Getting Under the Surface of Slip and Fall Injuries with Patrick Dooley
MEMIC Safety Experts - Podcast készítő Peter Koch - Hétfők
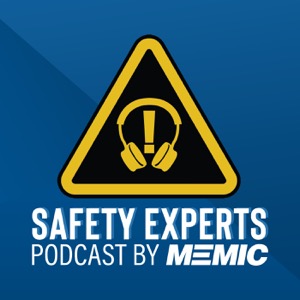
Kategóriák:
In 2019 the Bureau of Labor Statistics reported there were 190,000 slip and fall events that resulted in time away from work. 60% of those were falls on the same surface. Any surface is the interface with our shoes and together they provide stability for our base of support while moving. The surface composition and condition are key to the efficiency of our movements. A stable surface compatible with the work being done is a good place to start when trying to prevent Slip and Fall events. On this episode of the MEMIC Safety Experts Podcast, I speak with Patrick Dooley, CSP and Senior Environmental Health and Safety Specialist for LL Bean. We are going to get under the surface of slip and fall injuries and discuss how understanding your surfaces can help reduce slip and fall events. Peter Koch: [00:00:04] Hello, listeners, and welcome to the MEMIC Safety Experts podcast, I'm your host, Peter Koch. I expect many of you listening out there have had the chance to walk on the beach. Well right now I want you to think back. What was it like? Was it Rocky where the rocks big or the little pebbles? Was the sand hard or was it really loose the surface move underneath your feet when you walked when we expected a surface like soft beach sand or the gravel around where the surf breaks can be just what we want. But when that surface changes to something we aren't expecting, it can cause us to stumble or at the very least break stride. Think about it. So when our foot or shoe interacts unexpectedly with the surface, our base of support changes as our foot, knee or hip moves farther to the side or four and a half feet. So when we're walking or working, most of the time our base of support is our feet. So right now, if you can [00:01:00] safely do it, stop and put your feet about shoulder width or maybe just a little wider and then steady yourself and keeping both feet on the ground, shift your weight from one side to the other side and then back again should feel pretty stable, balanced. Even if you shift your weight pretty far to one side, you're still going to feel pretty balanced as long as your feet are going to be on the floor. Peter Koch: [00:01:23] When you move side to side, I want you to think about how far your center of gravity and that's right around where your belly button or your belt buckle is, how far that moves from side to side before you might feel like you're going to tip over. So depending on how far apart your feet are, your center of gravity can move quite a bit from that center position. You can move it almost all the way to the outside of that foot, to the side that you're standing on now. And again, only if you can safely do it, move your feet closer together with your toes or your shoes touching or maybe almost touching. Now shift your weight from side [00:02:00] to side again. And do you feel the difference? You should even see the difference in how far your center of gravity moves before you feel unstable, because the closer your feet are, the smaller that base of support is. We fall when our center of gravity moves outside of our base of support. The larger or faster the movement and the smaller our base of support is, the more likely we are to fall. It's just physics. You really can't get around it. And we take for granted the surfaces that we walk on during the day. That's really neither good nor bad. It just is like you're going to walk across the tile floor in the bathroom or you're going to walk across the rug in your home, or you're going to walk across the concrete at work and you take it for granted. Peter Koch: [00:02:45] However, the surface is an important piece. It's the interface with our shoes. And together that surface in our shoes provide a platform of stability for our base of support while we walk, move, lift, reach, roll or whatever [00:03:00] motion or ambulation that we're engaged in at the time. That surfaces composition and condition are key to the efficiency of our movement. So it's reasonable to think that a stable surface compatible with the work being done is a good place to start when you're trying to prevent slip and fall events. But how do you know what that surface is? How do you know how stable it is? How do you know how slip resistant it is? And unless you're fortunate enough to have built a custom facility, most of us have inherited the surface that came with the building. And even if you did build a new facility, some of the walking working surfaces may have been specked out by the architect and not the safety engineer. They may look good, but they're not compatible with the work, meaning that they don't have enough inherent friction to keep you from slipping or too much and may cause you to stumble. This is where a thorough surface or floor care and maintenance program really comes into play. So understanding all the components that go into [00:04:00] keeping us upright when we're walking and working around the business. Peter Koch: [00:04:04] And there's a lot that goes into one of those programs. And I don't know if you're like me. When I first started out, I was thinking, I don't need one of those. Our floors are just fine. And then if you look back at some of your statistics, it might show a different story. And if you look at it nationally and the Bureau of Labor Statistics has some stats that should make you look down at the floor a little more closely, because in 2019, BLS reported that there were more than 190,000 slip trip fall events that involve days away from work, and 60 percent of those were events that were a fall to the same level. So not a fall from a height, like a ladder or a vehicle, but a slip and fall on the same surface. So gaining insights to where to start and the pitfalls that you might look out for are key no matter what you're doing, if you're just starting out to create your own slip and fall program or if you're really evaluating an existing program [00:05:00] for your company. So that said on the podcast. With me today is Patrick Dooley, CSP, and senior environmental health and safety specialist with L.L. Bean. And we're going to get under the surface of slip and fall events and what steps L.L. Bean has taken to manage the surfaces its staff work on at their facilities. So, Patrick, welcome to the podcast today. Patrick Dooley: [00:05:21] Well, thank you very much, Peter. Happy to join. Peter Koch: [00:05:24] That's great. And, you know, you and I and a couple of others from MEMIC, we ended up doing a podcast, not a podcast, but a webinar a few weeks back on Slip and Falls and talking a little bit about Libyan's experience managing slip and falls at their store. So I wanted to have you on and just maybe take a little deeper dive into some of the things that you did, what you learned from your experiences, some of the challenges that you ran into and what maybe some actions that you took. So I'm hoping that we can get into some of those conversations today as we move forward. Patrick Dooley: [00:05:58] Absolutely. Peter Koch: [00:06:00] Before [00:06:00] we jump into the bean’s plan or process, tell us a little bit about your background. So what got you started in safety and how long have you been in the field? And maybe how long have you been at L.L. Bean? Patrick Dooley: [00:06:12] Well, thank you. So as of right now, I am lucky enough to be in the field of safety for the last 20 years, have a degree in safety studies from Keene State College. And I've been lucky enough to be with L.L. Bean the last 14 years. Peter Koch: [00:06:29] That's pretty awesome. And Keene State's got a pretty long history of having of putting out quite a few really good safety professionals with their safety studies programs out there. So were you able to jump right from Keene State to beans, or did you have a couple of places that you stopped in between? Patrick Dooley: [00:06:49] So in between the year 2001 and leading up to L.L. Bean, I was able to hold a couple of different positions within safety included lead in