Maine Miracle: How MEMIC Changed Workplace Culture w/ Michael Bourque
MEMIC Safety Experts - Podcast készítő Peter Koch - Hétfők
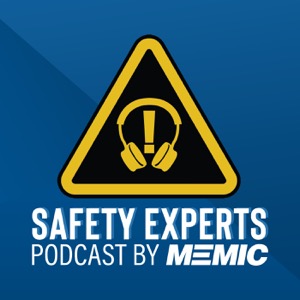
Kategóriák:
You might be thinking about how you can improve the safety culture at your workplace, but from the start MEMIC had to change the workplace culture of an entire state. MEMIC President and CEO Michael Bourque says that MEMIC was born out of crisis. In the late 80s and early 90s Maine had a terrible safety culture and increasing levels of legal conflict making it the most expensive place in the country to do business. The economy suffered and insurance companies were fleeing the state. Finally, workers’ compensation reforms were made in 1992 and Maine Employers Mutual Insurance Company (MEMIC) was created. Now with 8 offices across the Eastern Seaboard, MEMIC shares its workers’ compensation and safety expertise with policyholders across the country. Pete Koch: Hello, listeners. And welcome to the MEMIC Safety Experts podcast. I'm your host, Peter Koch. Join me and my guests every two weeks to discover new nuggets and insights while we discuss safety as it relates to us humans. Ever wonder what drives a company or even a state to change its workplace safety culture? Sometimes it takes a serious event or a series of events for leaders to recognize that change is necessary. And even then, real sustainable change is sometimes only born out of crisis. And it was in the crucible of the Maine workers' compensation crisis of the 1980s and 1990s. That MEMIC was formed. In today's episode, I'll be speaking with Michael Bourque, president and CEO of MEMIC, to get a better understanding of how a small Maine based workers' compensation insurance provider has changed the safety culture in Maine. Mike has a great big-picture perspective on workplace culture behavior and what it takes to make safety an essential part of the success of any business. Michael, welcome to the podcast. And before we dig in, can you tell me a little bit about yourself and how you came to your position as president and CEO of MEMIC? Mike Bourque: Sure, I'd be happy to. And thank you much for having me. I'm excited about the podcast and where we're gonna go with it. I think it's a great. It'll be a great resource for all kinds of people. And I'll look forward to listening to it, but not to this one, because I think I'll probably understand what happened here. So, I have worked at MEMIC for, I'm in my 25th year I came in 1995 to the company. I've been the president and CEO since September of 2017, but I originally arrived back in 1995 as a Communications Specialist. I had had experience as a newspaper reporter. Degree in journalism worked in daily newspapers in Maine and Alaska and then left Maine to go to Washington, D.C. and work for a trade association there as a PR communications person. When I was coming back to Maine. Moving back to Portland, I was looking for a job, really. I didn't know any, I didn't really even know what worker's compensation was. Certainly, didn't know what a worker’s compensation insurance company did. I didn't think a lot about safety and workplace safety at all in those in those years. And I arrived here and got a job as a communications specialist and worked in the communications area for years as a manager and a director and then took on the government relations side. So I would find myself often describing and presenting the company to people. And I think that provided me sort of a broad range, broad understanding of what happens throughout the organization, because my job was sort of to be a translator to translate for people outside of the company what the heck we do inside of a workers’ compensation company. And then actually on the other, the other way to translate for people inside what people outside make of what we do and how we do it. So, you know, workplace safety was part and parcel to the DNA of this organization. And so, I had an early chance to really learn that as somebody might who was just coming into the industry and learning about it. So I worked the last 17 years of his career for our founding CEO, and I always say that the way I learned was by keeping my reporter card to ask all the dumb questions, so I keep that to this day, actually it's very handy in this job. And it's great. You learn every day. And so that's been my career here so far. Pete Koch: That's pretty neat. So, starting as a communications guy with no background in safety whatsoever to the president and CEO. And I imagine that you that your understanding of safety. I know for me personally, like when I came to MEMIC, I had some experience in safety and workplace safety. But when I started my career in hospitality, I had no concept of workplace safety. And now I know that's evolved for me substantially over the years. How did it evolve for you? Your understanding of what workplace safety was almost being here from the beginning and seeing that that concept of safety being implemented over the years and helping MEMIC and other companies be successful over the years? Mike Bourque: Yeah, it for me, it was it was entirely a learning experience. I mean, we all know sort of the basic of what does it mean to safety and safety mean and what is workplace safety mean. And the idea that if you prevented injuries, you'd maybe reduce the cost. That seemed like that was a sensible thing. But I sort of learned the levels of safety sort of as we advance as an organization. I think we started really focusing on what are known as controls and engineering controls. How do you change either something about the work or something about how you do the work to reduce the risk and whether that's adding machine guards or getting a better machine or performing sort of early ergonomic review to make sure that how you work with something that makes sense to lifting all sorts of simple things like that to something that was much deeper, sort of cultural and behavioral things that change culture and behavior. And we were very into pretty early on at MEMIC that we were going to be changing the culture of Maine and toward a safer one in the workplaces. And Maine needed it. Pete Koch: Yeah. It seemed that it did. If as I go back and look at the history of MEMIC and the history of workers comp and MEMIC, we needed not just an insurance company, but we needed someone to come in and help really rebuild our work comp industry and then help the business groups here actually be safer because we were it, was a pretty scary place in the early, late 80s, early 90s, not just from a cost perspective, but we had a lot of challenging jobs, a lot of dangerous jobs. And that showed up in the workers comp statistics. Mike Bourque: Yeah. Pete Koch: Can you talk a little bit about some of the early problems that MEMIC saw, and why MEMIC was created overall? Mike Bourque: Sure. Yeah. Maine