there and then moving further through the solutions piece, the employer is a critical part of this, like their mindset, like you said, and moving in that company culture from top to bottom. But then we get to the employees and they play a significant part in this, too. So how does the employee piece fit into injury prevention and hazard mitigation? Steve Badger: [00:57:00] Certainly [00:57:00] we want to you know, obviously when the employer wants to start with, you know, the employee awareness, so what the hazards are in the workplace. You know, these are, you know, what the hazards are. And this is what we are going to do to prevent these from happening. It may be, you know, training. It may be, you know, proper fall protection, it may be scaffold, you know, construction, training, all of these different types of training. And then, you know, the important thing is there is that the employee sees that this culture is changing, that, you know, it's really a positive step. And that's going to give them that buy in that place where they understand that. You know what? It really is up to me. My boss isn't going to be there every minute of the day. But, you know, I had this conversation with somebody recently about having respect for themselves so that they're not, you know, injuring themselves or worse, but also respecting the company as well. You know, that even though I may not have somebody, [00:58:00] you know, standing over me, making me wear this harness, that I'm going to do it because it's the right thing to do. Peter Koch: [00:58:06] Yeah. For them to get by. And I kind of think about that from an awareness standpoint. How do you use the top ten list? Well, maybe you end up using that in a safety meeting or a toolbox talk or it gets posted up in the break room. And maybe you can put up a history of showing the last three years of OSHA top ten and look at where the top ten standards are and then what am I doing or what is the employer doing about this and what are the employee's responsibilities around what we're doing? So, again, awareness, you can use the lists that OSHA puts together to help with some of that awareness to get some buy in and start some of the training, possibly with your employees. What part do supervisors play in this process, Steve? Steve Badger: [00:58:57] Sure, absolutely. Supervisors are critical [00:59:00] to this because they're kind of that middle management level where, you know, they're the ones that may be in charge of this job site or they may be in charge of a crew. And doing inspections are absolutely critical. You know, doing a walk through and making sure people are doing the right thing, that they're using their equipment, they're using their ladder properly, they're using their scaffolding properly. That's been inspected and those sorts of things. And when not which does happen, you know, when they find something being very consistent and how they enforce that, I can't stress that one enough because, you know, just because someone's been there 15 years doesn't mean that they have any special rights or, you know, or are free pass because they've been there 15 years. It's got to be a consistent enforcement, you know, just not the new guy that comes in the door or the new gal that comes in the door. It's got to be everyone. It's got to be consistent because other than that, if it's not, people are not going to have that buy [01:00:00] in. And it is critical. Peter Koch: [01:00:03] True, very true. You bring up a really good point that 15 or 30 year or, you know, 10 year employee who's been there for forever and now all of a sudden you have maybe a new supervisor who's come in, come in from a different company, doesn't have the same longevity with that company or, you know, you might have to two people that have worked together for the last 10 or 15 years. And one of them moves into a supervisory position. That consistency of enforcement or application of the standards for what you're seeing is really important. And it helps, I think, with that buy in. Right. So the employee buy in. If I see someone being treated a little bit differently than I am, if I'm getting told to wear my harness or put on my respirator or put on my seatbelt in the fork truck, but the other guy is not. Chances [01:01:00] are when the supervisor is not around, I'm not going to use it because chances are the employee is going to think that and supervisor doesn't really care that much. They're just picking on me. And so why should I why should I do it? Steve Badger: [01:01:15] Exactly. Peter Koch: [01:01:16] Awesome, and all this kind of fits in with continuous improvement. So talk a little bit about the importance of continually moving your safety program forward and maybe how the OSHA lists the top 10 list can be used for that. Steve Badger: [01:01:37] Absolutely. Yes. And I think, again, is this is a critical part of safety programs, is that it's not something you write once you put it on the shelf and blow the dust off it once a year, you know, to bring it out, it's got to be something that you're visiting regularly, that as technology improves, as you know, training improves and, you know, different types [01:02:00] of things that are out there improve that you're updating that program to meet those new you know, that new equipment. You know, respirators is a big one that they always talk about where, you know, they specifically say in the standard that they want you to go back at least annually to update your program. You want to have a program administrator that takes a look in. Is there something better? You know, and there's several of the standards that are out there that actually have that component to it that they don't want. You just having this being a static document that, you know, you sit it on the shelf and, you know, it never changes. It's going to be something that's improved. And as this top 10, you know, tying it into that is that, you know, as you know, maybe there's better and, you know, more improved lock-out tag-out devices, you know, that are out there. There's you know, it used to be that you had a lock, you had a tag and you would throw that on anything. Well, nowadays, there's equipment that you can lock [01:03:00] and tag out almost anything that's out there. So things have changed over the years. And so should your program. Peter Koch: [01:03:07] Nice. And again, using that list as a way to almost as a checklist and again it doesn't go through that list, doesn't highlight all of the standards, only the ones that are most frequently cited, which again correlates into the most frequent causes of injuries and fatalities. So it's a good list to start looking at and say, all right, in my continuous improvement process, how am I doing in all of these? And at least it