asbestos abatement [00:07:00] and consulting, as well as working for a temporary agency and doing safety for all of their temp hires and working with actually MEMIC to help with our lost control. And then I was fortunate enough to land a job with L.L. Bean, and I've been there ever since. And the best part about L.L. Bean is that it's not singularly focused into just the retail division. We have a manufacturing division, we have our fulfillment centers, we have our facilities. So it's a lot more expansive than what people might think of LLB. Peter Koch: [00:07:37] Yeah, it's not just a store. And, you know, we were talking before the podcast. Neither you nor I are native to Maine. We're actually both native to Connecticut and then moved to Maine for our wives, which is kind of cool. And, you know, I had known of L.L. Bean while I was there in Connecticut and had come to Maine and actually shopped at the flagship store. But I had no [00:08:00] idea the extensive facilities that L.L. Bean has between, you know, research and design and manufacturing and then shipping storage besides the retail facilities. So that's pretty, interesting. You get but you get to see a lot of interesting things just within the L.L. Bean ecosystem. Patrick Dooley: [00:08:21] So the L.L. Bean as a whole, when you look at it with all the different divisions that we have from a safety perspective, you're able to apply all the knowledge you've learned over the years and gain knowledge as you go along. It kind of opens the doors for a lot of folks. It's eye opening. Most folks in our profession get kind of siloed into manufacturing or transportation or construction. And, you know, here at the L.L. Bean, we've been afforded the opportunity as safety professionals to explore all of those avenues. And it's been great. Peter Koch: [00:08:58] You even have I mean, even [00:09:00] at the retail store, you even have hospitality. So you have there's a little food outlet there, a restaurant that you have at the flagship store. People wouldn't think of that either. So when you explore L.L. Bean from a safety perspective, it's like almost working in a little city because you have all these different nooks and crannies that have different needs. And then you have the connection with the public. So it's not just workplace safety, as you might have in manufacturing or you might have in an office building or someplace else. But you have a pretty strong connection with the public that you're going to have guests and staff encountering different exposures together. Even so, you're planning on both sides, which from my perspective, I always think that there is a definite overlap between what you might do for guest safety and what you're going to do for workplace safety. There's a definite overlap there. Patrick Dooley: [00:09:56] And I would even extend it even further to guests, to [00:10:00] the community, because majority of the. Places where we reside throughout the country right now. We expand our offerings into the community from our outdoors discovery programs, so things are available to folks and it's not just the branding thing, but we want people to be outside and be in the outdoors. They're not just our guests, we are actually the guests to the outdoors. Right. I mean, that's the whole point. But how we do it and how we make people be safe and do things is I mean, that's what we've been very successful in, even through this whole pandemic. Peter Koch: [00:10:33] So that's pretty cool. And not just all of the different facilities that you have, that do different things. But you have locations across the country as well, which is something that didn't exist back in the 70s. Right. It's you've expanded across the United States. So you have 54 locations or something like that across the United States. Patrick Dooley: [00:10:56] Now we're across 19 different states [00:11:00] and there is roughly 54 locations with soon to be a couple more opening this year. But within this past year, those 54 locations in 19 states offered up many different challenges throughout the pandemic, as anyone could imagine. Peter Koch: [00:11:18] So I'm sure they have. And in all those different states, there are you know, there's different like you said before, there's different cultures that you have to work through and within there's different facilities, challenges. There's different perceptions from the public that you might have to manage as you go through there. All of these things kind of fit into that overall safety puzzle. And I would imagine, like one of the common things that you have for exposures across all of the different facilities and no matter what they do is slip and falls or slip and falls. So slip and fall exposures, how different are they across the different facilities and how different are they maybe [00:12:00] in different states or maybe in the different areas that you would have work going on, whether it be a public facing or outdoor center or manufacturing and warehousing? Patrick Dooley: [00:12:13] Yeah, I mean, if you look at it from a retail standpoint, I'll start with that is we are in those 19 different states. So what is the environment that we're in? You know, where we're not in sunny Florida where we may get a little bit of rain. We're in Park City, Utah. We're going to go for the big end of town that's known people their ski and we're in the Adirondacks and in New York. Same thing. Hopefully it's snow season and the rain events and everything else that comes along with New England. So a lot of the things that go into planning and engineering and thinking about how we build out our stores, slips trips and falls have to be kind of in the forefront, not just from our customers, not for our employees. It's things [00:13:00] that we need to think about. And those are things that maybe when we're building out these stores 10 years ago, we didn't have so much forward thinking. But now as we're, you know, 10 years later, we're trying to figure it out and say, oh, you know, we need to look at more of what's the impact to not only the customer or the employee, but sustainability to floor care and maintenance programs. What does that all look like? Peter Koch: [00:13:30] Yeah, it's all one big puzzle, really. And if you just, I remember in some of my past experiences or other working with clients at MEMIC or working outside of MEMIC before I came to MEMIC thinking about the flooring or the surfaces that you're going to have people walking and working around. It sometimes started with the idea of what's it going to look like? And we never really talked about how are we going to maintain it, what [00:14:00] type of footwear is going to be on it, how much traction is going to be there? Basically, they figured, well, we're going to put it in and then if we have to replace it, we’ll replace it in 10 years. But frankly and historically, those products, especially in those high traffic areas, never lasted the time that they expected to because of either increased traffic levels or, you know, I can tell you, you talked about Park City, Utah. I was the question that rolled through my head, when you're saying that was I wonder if you got anybody in ski boots walking through one of those stores. And I think from a slip trip and fall standpoint, ski boot on any surface is one of the most difficult things to try to figure out, because there isn't really anything that's going to be great, because you can find something that works for the ski boot, but then it's near impossible to keep it clean. Patrick Dooley: [00:14:52] For sure and one of the things that architecturally what was looked at when stores are being built, not just L.L. Bean, but other places [00:15:00] is. Does it look how does it feel? Is it on Brand in what ended up happening from. And from our standpoint is we were having like four or five different floor textures within one building. So now your floor care and maintenance program becomes a little bit crazy and the costs are a little bit different because you're vacuuming one space, you're mopping in another and you're dry mopping in another. So it just adds to a lot of the confusion. And like you