had among the highest injury rates in the country. It was the most expensive in the country for workers compensation. Those things tend to go together. We had a lot of old-line manufacturing we had an aging workforce. There wasn't enough investment in some of our industries. And so, you had, you know, really some old machines that were working in many of these places. And so, it got to a point in Maine that insurers refused to do business here because it was so expensive, and they couldn't accurately predict what their losses would be. And so, they began to pull out of the state. It's a mandatory line of insurance. And so, you really had what was a crisis in Maine, a handful of insurers who would insure only a few of the very best companies. And everybody else was in a pool that was known as a residual market pool. And there was sort of no incentive to be safe within that other than to take care of your people, which you'd think would be enough. But it wasn't there wasn't a financial incentive for employers. And so, you know, the state really was in a bad place. And ultimately, the governor in the early 90s, a guy named John McKernan, told the state legislature that, look, this worker's comp issue is too big of a problem. He had business owners coming to him from around the state, sitting in his office and explaining how high the costs were and how they couldn't seem to make a dent in them no matter what they did. And so, he told the legislature, I'm not going to sign this year's budget this year state two-year budget until you bring me workers compensation reform that we can agree on. And ultimately, they didn't they sort of called his bluff and he did refuse to sign the budget became nationwide news. It was on the front page of The Wall Street Journal. Maine's government shut down for a total of 17 days. There were dueling protests at the statehouse in Augusta state workers who were demanding that the budget be signed that, they weren't getting paid. They were on furlough during that period of time. And then businesspeople saying we really need to fix this worker's comp problem. And so, they finally came up with a compromise. They established like any good legislation; they established a commission to go to do the real work for them. But they agreed that they would vote on the entire package of the issue and work on it. And they appointed some really smart people who had experience and went out, looked at some other states and looked at experiences they had. And they came back with three major suggestions. The first was they made the benefits in the state for workers compensation the national average. They didn't want to be the highest. They didn't want to be the lowest. They wanted to be at the average. And Maine was sort of an up and down in various parts of its benefits structure at the time. They created a dispute resolution system within the state, which didn't rely on expensive lawyers, which the old system had and which tried to get people to mediate a dispute before they went into a sort of a court proceeding. And they establish that administratively, which was important. But thirdly, and most importantly, certainly from my perspective and I think your perspective, but I think really the state's perspective, they created caused the creation. I don't say they created because they caused it. They said it would happen. The employers had to then make it happen later. But they caused the creation of a company to be known a mutual insurance company, to be the guaranteed market in Maine, to be known as Maine Employers Mutual Insurance Company or MEMIC. And that company was established on November 13, 1992 was the date of our incorporation. And the governor at the time appointed 12 businesspeople to be members of the board of directors, the board of incorporators. And their job was to start an insurance company within the next 45 days, which they did. And you might guess that something like that that is as complex as a worker's compensation insurance company that started 45 days might not be the best organization, but because they started from a place, I think, of wanting to solve a big, big problem. And they had experience with what those problems were. They kept a focus on that. And so that was how they how they set out. Pete Koch: So, in the creation of MEMIC what was the mission? I mean, what every business has to have a mission in order for them to be that people look at their decisions and know that they're moving in the right direction. So, what was it founded on? Mike Bourque: The most important thing to the board of directors of MEMIC and remains so to this day was workplace safety, which is interesting because, you know, it isn't necessarily usually the first step of an insurer. But they set out in the mission statement of the company that workplace safety training services are mentioned long before it ever mentioned insurance. And so, they made it very clear from the very beginning that they thought that prevention of injury was going to be the way that we were going to be able to resolve the problems that Maine had in workers comp. And so, to that end. In addition to the mission, they also established an independent department, our Loss Control and Safety Department, and hired professionals within it to offer workplace safety training services alongside the insurance. And there'd be many companies that might have a loss control department or a section that might report to underwriting or any claims or even the policyholder services side. But to have it be an independent department and to say workplace safety is important regardless of cost. So cost is important. And that's what we do. We try to help employees drive down the costs. But there's a cost that's more than financial. When you talk about workplace safety and owning that sort of moral ground and feeling that importance was really that is our mission. And that's something that I think excites the people who work here, whether they work in safety or not every day and they have a part in it, no matter what. But those are things that really were established from the beginning. And give us a sense of this mission that was an important moral right. Pete Koch: I think it really takes the perspective of safety from safety is expensive to safety is essential. As part of that mission, going out and looking at new business or looking at existing businesses and trying to help them, it's not just these are your risks. This is what it's going to cost you. You've got a claims department back there to back you up, which are all critical parts to making the insurance piece work. But without establishing a way to get ahead of the injury curve to make the business better on the other end, you know, it's not a successful puzzle to put together. There's gonna be a missing piece there. Mike Bourque: That's right. I think we you know, we