gives you some sort of barometer and way to check. So maybe you have that when it comes out every year. Take a look at it, use it as a focus for a while in your safety toolbox talks. And then if you are the EHS guy or gal at the business that you're working for, maybe use that as the checklist, how we do it. Like if OSHA comes today, am I going to [01:04:00] be part of that number of the most frequently cited standards or are they going to come in and look at it? Go nope your fall protection program looks good or nope your respiratory protection looks good or HAZCOM looks good. Peter Koch: [01:04:14] And then knowing that if you miss the piece, that's OK, Continuous improvement, make a change, add that to the process and move forward. That's really great advice. Excellent. We're kind of coming to the end of the podcast time here. And I do want to ask you this question, Steve, because you've had quite a bit of experience with OSHA over the years. You're an authorized trainer for OSHA. What do you know now about OSHA that you wish you had known when you started out back in the 80s doing workplace safety and work in an industry? Steve Badger: [01:04:51] That's an interesting question, Peter. I tend to look at it the other way around. Really. There's things that I know now that I wish I didn't know then, you [01:05:00] know, you know, types of things, you know, think things like, you know, the dollar numbers that are thrown out there with the citations. I mean, to me, that that's a very unimportant number when we're talking about lists, it's not as important as, you know, what is that violation in and how do we fix it? You know, too often I see people focusing on those numbers that, oh, I got this fine for 5000 or I got this fine for 10000. Yeah, that's the least important part. It really is. And that's why I say I tend to wish that I didn't, you know, back then when I first started in safety in 1986, that wasn't a factor. That was you know, it was doing it for the right reason. And rather than worrying about those money issues, are the money issues important? Sure. But it's not something that should be the focus. You know, that's not that you know why we should be doing this. Peter Koch: [01:05:56] Right. And I think, like with any good partner, there's some accountability [01:06:00] in there. And I think from an OSHA standpoint, they have little to do around accountability. So there needs to be you need to have some skin in the game. Right. As an employer. And part of that skin in the game is going to be dollars and cents. But like you said, and I think that's a really, really great point, is the dollars and cents are not the important part of this. The focus is what part of the standard what part of that compliance? Aren't you following? Because in that non-compliance, there's a gap someplace in your program where one of Those employees that you hire, which may not have the same understanding that the rest of your employee employees do, is going to fall or is going to use a piece of equipment incorrectly. And you're going to be in that position as the supervisor or the manager or the vice president or the owner of the company to make that call to the significant other to say, hey, you know, Judy fell today and [01:07:00] I'm not sure if she's going to make it home. That's never a place where you want to be. And that's not the time to decide to make a change. I mean, it is you certainly want to stand up, recognize that and make a change, however. Do it before that, use these lists to help recognize where some of the gaps are. I guess that's might be a good place to kind of a good way to think about it for sure. Right. So we're kind of getting again, like I said, we're getting to the end. One more question for you, Steve. If someone had more questions about OSHA and their top 10 lists, where can they go for more information? Steve Badger: [01:07:40] Yeah, certainly the again, going back to the OSHA.gov website is really good because one of one of the things they do is they give you this top 10, but then they also break it down into the top five violations under each of those top 10 so that you can kind of see, OK, when like number one [01:08:00] here says fall protection, general requirements. But what does that really mean? You know, in the case, you know, when they're talking, you know, when they break that down, they're looking at the residential construction as being the number one within that particular area. Unprotected sides and edges is the second largest. And so it kind of breaks down for you what individually within those sections are the points of pain that we're looking at that, you know, you take a look at that list, that secondary list, and you say, OK, are we protecting our people from unprotected sides and edges? You know, we work on roofs that are low sloped. Are we protecting our people? This gives you an idea of one. You know what they're looking for. But two what are hurting people falls from those heights. Peter Koch: [01:08:50] Yeah, that's great. So perfect, Steve. I think that's great. So recommending people go back to OSHA and there's lots more information. We've just kind of scratched the surface there [01:09:00] of what that top 10 list can break down for us. So thank you for that. This about wraps up this week's Safety Experts podcast. Thanks for sharing your expertise with us today, Steve. Steve Badger: [01:09:12] Very welcome. Thank you. Thank you for having me, Peter. Peter Koch: [01:09:14] Yeah, beautiful. Peter Koch: [01:09:15] So thanks again for joining us. And thank you to all of our listeners out there. Today on the MEMIC Safety Experts podcast, we've been speaking with Steve Badger, safety management consultant with MEMIC, about OSHA's top 10 list and how they can be used to improve your company's safety in the workplace. If you have any questions or I'd like to hear more about a particular topic on our podcast, email me at [email protected]. Also, check out our show Notes that MEMIC.com/podcast where you can find additional resources and our entire podcast archive. While you're there, sign up for our Safety Net blog so you never miss any of our articles or safety news updates. And if you haven't done so already, I'd really appreciate it if you took [01:10:00] a minute to review us on Stitcher, iTunes or whichever podcast service you found us on. And if you've already done that, thank you, because it really helps us spread the word. Please consider sharing this show with a business associate friend or family member who you think will get something out of it. And as always, thank you for the continued support. And until next time, this is Peter Kotch reminding you that listening to the MEMIC Safety Experts podcast is good, but using what you learned here is even better.