said, it's, you know, depending on the area your in, that may not be the way to go. So 2021, let's revisit that and see how we can make improvements on that. Not only impacts our employees, but the general public that comes in to visit L.L. Bean. Peter Koch: [00:15:46] Sure. So we're going to talk about the refurbishment program that you guys went through and specifically about some of the flooring. But I think it's worthwhile talking a little bit about some of the challenges with slip and fall prevention and [00:16:00] kind of how they affect the big picture. I think some of the big ones are in and you alluded to this in our webinar, perception is one of those things. Visibility is another. And then surface traction. I think those three are pretty sizable. And we can address some of those as we go. So let's really start with surface traction and what it is. And why is low traction a problem? Patrick Dooley: [00:16:26] I think it is an easy question to answer. But at the same token, it isn't because it's one of these things that people don't see. Right. It's invisible. So problems with these surfaces cause what the majority of the slip trips and falls for the most part, if we see a puddle on the floor or something that looks slick or, you know, gum or leaves or whatever, we can kind of focus on that. Right. But if we're not wearing proper footwear, you're not going to get the right amount of traction. [00:17:00] And the amount of traction depends on what kind of flooring you have. So if you go see not only attraction's really invisible, but it also isn't immediately obvious how to quantify and tell when to do something about it. So how much water makes it so slippery or, you know, is it the snow and ice on the sidewalk? It's slippery or, you know, is it snow melt or calcium chloride that we're putting outside and tracking? And that makes it slippery. So there's so many different environmental factors that can come in that can give you this low traction effect. But then there's this underlying thing of what's our perception of slippery? Your perception is going to be different than mine. You know, a perception of someone at a younger age, a toddler. Their perception is that we're going to be way different than someone who is probably a little bit older. So where [00:18:00] they may walk fast, someone may walk slower. So perception is kind of this undefined thing when it comes to slips trips and falls and how to figure out what it's not slippery and what is slippery. Peter Koch: [00:18:12] And I think that's a really good point. And it's perception is one of those things that you really it's hard to control outside of yourself. Like one of the first things that people do to help prevent slip and fall injuries are to put signs up. We're going to put a sign up and help make people aware. You've all seen the yellow wet floor signs or maintenance in progress or something sign. And they're fairly ubiquitous. I can't tell you. Well, before all the travel restrictions happens, you know, you walk through the airport and guaranteed if you're walking through early in the morning, you're going to see a number of those along the walkways. And after a while, you don't even see him anymore. So, like, they're not even they don't even create additional perception. [00:19:00] You just see them as part of the background. You might not even process it. So that's one of the challenges with perception. But the other challenge, too, is like it's all it's different. You said what might be slippery to you or hazardous to you and your perception is going to be different for me, my perception of what the hazard is and then it changes what you do with it for sure. Patrick Dooley: [00:19:20] Right? I mean, we all have unique gates. Our strides are all different. Our footwear choices are all different. Now, the type of shoe that you wear that we have an on our footwear all adds into what can be slippery and what isn't slippery because you and I could be wearing the same shoe. But your shoe could be six months older than mine. But I'm sticking to the floor and know you're falling on your behind. It's very different. Peter Koch: [00:19:47] So and if I'm taken if I'm taking a six or eight inch longer stride than you are in our legs or the same length. So there's a different amount of force placed on the heel and the sole to generate [00:20:00] friction when it lands. So. It's a there's so many different things that go into that to drive perception, and they're all a lot of them are habits. I mean, we're many of us don't put on shoes in the morning in order to prevent a slip and fall unless, of course, you're going out into a hazardous environment. And then you might put, you know, ice cleats on or micro spikes or something. That is going to be a traction enhancer for a pair of shoes that you're going to have. But typically, when you get up in the morning, go to work, you put on the shoes that either match the outfit or they're going to be comfortable for what you're going to do or required for what you're going to do that day. Patrick Dooley: [00:20:40] Right. And I think that from an employee standpoint, because you're in the same workspace day in and day out, you recognize those areas that can be slippery or not slippery. And so you can adjust the footwear that you're going to wear or you're recommended the footwear. So [00:21:00] if I'm a line cook in a restaurant, I know that it's going to be slippery back there. So I'm going to wear footwear that translates to that environment, similar to the fact that if I'm outside shoveling in the middle of winter in ice and snow, I'm going to wear footwear to that effect. But if I'm shopping inside of a store, for the most part, it's fair game. You don't know what people are going to wear and come in and come out from. So from a general liability standpoint, we can't anticipate what their perception is going to be of a floor and whatnot. We can coach our employees. We can do certain things to lower the risk, but the general public is open to us so they can come in and they're at the risk of the environment that they're in. Right. Peter Koch: [00:21:46] Flip flops to steel toes, really, I'm sure you've seen it all come through the door. Patrick Dooley: [00:21:52] Absolutely. Peter Koch: [00:21:53] So perception exacerbates the problem of low friction. If you have a flooring or a surface, whether [00:22:00] it be inside or outside, that could be generally slippery. But your perception and how you see that surface can change how you interact with it. What other factors play into reducing the traction on a floor. Patrick Dooley: [00:22:17] So let's think about the kind of the five biggest things that you see for a slip trip and fall events. Right. It's slip resistance on walking surfaces. So we've talked a little bit about that. The walking surface conditions, visibility is another one poor condition of either handrails or guardrails that are in the area. And the accessibility can be a major factor, too. So is it too crowded? There's too many things going on for us to be like fixtures? Let's think about having fixtures in aisles and you're offering up an area where people are aware of their surroundings and can slip trip or fall or something. So [00:23:00] I think those are probably the five biggest things that we would look at in order to kind of reduce the risk of a slip trip fall. Peter Koch: [00:23:09] And when we start to look at those different factors, a lot of it's going to come down to what the flooring is at its base. Like what material, what's the composition of that particular floor that you're on? And then what? What are you going to do with it? And that's the fixtures. That's the maintenance. That's the way it's going to be used. The number of people that are going to be on it. All of those things contribute to it. But there's a base slip, resistance or traction that flooring is going to have when it comes from the manufacturer. So if we start there, because again, let's start at the base and let's really get down to the nitty gritty of this whole thing. How do you know how slippery a floor actually is even before [00:24:00] you start putting