discovered we knew that. I think people knew that who came to work here early on. But it was a matter of sort of changing the cultural norm in the state around what it meant to do workplace safety and so starting from those engineering controls and you know, one of the early things that we did and it was sort of I think an indicator of that we were going to be maybe successful at this effort was to establish a public service campaign that was called the Partnership for Workplace Safety. Pete Koch: That's right. Mike Bourque: And we spent a fair amount of money. And there were some people there's some people who were a little concerned about that. But getting messages out into the public, to workers and employers alike, saying workplace safety is everybody's business, it's everybody's job. And the only way we're going to really tackle our problems in this state related to the cost, related to the carnage would be if everybody took some ownership of that. And so, we created this, we basically said employers and employees working together said that line over and over again and I think helped to see that. So that sort of resonate with people and understand that this was about more than more just than the dollars. There was a cultural change that needed to happen. And having mom or dad come home the way they left in the morning was very, very important thing. Pete Koch: I see that when I go to businesses, those businesses that are most successful, there is a true partnership between the management team and the employees to get the job done, not just from a qualitative standpoint or within my budget and timeframe, but safely. And those companies that have that open communication, that true partnership between the people who are doing the work and the people who are getting the work for the people to do, that there is dialogue back and forth. There is support for initiatives that employees are trying to take in order to make that job not only maybe easier, but safer to do. And that partnership is truly essential, has to be part of the culture. And I think it would be hard for an insurance company to hire a bunch of safety people in order to make that connection happen at a workplace, to go to a workplace that might not have that partnership. More of that traditional management employee relationship or not a relationship and have your traditional safety person go in and try to try to culture that there. How did MEMIC get around that? Who did they hire to help make that safety process work, make safety essential, that partnership essential? Mike Bourque: It was an important aspect in the development of the company and development of that safety and Loss Control department to hire, not insurance people with clipboards, but to hire people who actually worked in the industries where they were going to be going into the field and working with employees. We always say they come from the industries they now serve. And the idea was you had people that one knew the work. But the other side of it was they had credibility with the employees and the business owners or the supervisors in a place. If you showed up, you know, in your in your tie in some cases with a clipboard, you look like an insurance guy. And we hired people from the construction industry who knew construction from manufacturing floors, who knew manufacturing and manufacturing safety. And they could also communicate, by the way, which was a hugely important aspect, health care, same thing. And so, we found some really top flight people and they had challenging jobs. But early on, they really helped set the tone for the kind of work that we were going to do. And that's made a huge difference. It's made us. It set us apart from certainly other insurers and helped driven the success of the organization. Pete Koch: I can speak to that specifically. I'll go back to a story prior to my coming to MEMIC the business that I worked at, we were insured by a mimic. So, we had a project. I was the risk manager there. We were doing some condo development and we were going to fly some trusses a couple of weeks. So, we had asked MEMIC if they had someone to come in and do some crane safety with us. So great. Yeah. We got this guy, Rod Stanley. He'll come in. He'll help do the training for you. He'll take your crew all the way through. We'll go through all the aspects of crane safety for you and your crew. Awesome. I'm excited. Risk manager got it going. And I'm trying to sell this to the departments, and we have construction guys. We've got concrete guys. You got a crane guy and they're like, who is this insurance guy that's going to tell us how I am going to run the crane? And then Rod comes in that day and it doesn't look like an insurance guy is right at their level, is able to communicate with them. He's able to relate to the stories that they tell and before the end of the class, so at the beginning of the class, it was the stoic arms crossed both feet on the floor, leaning back of the chair. Going you need to prove to me that you have credibility. By the end of the class, there was a lot of leaning in. There was leaning forward. There were questions. People came up to him afterwards and asked him a bunch of questions about, so what about this situation and how should this work and this guy's operating it this way? And what happens if we have to do that? And he had answers, which was pretty amazing for your insurance company to have that type of resource that totally sold me on having MEMIC as that partner, because there's not only a partnership between the employee and the employer, but in order to make this thing work, there should be a three way partnership between your insurance company. If there is an injury helping on the claims side to work on your rates, on the underwriting side and then from a prevention side from the safety side. Mike Bourque: Yeah, it's a three-legged stool. We often talk about that. You need claims, you need underwriting, but you need loss control. You need safety to be part of that. And that's part of the service that is being provided with the policy. And, you know, I can't imagine selling insurance and not doing that. That's what I've grown up in here in MEMIC. And that's how we do it. It doesn't make sense to me that you wouldn't add that aspect because, you know, we've been able to do it as well as well as we have. I think, you know, we've seen these sort of really interesting-personality people come to join that department and it's always fun to go see what's going on in the Lost Control and Safety Department. Usually we've hired people who are very good communicators and know their field well. And most of the time they're not in an office. They are. Their job is to be out in the field and in peoples at work sites and visiting with people. And I always love to make contact with them to find out what they've what