things on top of it and people on top of it? Patrick Dooley: [00:24:03] Right. So fortunately, we're lucky enough, right. There's there is some sort of scientific method that we can apply to looking at the coefficient of friction, which is objective. Now, the standards on coefficient of friction are all over the place for flooring, but there is a threshold that people can use or benchmark against that says that is your floor more slippery or less slippery. So OSHA doesn't define it. The National Flooring Institute, they have their own standard, but you can benchmark it. So when you're buying something off the shelf from, let's say, Home Depot and you're buying tile and you're putting in your bathroom, there is a COF coefficient of friction label on it that says this meets blah blah blah. From our standpoint, we would bring in someone like MEMIC to sample the floor. So we do try Bomaderry. Right. So basically it is science of measuring friction. So we're going to use [00:25:00] a device. And in this particular one, we're using a binary tribometer or output tribometer that measures the coefficient of friction, the floor sideways, frontwards, backwards, wet, dry. And he gives us an idea of where we're at and what risk measures do we need to take to lower the risk of a slip and fall inside the workplace? Or is the flooring in to match the environment we're putting it in? So obviously, if we're putting flooring in Freeport, Maine may be different than what we put in Virginia. Virginia is not going to have snow and they're going to have snow melt. They're not going to have, I should say, that could knock on wood after this year. Anything can happen. But, you know, generally speaking, they're floor conditions. They look different than what we're going to have in Freeport. So let's define that and let's come to a conclusion of what's happening to the environment, basically is what it is. Peter Koch: [00:25:56] Yeah. So how do you understand first understanding of the environment [00:26:00] and then getting some information about the floor and how those two things would match up and compare to each other? Because certainly, you know, like you talked about like in a food service standpoint, a hard, hard core tile with a real polished surface isn't going to be great if you're going to get grease on it from your fryolator. Not a great combination. And that same combination wouldn't be great to have, say, in Freeport, where you're going to have outside, where you're going to have snow and sand because it's going to wear really poorly and wet shoes. Wet slick shoes on that surface is going to be crazy slippery. Patrick Dooley: [00:26:43] Absolutely. And also, what is the location? What do you where you're at? So it's easy for us because it's our campus. It's our store. But outside of Freeport, you know, we're leasing spaces inside of malls. And, you know, we may be just a pass through. [00:27:00] Into the mall. So, you know that the parking is convenient. So people are walking in and out. So what happens is that they're dragging stuff in and out of the store. So we need now what we didn't know then is to match the flooring to the traffic that's going to happen inside of the store, Peter Koch: [00:27:19] Traffic patterns and volume are especially for your situation it was pretty critical as you started to look at what do we use when we start when we get into that refurbishment project? I also think that that's a pretty important thing to think about, no matter where you are. I mean, traffic patterns, whether you're in a doctor's office, hospitality situation, manufacturing, I don't think it really matters. Even a grocery store traffic patterns are a big deal because depending on where they're coming from, like you said, you think about a grocery store, if you're coming from the butcher area or you're coming from the back of the house space where we're [00:28:00] storing things or you're coming from front of the house as people are walking in through the entryway, how much what's the possibility of having a contaminant on the bottom of your shoe that you're dragging in? And how do you treat for that? How do you plan for that? How do you manage that? And there's some definitely some strategies there. Sure. Patrick Dooley: [00:28:19] Right. And then the interrogation of the surface. So obviously the middle of your walkways inside of a store or a building or what have you are going to have less traffic than your main entrances. So do you have a specific plan for now resurfacing those? Peter Koch: [00:28:37] So I guess this is a good time to sort of jump into the refurbishment project as you started to look at your facilities. It was time to replace some flooring and to refurbish some of those facilities that needed to have needed it. So when you started to do that, I know we had talked about before that you had used tribometry to learn [00:29:00] what the coefficient of friction was about some of those surfaces. Talk to me a little bit about the refurbishment project that you did and then what part sampling the surfaces, either before or after played to you making decisions about flooring. Patrick Dooley: [00:29:16] So when we kicked this off, let's say, three years ago, the question came up from our store operations, the facilities, teams that we hate. We're thinking about getting rid of all this different floor textures and going with a singular floor texture inside of our stores. What impact would that have on not only the general public, but on our employees? And that posed a great question for us. How do we gauge that? How do we figure that out? Luckily enough for us, at the time we had this great big expansive space that was getting ready to be refurbished that allowed us to take some concrete and [00:30:00] create sample areas. So the goal was to come up with a concrete surface for the store the goal on top of that was to have our floor care and maintenance program. The cost reduce it would look clean it would be singular. But in order to get to that point, how do we know it's not just safe? Because I don't think safe's a good word to use. But I mean, is it slippery? Does it work? Can we drag fixtures across of it? Does it need to be mopped? Do we need to use a machine so we are able to create this space and use four different textures? And we partner with MEMIC and said, hey, bring your tribometer here, to L.L. Bean, let's do some testing. We're going to wear it on the floor. We're going to make it where we're going to make it dirty. Patrick Dooley: [00:30:53] So that way it's not like you're getting a fresh floor when you come in and it gives us a little bit of wear patterns and such. Take the readings and then [00:31:00] from the readings, we will determine what would be the best option to replace in the flooring that we currently have in our stores. And with that, we came to the conclusion, let's use a flooring that has some texture in it, has a urethane finish. It'll look nice. It’ll look uniform and has a high coefficient of friction. Little did we know that the environment dictated kind of what would happen in the future for one of our stores. But for the most part, it was the right decision. And if you look at major retailers right now, you look at your Wal-Mart, you look at your Hannaford's, you look at Shaws, and they're all going to this rough surfaced concrete slab. And really, it's because your floor care and maintenance programs are really less than what they would have to be if you had tile. The agent deterioration factors kind of go down. You don't have to have as much floor care repairs than you have now. And aesthetically, it actually looks good, removed four textures from the floor. [00:32:00] You know, for us, you go from a wood floor to a carpet to a court floor to a carpet in our demographics for our customers. Unfortunately, that created more of a hazard than anything else. Peter Koch: [00:32:16] Let's take a quick break. Safe for S.A.F.E is an acronym for many different things. But when talking about slip and fall events, Safe represents the four areas that you can focus on at your facility to prevent slips and falls, surface awareness, footwear and environment. Look at the surface as it relates to its composition, condition, changes and contamination. Evaluate how your facility layout and pace of work may affect the awareness of your staff to slip and trip hazards. What is your footwear policy and how is that compatible with the type of work and the surfaces at your facility? And last, how [00:33:00] does the lighting and weather in and around the work environment compound or create slip and trip hazards? If you're interested in learning more about how to prevent slip and fall events at your workplace, check out the resources at www.MEMIC.com/workplace safety. Or if you're a policy holder with MEMIC, you can sign into the MEMIC safety director and find more resources there. Now let's get back to today's episode. Yeah, that kind of ticks into that whole perception and visibility, too, like if I'm on one type of surface and it has a lot of traction to it and I'm not really understanding what the next surface is going to bring, I might know that it's not there or it's going to be different, like going from carpet to cork because it's fairly easy to see that difference. But you have no idea how it's going to react under foot. So they might continue their gait the same way and [00:34:00] their feet might still be wet from tracking in from the outside. And all of a sudden it's a slightly different coefficient of friction and down they go at end. Lighting must play some difference in that to being able to see changes in elevation, changes in surface texture that might cause someone with a low gait, more of a shuffling gait to maybe even trip on some of those higher traction surfaces or maybe uneven like cobbled surfaces. Patrick Dooley: [00:34:28] So the majority of our refreshes, not only do we look at the flooring, but all the lighting was changed and all of our fixtures were changed. So we eliminated not only a lot of heavy fixtures, but also our stores were a lot more adequately lit than they were in the past. I can't tell you what the foot candles were, but I can tell you that it made the product look a lot better. Peter Koch: [00:34:57] It's kind of amazing how something small like that, you know, [00:35:00] you might even change something for a product, get the product to look better, increase the lighting so you can see better. But visibility makes a huge difference and slips and falls. When you can see the surface. It helps you with your perception. It helps you with understanding the exposure, especially in those crowded areas. Some of the things that we talk to our clients about, too, is as you go through your facility, some of the areas that you should pay a lot of attention to are those low-lit areas where your employees are going to be like your trash handling spaces, the back of the house spaces that typically aren't as well-lit as some of the front of the house spaces. Those are always areas. If you go back and look at what your trends are or your injury or your near miss trends, you're going to find that they're going to happen in those spaces just because you can't really see what's on the floor. Patrick Dooley: [00:35:51] And those are the areas that we tend to lose focus on, right? They're not selling areas for us. So Backhouse is a good [00:36:00] example. Your employee entrance. No employees enter from the front door, right? It's always the back door. The back door has one little light, usually on top of it. You know, lighting is a is a big factor in what we do. Peter Koch: [00:36:12] Yeah, yeah. And you have some complex needs because you are you're not only trying to develop flooring that's going to help you reduce the overall maintenance and replacement costs. But it had to look good. It had to match, I guess, the branding, you could say, for L.L. Bean and had had to draw people into the space and make them feel comfortable. And it needed to be functional not only for traffic walking, but also for moving your fixtures over the floor, too. And I think it's something that we forget. And when you're talking about moving a fixture, what do you, I think I understand what you're talking about. You're moving racks and carts and things across the floor. What else would be considered a fixture [00:37:00] that you might have to plan for Patrick Dooley: [00:37:02] Going from back of the house to the front of house or using dollies are used in pallet jacks or, you know, you're moving over stuff, Xerox, anything that would be product movement. And not just that. There's stuff that we sell that, you know, you have one person that needs that kind of move it along in a customer needs to pick it up or do it. So how can we make it easier for them? One is it is the flooring work for them? Is it going to damage the product as they’re dragging it across? Is it going to damage the texture as they're dragging it across? So is it going to be agent deterioration factor on that? So I think there's a lot of different things to think about. And you could probably go way down a rabbit hole on that. But, you know, in general, what's going to work best for that environment and how do you how do you figure it out? And I think we've only done a really good spot, because if I look at my employee injuries that have occurred over the last ten years, you [00:38:00] know, there was a significant push pull was a big one. Patrick Dooley: [00:38:05] You know, they're moving fixtures around. We did floor set changes monthly, which is crazy, right? I mean, did you force that change? It's massive. So now we've gone to quarterly and that has made a significant difference in how we handle product, how we move product, you know, tag product change, all of it. It just has a little trickledown effect. Our store injuries have. Gone from pretty significant to pretty insignificant over the last. So if we look at I did 13 years, my 14 years over the last three, we've seen a dramatic dip in retail store injuries. And a lot of it has come from our process changes our front of house changes, flooring, fixtures, lighting mannequins, handling mannequins, you know, bringing them upstairs, downstairs, dragging them across floors, [00:39:00] all that stuff. So it's had a huge impact. So people think I'm making a floor change or I'm making a fixture change. It may seem very insignificant, but if you look in the long, broader lens to it, it really does have a huge impact. It has a huge impact on how people play with the landscape of what their store looks like or what their environment is. Peter Koch: [00:39:23] And those changes prevent exposures. But it also allows you to do more like when you when you have good flooring, good lighting, good changes, good processes in place. It allows you from a retail perspective to have your associates interacting with your guests, which is going to be a huge part of the experience when they come to L.L. Bean or they come to any retail establishment like you don't want your staff always focused on how am I moving all this stuff around and what's going to happen if it's a complex process or a big deal. You want them interacting and then when they're not interacting, then they can start to move different things. It's just part [00:40:00] of that. So some of these changes can, like you said, have far, far reaching effects. But there is a lot that goes into it. Did you have a team of people that worked together to make these floor changes or decide on the floor changes? Or was it kind of just you and your notebook? Patrick Dooley: [00:40:18] No, absolutely no. We had we had to definitely have a team. So in the past, it was more of a facility planning and operations lens on what the store is going to look like and how we're going to interact. And aesthetically, was the approach right. Let's make the store beautiful and have that environment. When you walk in, you're like, oh, wow, this is L.L. Bean. Now, 20 years later, like no we want it to be shoppable. We want it to be yes, we do want it to look nice, but we want our customers to interact. We want our employees to be able to interact. We want to do in a safe manner. And, you know, is it functional? Is it flooring? [00:41:00] Does the fixtures, is it all meet