they've come across most recently. And I think they are they tend to be people with great curiosity and also great knowledge. And I think it's a great I think, you know, probably there was a time when having a visit from your safety loss control person from your insurance company would be something that would be dreaded. I think often while sometimes we have some tough messages delivered, delivered to people, I think often it's something that they really look forward to, that there's a resource that they have that they're going to be able to glean from and establish something that that'll help them get better, maybe more productive and safer at the same time. Pete Koch: Yeah, for sure. That piece of having safety as a resource, seeing it as a resource instead of an extra thing that I have to do, ends up making it part of your culture, starts to make it part of your culture. When I'm not thinking about did, I check off the safety box today that I where my this today. It just becomes habit, which is a neat part about the people that work for MEMIC on the safety side there. You talked about all the personalities that work within that particular group. You know, you think about Andy Wood early on with the logging group and continuing on with the logging group and having significant impact over the years with not only the cost of workers comp, but the overall injury trend for workers comp on that side. He's been able to make a great impact just because of his knowledge in the field, his credibility in the field and the support that MEMIC has given him to do all those things. Mike Bourque: Yeah, I think it's important. That's a that's a really important example of one of the ways that we started to see success tangibly occurring in the field within the logging industry. So that's obviously a traditional industry in Maine. You look at the state flag, there's a logger on one of the one of the two or a lover and a farmer. And so, you see that. And so it's a traditional industry. And people worked in it for years. And it seemed to be sort of just a given that, well, some people are gonna get seriously hurt because it's tough work. Mike Bourque: And that was something that became unacceptable to us and lots of people in the industry. And so, one of the things early on we did in addition to hiring Andy and a team of people who really work. They'd go out into Maine's Northwoods and work directly with loggers and teach them things that they thought they probably already knew. We had one who spoke French at the time because they are French Canadian logging crews that were there. And I think Andy can speak some French actually himself when necessary. But we established a standard called the Certified Logging Professional and something called the Game of Logging, which really established safe methods for felling trees and dealing with the hazards in the woods. And required certification. And we were in a place where we could do that because there were deaths and paralysis cases occurring in the woods of Maine every single year. Terrible, terrible injuries in addition to being obviously very expensive. They were hugely either life ending or life changing, certainly to the people who experienced them. And so within a few short years after establishing that, there were no deaths and no paralysis cases for many years after that. Within the state, it changed the industry in some way. Sometimes mechanization had a little to do with that. But certainly the credibility of those guys who were out in the woods, who talked to old loggers who had been felling trees forever and said, there's nothing you can teach me, and then they'd watch Andy or one of the guys fell a tree on a dime, somewhere uphill, downhill, side hill, side lean, dealing with widow maker trees that are around. They saw that there was a different way to do the work and began to understand that they were putting themselves at risk and they really could be better. And so that was an example. You know, from the very beginning, we saw attention to something that had been thought to be just inherent. That's just an inherent risk. That's how it is. We didn't accept that. And the people we worked with didn't. And that's made all the difference. Pete Koch: The logging examples a fascinating example, because the training and the certification that was done really originated from production. So, the principles that are taught for the certified professional logger are all about getting the wood in the pile and being productive. But the underlying principles for that are not only allow you to be faster, but it also allows you to be more accurate and it allows you to be safer. So, allows you more control over a standing piece of kinetic energy, basically, which is a tree. So, you've got to get it to go where you want it to go. And once I understand how it works. So, we're using principles for production that actually have a lot of underlying safety practices. And without those underlying controls to make production faster, you won't be as fast. And historically have showed that you've killed people and paralyzed people and injured people substantially. So that's a really interesting. Mike Bourque: Yeah. It's a very good point. I mean, that safety can't be seen as something that it gets in the way of production. And that was the old way of thinking, I think within Maine within lots of industries. And that's been a principle, the principle that increasing improving safety leads to increasing and improving productivity is something that wasn't obvious to people right away. But over time in industry, after industry has come to be true and they've seen it seen it happen. And so, I think those of you who talked to people who have been in their industry for a long time and they will say, I didn't know it could be done, but it can. And we're doing it. Pete Koch: Yeah. And moving that the thought from safety is expensive. And so many times when I go to an account that we've never had before, it could be in Maine, could be in a different state, could be a brand-new company. The discussion is always around safety is expensive. We've got to do these things. I have to put machine guards on. I have to hire new people. We have to do safety training. And once you get beyond that to show that there is truly a connection and that three-legged stool that you talked about before, that in order to balance your business for the long term, anybody can be successful. In the short term, I can have a super successful set of years, but I won't be able to replicate it if I don't know how I got there. And so, I might know how I did it financially. We might know how I did it from a qualitative standpoint. But if I don't get how I kept all my people saved through the program, through the production, through the years that we were successful, we won't be. So, moving from safety is expensive