what we're trying to do here and is it on Brand? And I think we have achieved that. And I will say, you know, we're having a store opening here in May and it's probably going to be one of the probably one of the nicest stores that I've seen. And it's going to have all these different components that we're talking about today wrapped up into it, which is going to be great to see. Peter Koch: [00:41:23] Yeah, that's really cool to kind of see it all happen in one particular space and then start from scratch and see how they kind of move going forward. That's pretty cool. So when you when you were making these changes going through and I know it's a process of understanding, installing, observing, making some more changes. Was there anything unexpected that you found when you were when you were testing flooring or after you installed some flooring that you hadn't expected? Patrick Dooley: [00:41:59] Yeah, [00:42:00] I think, you know, there are unknowns. I mean, you try to do as best you can to replicate situations and environments when you do sample areas inside of what we tried to do. But then when you get it into the actual environment, they're going to be putting it in. There are certain unknowns. They're going to happen. There's obviously external environmental factors that are out of control. A good example is, you know, one of our stores in upstate New York, they're using a different type of snowmelt. So we typically use salt and sand mixtures. They were using a calcium chloride based product that was being trapped in through the store. And this store was a pass through into a mall. So, you know, a lot of our traffic isn't even shopping. They're going into the mall. They're dragging the calcium chloride in. So the further and further they're bringing it in to more slip trips and falls that we were having from not only customers, but from employees. Because now remember, back to the perception thing, employees [00:43:00] already knew where the hot spots were. Right. But as these as this calcium chloride is being tracked to the store, those hotspots changed. And so this particular store, which usually only has a handful of slips trips and falls a year, we had upwards of 50 within two months. And it was something that we didn't plan for. Now, we had the same flooring in some in two other stores earlier in the year, but. You know, winter came and we found out that maybe this flooring wasn't the best, so we had to go back and kind of think about, all right, why is this happening? Do we know what some of the root causes are of it? And what do we do to kind of fix it? And luckily for us, within a short time frame, we're able to come to a lot of big conclusions and pivot to, [00:44:00] you know, getting a new floor care and maintenance program in place because we knew that the machine that was there wasn't working properly. Patrick Dooley: [00:44:07] We knew that the landlord was using a different product on the sidewalks that was being tracked into the store. So, you know, we worked with the landlord to change that product. So that way the calcium chloride was, you know, the problem with calcium chloride that sticks to these surfaces. And it's a it's a real pain to clean. And actually, it broke the machine that was supposed to clean the floor. So we asked the landlord to go to a different product for the store. We also found our floor mats are terrible in this particular store. So a water hog mat, which is something that we sell, is wonderful from a household standpoint. But from a commercial standpoint, maybe not the best product to use in a store that has a very large traffic volume. So we changed out our floor mats. This particular store, you would walk in and you would see the yellow floor. What signs up and down the aisles. [00:45:00] Now you walk in the store and you don't see them anymore because we did make those changes. Patrick Dooley: [00:45:04] The floor care maintenance program is way more robust. The matting program is now included in that floor maintenance program, which it wasn't in the past. The changes were made to the salting and sanding and calcium chloride outside the stratification inside of the vestibule was turned up. So that way and you're getting it was drying as you're walking in instead of staying white all the time. So those are things that you don't really necessarily think about when you're sitting inside of a box sampling flooring. Right. You have all these wonderful ideas of what you want that's going to be and how you're going to work with it. But then, you know, you don't know what someone's bringing in. You don't know if, you know, that site had recently been paved. So if it had been recently paved and it's wet, you're dragging all those oils into the store, which would cause a similar effect to what calcium chloride had done. So while it may be temporary, you're still going to scratch your head and figure out why am I having all these trips [00:46:00] and falls? So there's a lot of unknowns that happen with this. You can only focus on the things that you can focus on when you're trying to make a decision like this. But, you know, I think is always going to be that little level of uncertainty that you have to have. And that's the risk that you need to be either willing to accept or not accept. Peter Koch: [00:46:25] Yeah, I don't think there's any perfect solution for slips, trips and falls, except, you know, maybe carting people everywhere they go, pushing them around. But that, you know, creates other hazards, other places that you bring up some interesting problems that you wouldn't find unless you're doing one or two things, one, paying attention to your injury trends or near miss trends. Right. So what are people reporting? What's going on? And are you seeing clustering happening in a particular location, whether you have one [00:47:00] facility or multiple facilities? And then the other part would be paying attention to the surface in the maintenance process itself? Because, you know, how did you find out that the floor care machine was gummed up and not working as well? How long had it been there in that condition or how long had someone been using it in that condition thinking that they were cleaning the floor when it really wasn't working as well as it should have? Well, it starts smoking on you and blows up in one spot. They're typically gradual, like they're going to work really well. And then over time, it's going to be a reduction in the quality that for the surface that the machine leaves afterwards. And unless you're really paying attention, you're not going to see it. So I think there's a value in checklists and like, what are you paying attention to locally? And then your position kind of globally, overseeing safety for multiple areas is checking in on those spaces and seeing what's really happening [00:48:00] on the ground. And those are always going to be great indications that something's either working or something might not be working for you. Patrick Dooley: [00:48:08] Yeah, the biggest thing is really, you know, from an employer standpoint is to really encourage employees to report stuff. So the earlier that you report something, you know, the more data you're going to have. So we talk about what leading and lagging indicators, right. So lagging indicator. Someone's already fallen. Someone's gotten hurt. But the leading indicator as well, someone slipped there yesterday, but they got hurt today, but it wasn't reported yesterday, so we couldn't we didn't have the opportunity to take a look at that and fix it, you know, or what's the trend look like inside of a different store or stores that have similar flooring, similar fixtures. You know, what's the trend look like? How can we match those apples and apples and apples to oranges and figure out, you know, do [00:49:00] we need to pivot and make a change in how each fixture or the flooring in a different store? So, yeah, I think data is just absolutely necessary. Stuff doesn't get lost in data. If you're tracking the right things, you're going to be able to get ahead of a lot of different risks then you would have if you've didn’t, because you I think