to safety is essential and is an essential part of any business out there. Let's take a quick break and we'll be back with Michael in a couple of minutes. Thanks. Pete Koch: Welcome back. And today, we're talking with Michael Bourque, President and CEO at MEMIC. So, Mike, I wanted to jump back in with some more questions. And in the previous segment, we were talking a lot about how MEMIC brought safety to the forefront. And it was the mission that they used to help to fix the worker's comp situation in Maine. Safety being an essential part of any business plan in order to be successful over the long term. So, we know now that we were successful because we can look back. Hindsight's always 20:20. But what were some indicators that MEMIC was on the right track? Like how did the leadership at MEMIC in those early days know that they were going in the right direction with putting an emphasis on safety and quality team or quality claims and quality underwriting? Mike Bourque: At the beginning, it really happened pretty quickly, amazingly enough. We started and I started to see rates fall by a couple of years into the company. And so, Maine had the highest rates in the country in terms of workers compensation costs and those started to come down fairly precipitously. And another indicator was all of a sudden, the insurers who had refused to do business in Maine, had all turned in their licenses, by 1997 there were about 200 of them who were back willing to do business in the state again. So, it was very clear that they were seeing something in numbers that was indicative of a better environment. So, we saw that. But the number that that set it right away were the number of lost time injuries that were down. So, in 1992, the year before MEMIC came into existence in Maine, there were 19,200 lost-time injuries in the state. By again that time 97, 98, it was down around 13,000. And those are just a raw number of claims that wasn't on a per worker basis. And that was at a time in the economy where we were coming out of the late 80s, early 90s, where there had been a low in the economy to a place where there were lots of jobs being added. So, you had fewer injuries on a larger job base. So, the rate of injury had fallen precipitously. We could we could certainly see that. And then the numbers in terms of costs were as well. We also saw that that message that we started to get out around the public service announcements that we did really was resonating, that people were paying attention and listening. And you'd see it on work sites. You'd see it my old boss would say whenever he went out someplace, somebody would see him and remember him from the ads, but then say, "Hey, look at this I'm working safely” whatever it might be. So that was that was an indication. Pete Koch: That's cool. There is a connection, though, in order for those claims to go down. Or the injuries to go down, to realize that and have the other insurers look at say, oh, there's something good happening here in Maine. And pretty quickly. It couldn't just happen because we were underwriting the right businesses or we were managing the claims because, yeah, you can manage claims costs, but you can only do so much. So really had to be the safety aspect of it that caused a majority of the success that was out there. So, there is a partnership. We talked about that partnership, the ad campaign, the getting business owners and employees to partner together for workplace safety, having a third partner of MEMIC as the resource of the insurance company. But what part did the safety consultants play in making sure that companies were working safely in the field? Mike Bourque: Well, they were you know, there were assigned customers. They had a regular set of customers, and they do to this to this day. And they were out meeting with them regularly. Their job was not to be in an office anywhere, but to be out in the field in those places and seeing things change and happen and follow up. And so are using all kinds of best practices around managing projects and all of that. And to bring new information. And so, I think they became looked upon as a real resource for those employers. And they knew we were we were serious about it. This wasn't just a one-year thing. We weren't just going to show up, you know, at the beginning first six months and say, "Okay, we'll see how this goes and then we'll send you a bill after that." We were going to come back over and over again. And they did start to realize that. I think some who didn't get it early on said you were gonna see that guy Rod Stanley again, I guess. And so they started to really understand that this was a movement that really was something that was going to be lasting. Pete Koch: That follow up, I think is key. Talk about, Rod Stanley go back to that training session. The last thing that he did before he left was say, Okay, so here's the action that we are expecting that needs to be taken in the field. Let's follow up in a week or during the project or after the project to see how you did. So, there is always that follow up, at least on my perspective. From my perspective, when I was working in the industry, that MEMIC would come back to that. And on the logging side of it, too, in order to maintain your certification, you had to have an evaluation in the field to assure that you were actually doing the or following the practices for the game, a logging in the certified logging professional. So, there is accountability built into the safety program because that key part of any partnership, in order to have a partnership, each partner has to own part of it. There has to be some accountability on that. Mike Bourque: You know, it's I think it's interesting. One of the things that followed on a few years later from the Certified Logging Professional was something we know here is the CCP, the contractor certification. And it was a program that we put in place after some really serious falls had occurred around small homebuilders. So, these are one and two-story structures being built. And there were about 2000 of those organizations around the state of Maine, and they're notoriously independent. I mean, they were in charge of their site. They knew how to do it best. And they were tough nuts to crack, there's no question. They didn't need their insurance company interfering with what how they did and what they were doing. But we put in place some pretty strict standards and then followed up. We had to add the staff to do that and invested in it. And, you know, it's very interesting. Just this past year, I was at a St. Patrick's Day party actually on an island in Maine and a guy I knew to be an ornery old contractor. He actually was an ex professional football player, ambled up to me and he said, so you're the MEMIC guy. And I said, yeah, and he stuck out his hand. I want to thank you. We're a