we've all heard it and especially with some of your policyholders and I've seen it in some of our buildings. Well, that spots been slippery for 10, 15 years. Right. Well, why don't you tell me for 10, 15 years ago, I would have fixed it and want to be slippery anymore. But yet over those 10, 15 years, how many different people have crossed that spot and had a little bit of a slip without a fall? But all it takes is that one person to have a catastrophic incident. And everyone says, well, I knew about it 15 years ago so. Peter Koch: [00:49:57] And then you scratch your head and why didn’t you tell me, why don't you tell [00:50:00] me? And I think that's a whole other podcast. Like, why don't people say something? That's a whole other topic. But it's really important. And that culture of employees being able to have a conversation with the safety guy or gal or the supervisor or the manager about some of those things is really important. Like you said, it's critical and then not forgoing that information, like following up on that information, because I would expect that this is my experience, because I've had that same thing happen to me where you go to someplace, you're investigating a big slip trip and fall injury that happened and you talk to the employees and they say the same thing. Oh, yeah, it's been like that forever. Well, how come you didn't say anything? Patrick Dooley: [00:50:45] Absolutely. And the thing is, like as a safety professional, I think one of the biggest misconceptions that people have, especially if you look at people from an employee perspective, a safety professional isn't just a [00:51:00] pocket protector and a clipboard. You know, we're there to really help and do things and have the conversations and learn about your job. And we're excited to learn about your job. Right. So if there's challenges in flooring, if there's challenges in your how you do your work, well, we just want to know about that so that it's not nothing that's negative. It's all positive. And that's kind of the environment we live in now. But 10, 15 years ago, I don't think the safety professionals kind of looked like they were clipboards and pocket protector people and telling people no, whereas now we're like, no, but the risk of doing it is this. And the risk of not doing it is that. So there's a nice conversation that happens. And that's kind of how we landed on, you know, some of the different things that we've done inside of our store reverbs. It was a conversation that just didn't happen. So now those conversations do happen. And I think we all land [00:52:00] in a great spot and we have less things to do. And in the end run, Peter Koch: [00:52:03] That's pretty cool. So we're coming towards the end of the podcast here. Do you have any recommendations for companies or maybe a safety person at a company that's looking to do some refurbishment, that's looking to do some floor replacement or maybe even creating their own floor care and maintenance plan? Any recommendations? Patrick Dooley: [00:52:26] Yeah, I have a few. I mean, if we're looking at specifically with flooring, so know your environment. Right. So select flooring materials that that match that environment. So when you build and expand remodel facilities, make sure this little resistance meets that environment, know what the out of box stuff is. So if you're purchasing something at a Home Depot, it may not be the best thing you may have to really look at the literature that comes along with it specifications and say, is this the best flooring? Make sure your floor care and maintenance programs are up to speed. Make sure whatever you're using matches [00:53:00] the flooring material that is laid. So even mopping is great, but some flooring and says don't mop with detergents and cleaning products. It could just be water and rinse off and or people think floor care machinery you're cleaning, it's meant to clean. It doesn't need that. Machinery does not need to be cleaned. Right. So there is a preventative maintenance program for that piece of machinery. So make sure that's up to speed. Yeah. You use a dirty old mop, you put in dirty old water back on the dirty old floor, right? Peter Koch: [00:53:35] And you know, that's a topic we didn't even get into today and which has its own nuances. The cleaning the floor itself. And you alluded to a little bit with the calcium chloride, but the product that you choose, how you apply the product, how it interacts with the floor, there are some subtleties there that not everybody knows. And, you know that old rule of thumb, that more is better is not always where [00:54:00] you want to go when you're trying to clean your floor. Patrick Dooley: [00:54:02] Yeah, right. I mean, a bottle of old English is not going to work on a tile floor, right? Peter Koch: [00:54:06] No, not at all. Patrick Dooley: [00:54:08] I mean, you really have to match the cleaning product to the flooring and what's coming in. So, you know, the calcium chloride. It's a tough thing to clean. So you want to make sure you're matching the cleaning product to what the environment is, as long as it matches, as long as the manufacturer's recommendations are match as well. The other couple of things would be like make sure your MAP program is part of your floor care maintenance program. So that would include like any of your runners. And I would also expand even further to like if you have rugs in the facility, you take a look at your rugs. Is the age of deterioration of certain areas of your rugs pretty sorry? So do they need to be replaced? Do they need to be repaired? Those are things to think about. And maybe is that the right product for that type of area when you go to replace it? And then, you know, I think we just touched upon it regularly [00:55:00] review your incident reports, you know, what is happening, what are the trends? Are there things that are happening that you can't anticipate? Encourage near miss reporting? Get that leading indicator in there. Make your employees report those near misses. It may seem laborious at first because I think what ends up happening is we encourage all this leading indicator stuff and you get a ton of reports. But they're significant. They're significant to the person reporting it. So let's pay attention to it and chart it and map it and put the data to it. And then finally, from a floor care maintenance program and an employee thing, make sure folks are trained in just cleaning up spills like a from our standpoint, we have a retail store. We don't have a janitorial staff on site all the time. So they're trained in how to clean up spills, make sure that if you do have [00:56:00] a custodial staff that they're trained and respond to spills appropriately. I think those probably would hit the big beats. Peter Koch: [00:56:09] Yeah, I think so, too. And that last point is very interesting. You know, you would think that cleaning up a spill is a skill set that everyone should have. I mean, all of us here. And if you're not raising your hand, you're lying. All of us here have spilled something. Doesn't matter if it's a glass of milk, glass of water, whatever, that something has spilled and you've cleaned it up at home. Great. But in the workplace, you might not be dealing with it. Like how many of us have actually spilled something, maybe off the stove that's a little greasy and you're using an off the shelf cleaner to clean that up? And how many of us have gone back to that spot? And it's still a little greasy. It's not as clean as it should be because we might not have used the right cleaner. We hadn't had the skill set or the training. [00:57:00] So making sure that your staff, who aren't your custodial staff, have some understanding of what they should be using to clean up the potential things that they're going to encounter when they're in their workplace. And then your custodial staff needs to have another whole level of training so that they can deal with anything that comes in and understanding the products and understanding the process, understanding the potential risks of using this the wrong way. Understanding limitations, I think is huge. Patrick Dooley: [00:57:28] Right. And use and use things like the yellow, floors wet signs everywhere. Right. But if they're not used appropriately, it can actually create a hazard. Right. Because now you have people that are anticipating perceive a slip, trip or fall and there isn't. So they've changed their gait, they change their stride and now they're actually tripping. Because they're their perception is changed. So, you know, making sure that things that you do [00:58:00] are in line with the environment, what they need to be doing it use them appropriately. And I guess that's the key. Peter Koch: [00:58:07] One last thing I kind of want to end on here, and you said it as the second to last thing of the recommendations, reporting those near misses and especially for slips and falls. That's huge. So, you know, you've got the ability to map things. Everyone has it. If you're working in a space, you have a facility. And even if you can't draw, you can still draw a box with a couple of places where things are in your facility, so you think about all that data that you have, sorry, do you encourage people to talk about their near misses? And in a month, out of the 10 employees that you have, you have 50 near misses, one that should tell you that there's a problem inherent there. But two, what are you going to do with all that data? Well, you might not have to respond to everyone individually at first, but maybe take that data and at least put those near misses on the map and then see where they cluster. And that can open your eyes [00:59:00] to, hey, maybe we need to look more in that area, because out of those fifty twenty-seven of those reports were in this particular area. So then you can look at what's your floor care process there? What's the flooring there, what does it look like, what's the condition, what's the kind, what are the changes all of those parts for then you as the owner of the business, if you're a small company or if you have a safety person, maybe they can be the person that goes to do a little more investigating so that that mapping process as a hugely powerful tool with those lagging indicators and in even the leading indicators. So you flip it around and start looking at the hazards that are out there in your facilities, inspection and mapping those. Patrick Dooley: [00:59:41] And just communicating back to the person that did report it. So you have to because you want to make sure that you encourage the effort to put that in and you want them to do it again. Even if it's insignificant. But that's just a data point that you have and you could utilize [01:00:00] in the future. And, you know, I tell folks all the time, I encourage them to report anything. You know, I'd rather see my email flooded. Then no have one email at all. Peter Koch: [01:00:13] Because, you know, if you get one email, it's going to be that email. Patrick Dooley: [01:00:18] Right. And, you know, and if someone took the time to report it, it's an important it's important enough to them that I should respond and make sure that they know that we're going to work on we're going to take a look at it, that it's not just a data point. That is something that we encourage. And, you know, it leads into other things in the long run. Peter Koch: [01:00:39] Yeah, encouraging that communication, Patrick Dooley: [01:00:42] Leading indicators are just huge. And I think, you know, majority of safety professionals and in the environments we work in that we don't see enough of them. They're hard to judge. They're hard to go by. But they play a huge role in how you determine how [01:01:00] we lower risk in certain different areas and different areas of our business. So, yeah, Peter Koch: [01:01:05] And it's that one cool thing. You know, if you think about all the rest of the measurements that we have in business and most of the measurements we have in business are lagging indicators. It's the measurement of your income versus outflow for the monetary side of your business. How many employees do you have this month versus last month? Most of those are lagging because you're looking at a report of something that happened historically where the leading indicators are its information right now. It's that dashboard of real time information that it's enormously helpful from a safety standpoint because there's a human factor about it. Like to be able to respond in kind in time with something that's coming from another person is huge for your culture. Patrick Dooley: [01:01:56] Yeah. I mean, literally, the lagging indicators are the last thing that a safety person [01:02:00] wants to talk about. The Debbie Downer of a meeting. Right. I mean, you're going into a meeting and you're talking about things that have already happened, the cost to the company. You know, the things that happened to me, G.L standpoint, comp standpoint. I don't want to talk about it. I want to talk about. No, here's the things that we've done that we reported ahead of time. And these are the things that we fixed. So that way we're not injuring someone or we're not having an incident with a vehicle or PPT like this is what's happening because we're able to have these leading indicators. And I'm not standing here and talking about, you know, someone being injured because someone didn’t, you know, take the grease off the floor. Peter Koch: [01:02:37] So that's cool. And all about kind of understanding the surface. I mean, that's what we started with today is, you know, talking about slips and falls. And there's lots of things that go into the puzzle of preventing slip and fall events. But really, where to start is understanding your service, how people interact with it, what goes on it, how it's cleaned, your maintenance program, all that stuff. Understanding the surface really gives you the best [01:03:00] idea of how to manage the other things that go towards preventing slips and falls. So that's pretty cool. And really, we've now hit the end of the podcast here today. And I really appreciate you spending some time with us, Patrick, and sharing your expertise and your experience with us. So thank you for that. Patrick Dooley: [01:03:19] I thank you for having me. And this has been great. And now I look forward to working with MEMIC and some of your policyholder's in the future. Peter Koch: [01:03:28] Yeah, I hope so. That'll be great. We will have you on again, and there's you know, like we talked about at the beginning, L.L. Bean is multifaceted when it comes to the different industries or the different safety aspects that are involved with L.L. Bean. So I'm sure we'll have you on again. Maybe we can talk fall protection or we can talk personal protective equipment or something else would be kind of cool to have a chat about. Patrick Dooley: [01:03:50] Awesome. I look forward to it, Peter. Peter Koch: [01:03:52] Very good. Well, thanks again for joining us. And to all of our listeners out there, appreciate your listening today. Today on the MEMIC Safety Experts podcast, [01:04:00] we've been speaking about slip and fall prevention with Patrick Dooley, CSP and senior environmental health and safety specialist with L.L. Bean. If you have any questions or I'd like to hear more about a particular topic on our podcast, e-mail me at [email protected]. Also, check out our show notes at MEMIC.com/podcast, where you can find additional resources, links to other podcasts, as well as the entire podcast archive. And while you're there, sign up for our Safety Net blog so you never miss any of our articles or safety news updates. And if you haven't done so already, I'd appreciate it if you took a minute or two to review us on Stitcher, iTunes or whichever podcast service that you found us on and subscribe. And if you've already done that, well, thanks, because it really helps us spread the word. Please consider sharing this show with a business associate friend or family member who you think will get something out of it. And as always, thank you for the continued support. And until next time, this is Peter Kotch reminding you that listening [01:05:00] to the MEMIC Safety Experts podcast is good but using what you learned here is even better.