lot safer than we used to be. And you know what we thought we were doing, but we didn't. And to hear from this guy in particular, that to me is an example of the kind of thing that happened over and over again. And, you know, at the absolute, you know, sort of grass level, I mean, it was this was right down in the weeds. And we needed to do that. And it did. And there were some people who would have were a little nervous about sort of, you know, plucking that string. I think that we thought we would, and we did meet with some people who weren't going to join us in that effort. But by and large, we've had pretty good success in helping to make that happen. Pete Koch: Yeah. That's a great story about the guy coming and saying "We're a lot safer than we used to be. We thought we knew, but we really didn't know", which is a lot about safety because how do you learn about safety? Chainsaws, right? So, logging everybody in Maine has used a chainsaw. We do logging, training or chainsaw training with occasional users now. So, since a lot of the logging in Maine now is mechanical. Most of the training that Andy is doing is for those occasional users. So, your property managers, your maintenance guys, your golf course people. So, we'll do some chainsaw safety training. So, the first question that you always ask is, so who has operated chainsaw before? Everybody raises their hand. So, who's had training before? Nobody raises their hand. Or somebody does and then you ask him. So, who trained him? And it's your grandfather or your father or... And great training, really, to be out in the woods with your dad, your grandfather in that tradition. But where is the safety coming from? Pete Koch: How are you learning that? So, to be able to give a resource and at an expert level for the industries that we're going to insure is really key. I think that's important on every level. So a company that is doing a particular type of work, whether it be hospitality or construction or nursing or logging or whatever that is, there should be people that are not just experts in what they do, but experts in how what they do can affect them. So, I have an interesting story kind of along those same lines and that that interaction with that person. So, one of the first years that I was working for MEMIC, I was doing a confined space workshop for an account. And we were in the field and we were at one of the spaces and we were learning how to use the gas meter. So, you put the meter in the hole, you take a reading of the levels of oxygen were and any flammable gases. And then it would tell you if it was safe to go in or not. And so, I got the meter down there. And I'm looking at the reading and I'm looking at it and I'm talking to the guy who does work in the hole. So, it's a relatively deep hole. It's about 15 feet and it's only about three and a half feet wide. And there's some valuing and steel parts at the bottom of the hole that he has to go in and adjust. And there's a flow meter that he has to read whenever there's water flowing through that space. So, he goes down there once a week or so does the reading. And I asked him, so how do you how do you feel when you go down there? Well, you know, when I go down there, sometimes when I come out, I got a really bad headache, or I feel nauseous and it takes me a while. But, you know, I get out and I breathe again for a while and I do good. And then I'm fine and I go on. And I look at the meter reading and we were well below the livable oxygen level down there. So, if he had spent long enough down in that space, it might have been a different story. He might not have come back out. So, from that particular interaction and then being able to show him exactly what he was breathing down there, they changed what they did. So, they moved the flow meter from 15 feet in the hole to right at the surface. So, they engineered the problem out. But that was business as usual for them, which I think is a is an essential part of what MEMIC's safety people do as they make that connection in the workplace. Mike Bourque: Yeah, it gives people a place to verbalize some of the challenges they may have. I mean, I think, you know, until you ask somebody, how do you feel about that? There may not be any reason. Well, it doesn't really matter, because I have to do it, doesn't it? Well, maybe it does matter. Maybe there is a way to fix it, to make it better. And I think we part of what we've tried to do is create the sort of safe spaces for employer employee communication around that, because we know that's vital. And, you know, I think there's more and more space for that to happen now than before. Maybe the safety consultant stepped in, maybe as sort of the ambassador between the two to kind of hear both sides and just say, OK, let me connect you, because there's something here for both of you. And that's the win win. Pete Koch: That's interesting. You bring that up. That's very much like you are talking about your communications job before interpreting what people on the inside we’re hearing from people on the outside and then vice versa. So that being able to be that that go between to say, "Okay, so I understand what management's saying. I understand what employees are doing." Let's bring those two together and make sure that we can do the job safely and productively and at a quality level that we can maintain over time. Mike Bourque: And I think you obviously know this as well as anybody. But the truth is, there is a place there where those things overlap. That Venn diagram comes together and it's better for both. And ultimately helping them to realize that is the win for both sides. Pete Koch: Yeah. We talk about this in our leadership, our safety leadership training. Where you talk about safety being first, safety being for safety being first as part of that three-legged stool or part of that triangle. So, safety, quality and productivity are all on that triangle. But when you think about each of those three things, productivity will flex. It will go up, it'll will go down. You'll have lean times. You'll have you'll have fat times. It'll be good. It looks bad. You'll have people, you won't have people. You'll have a lot of stuff to do. You won't have a lot of stuff to do. On those times when productivity gets pushed pretty hard, like that small contractor who now all of a sudden has to make all of his money in the summertime. And in Maine, the summer might only be a few weeks sometimes. Or like right now, it's beautiful and it can extend for quite a while. However, they only have a short period time to do all the work. So, they're trying to get as much work as they possibly can, stuff it all into a short period time. So, productivity for them is pushed pretty hard. If you have safety that's robust, that's part of your culture, that it's incorporated into everything that you do. When I have to push productivity pretty hard and safety is what that upside down triangle now rests on, if you think about safety as the base of the triangle single point, but at the base and then productivity and quality on the other two points but are in the air. If that's robust enough, you can push productivity pretty hard and that triangle won't fall over. But if it's just that little point and you've got to check a couple of boxes in order to make sure you're safe, as soon as you push productivity pretty hard, it's going to fall over and people get hurt and then all of a sudden you can't be productive anymore. Mike Bourque: I think one of the things it does to the people are don't really fully understand or appreciate it, but it creates a it creates a structure around ability to do those other things and to do them well. And sort of whether it's a process and whether it's just it creates sort of the comparison you can make to go from, you know, sort of focus on productivity versus a focus on safety. But if you have sort of this built in culture and it's set for you, it's much easier to be able to do that, as you say. And it sort of stands up. But I think it also is just an easier, easier leap for people. Pete Koch: So, let's talk a little bit more about those MEMIC safety experts and what role they played in the continued success of MEMIC. So MEMIC has grown, we haven't just stayed as a regional or Maine-based insurance company. We're now ensuring all across the nation, really mostly on the East Coast and regionally, but all across the nation. So how has MEMIC's safety experts played into the success of that? Mike Bourque: Yeah, happy to talk about that because it's really at the forefront. You know, by the late 1990s, we were hearing from people in other states who had sort of heard about the success that had occurred. Maine worst in the nation status to this huge improvement. It was being made more insurers wanting to come do business here and started to hear, "Gee, can you come do that for us?" And we actually developed a consulting firm for a time called MEMIC Safety Services. And we would go out and do safety work really across the country. And it didn't take much marketing to get attention in health care and manufacturing and ergonomics and all sorts of places, and logging to be able to find some of that work. Ultimately, we decided we really were an insurance company, too, and we wanted to be able to insure in those other places. And so, again, the lead for us was we were known as the safety company. And so that's how we sold ourselves as we've moved down the East Coast. And, you know, we don't do business just in any state, in part because we want to have a safety person within driving distance of the organization so that they can be on the worksite and be, you know, on the shop floor and help the way they help here. We're not the guaranteed market in those other places. So, we write larger entities that have probably have some interest in safety that they've already established and expressed. And so, they understand that their relationship with their safety and loss control person from MEMIC. It's going to be a big part of the arrangement. And that's what they want. They're looking for that and they don't seem to find it other places. So really, it is the calling card for the company as we've left Maine. And luckily, we found many more of those great people who come out of those industries who are really interested in safety and who are really good at it and develop those same those same relationships that we are able to develop here in Maine. Pete Koch: So it sounds like part of the MEMIC success is having a safety expert, boots on the ground in the field, working with partnering with those different businesses that we're going to insure. And that's really the essential part to be successful as a business. If you take that model that MEMIC has, of you know, having your financial people and your claims people and then your safety people. That safety person can't be in the office, they have to be boots on the ground. They have to be knowledgeable; they have to be a good communicator. They have to be able to understand the business and then to be able to think outside the box because it's not always compliance. Just because this is the rule doesn't mean that this the way it's written is the way that it's going to be applied or if it has to be applied that way, you might need to think outside the box for how you do your job and your task. So if you had a -- and I don't want to put you on the spot Michael so -- putting your creative hat on for a moment here, if you had to give some advice to a business owner that was looking to fortify their safety program or change their safety culture, what would be some advice that you could give them based on your experience here at MEMIC and some of the success that we had that they could use in any business? Mike Bourque: Yeah. Well, the first thing I'd say is make sure MEMIC's your workers compensation insurer - that would be the - because we have experience and we know what we're doing. But I think it would be "Engaged in that relationship with your safety professional." They are your consultant. They are your expert. They are at your disposal and they have a lot they can bring to your organization from their various experiences. They see and they are learning all the time. It's not that they only come with whatever they learn last year. They visit a different place a few times a week. And so that continues to sort of add to their knowledge. Plus, there's people who are out doing education there. They're staying on top of what's happening in their field. So, I think those are really, really important aspects. And I think the other part that we talk about, we've talked about this a little bit earlier, just opening up and listening to your employees because they have something to tell you. And, you know, it may not be that you agree, but it's you have to hear, because more often than not, I found in this job, which is not always about safety, it's about all sorts of other things. But you learn that way. And so, I think it doesn't matter what kind of management job it is, you're going to learn from the people who are sort of on the front lines of your organization. Pete Koch: I think those are great points. And that commun - or the listening the communication part of the partnership goes both ways. Like I have to if I'm a business owner, I have to listen to the people that are doing the work because just because I was really good at doing that job before I owned the business doesn't mean that that person doesn't have a different idea of how to do it better or how to do it safer, or how to actually make it so that we can tie those two things together like we did in logging and make the safe way to do it that much more productive. That's pretty key. And then utilizing your resources and then MEMIC bringing that expertise to the workplace. That's fantastic. Great advice. What does the future hold for the safety experts at MEMIC? Like what's the, where are we going forward from here? Mike Bourque: Well, I mean, you know, we've established ourselves as an organization by selling safety and continuing to grow in that realm. And, you know, while we've been through a time where the frequency of workplace injury is down around the country, there's been more attention to that. It's down by a larger percentage here in Maine where we really got our start and got that ball rolling. So, we're not going to go away from that anytime soon. That's really is who we are, in fact. And I know you know this. But the you know, part of the deal for us, as we have developed in the place where we're not the guaranteed market, which is the rest of the country outside of Maine. Until send out a safety person to do a review of a of a workplace and look at what they're doing for safety and come back with that plan, you know, sort of an action plan for what are we going to work with you on? What will we work together on? Until somebody high up in the organization, preferably the president or the owner of the company, signs that to say, yes, we'll work with you, we won't offer the quote. That tells you how serious we are about it. We don't want to necessarily underwrite your business if you don't want to spend time and work at it with us, because that's where we think we can add the value. That's what makes us different than we think other insurers. So, you know, the continuing development along that spectrum of workplace safety and those people, I think we are going to always rely on the human side of this. I mean, I think there are all sorts of resources that are available electronically. I think those are just tools that go alongside the safety professional who humanizes it and also can look with their eyes and see what's happening, you know, in a place. So, I think we'll continue to have more capacity as a result of those tools. But it really is about the people who know what they're talking about and can help relate to the people, because in the field, that's how we'll continue to grow. Pete Koch: That's great. So that essential safety is about relationship. It's about the people both doing the work, seeing the work, committing to improving what's happening. And then at the end of the day, that commitment to making sure all your people go home in that same condition as they came in, maybe a little bit more tired than they did when they came in. But all their fingers and toes, safe, happy home so that they can work another day for you. And that's the bottom line. Mike Bourque: And I think, you know, most every employer wants that. And I think that's the truth of the matter. So, we start at good place, I think. I think human nature is that we want to have people, you know, be whole and be productive outside of their work time. And that makes those relationships better. And at this day and age, especially in the northeast and down the east coast, where you have really low unemployment numbers. You've got to take good care of those people that you have invested in that you've brought in and you spent money to hire them, to put them in place, perhaps to train them, to provide them with equipment. The last thing you want is to see one of them go out with an injury. And because it's not only an injury to them, obviously it could be life lasting, but it's an expense to your organization. And you may not find that same person out there somewhere, a free agent who you can bring in and hire. You need those people. Pete Koch: Yeah, you definitely need those people and they're hard to find. People are hard to find. They're that essential human resource. But they're becoming scarce these days, which, you know, that's not a bad thing to have sometimes when your economy's going that fast that you need that many people. But it also becomes more difficult to keep those people around. So, safety, again, be another essential part of those three things. Right. Safety, quality and productivity all the time. Mike Bourque: Absolutely. Pete Koch: Fantastic, Mike. I think that about wraps up this week's Safety Experts podcast. And I wanted to thank you very much, Mike, for spending time with us today and sharing your story and your experiences and just being here for us and supporting the continued mission of MEMIC overall. Mike Bourque: Well, it's my favorite topic, of course. And MEMIC and our work in safety. So, it was fun to do. And I think this is going to be a successful endeavor. I look forward, like I said, to listening to future podcasts because I think you going to have a big audience. Pete Koch: Thank you very much for that. Any last words or tips that you have for our listening audience out there? Mike Bourque: No, I think I think we've touched on all of it. I think we did. Pete Koch: Yeah, that's fantastic. So, thanks again, Michael, for joining us today. And this is Peter Koch for the Safety Experts podcast. If you have any questions for our guests or would like to hear more about a certain topic or from a certain person on our podcast. Send us an email at [email protected]. This podcast was presented by MEMIC, a leader in the competitive insurance market and a company committed to safety. We are that safety company that sells insurance that we were talking about before. And to learn more about how MEMIC can help your business, visit MEMIC.com. Don't forget about our upcoming workshops and webinars. And for those dates, you can also find those on MEMIC.com. We appreciate your listening and encourage you to share this podcast with your friends and co-workers. Let them know that they can find it on their favorite podcast player by searching for Safety Experts. And last. Thanks for tuning in to the Safety Experts podcast. And remember, you can always learn more by subscribing to the podcast at MEMIC.com/podcast. Resources/People/Articles Mentioned in Podcast MEMIC - https://www.memic.com/ Peter Koch -https://www.memic.com/workplace-safety/safety-consultants/peter-koch Michael Bourque - https://www.memic.com/about-memic/leadership-team/michael-bourque John McKernan - https://www.uschamber.com/john-r-mckernan-jr Wall Street Journal Article – https://www.wsj.com/ MEMIC’s Overview & History - https://www.memic.com/about-memic/company-overview MEMIC’s Mission - https://www.memic.com/about-memic/the-mission Rod Stanley - https://www.memic.com/workplace-safety/safety-consultants/rod-stanley Andy Wood - https://www.memic.com/workplace-safety/safety-consultants/andy-wood Maine State Flag - https://statesymbolsusa.org/symbol-official-item/maine/state-flag/flag-maine Certified Logging Professional - http://www.clploggers.com/clp2.html Game of Logging - http://www.gameoflogging.com/